Recent advances in robotic programming have reduced the implementation time of robotic automation to a point where even small and medium sized manufacturers with high-mix, low-volume production can get a robotic packaging application up and running in just a few hours
How to Successfully Automate Packaging in Low-volume, High-mix Production
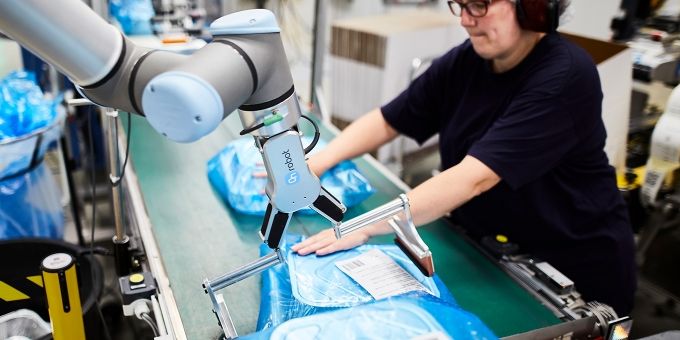
Article from | OnRobot
Your competitors are either considering robotic packaging automation, or they have already implemented it. 83 % of respondents in the McKinsey Global Industrial Robotics Survey said they were likely to or had already implemented robotic packaging applications.
Robotic packaging automation can increase production throughput, reduce costs, inconsistencies in the packaging process, and the risk of injuries on the packaging line. However, the high initial investment with an ROI a long way into the future and a daunting implementation process put off many small and medium sized manufacturers.
However, recent advances in robotic programming technology have reduced the implementation time of robotic automation to a point where even small and medium sized manufacturers with high-mix, low-volume production can get a robotic packaging application up and running in just a few hours, earning back that investment in record time - if you plan your robotic packaging automation right, of course.
Here is what you need to consider when planning your robotic packaging automation solution:
1. Questions to ask yourself before investing in robotic packaging
- What is your budget, and how cost-effective is the robotic packaging solution?
- What is your required production throughput per day?
- How consistent is the size, shape and weight of the production units?
- How consistent are the package size and packaging patterns?
- How much floor space is available for the packaging application?
- How much time are you willing to spend on deployment and redeployment?
- What are your plans for up- or downscaling production?
- With which other systems do you need to integrate the robotic packaging application?
Cost-effectiveness
Assess the initial investment cost of the robotic system, including the robotic hardware, extra equipment such as vision cameras and grippers, programming, and integration expenses. When considering the return on investment (ROI), remember to factor in the implementation time, long-term expenses to maintenance, support and training as well as positive factors such as labor savings, increased productivity, reduced errors, and overall operational efficiency.
Flexibility and adaptability
In low-volume, high-mix production, flexible and easily adaptable robotic applications are essential to successful packaging automation. Consider the ability of the robotic solution to handle a variety of packaging tasks, package sizes, shapes, and materials. Look for easy reprogramming capabilities, quick changeovers, and compatibility with different packaging formats to accommodate changing production needs.
Scalability
Choose a robotic solution that can scale with the business as it expands, allowing for the addition of more robotic applications and increased capabilities. Scalability is essential to accommodate future changes in production volume or product lines.
Ease of use and programming
Look for intuitive programming interfaces, easy-to-understand controls, and straightforward integration with existing processes. The more user-friendly the solution and the more automated the programming, the faster you can deploy and redeploy the robotic packaging application with minimal training required.
Safety considerations
Assess which safety features are needed, especially if the robotic application needs to work in proximity to human operators. Collaborative robots (also known as cobots) are designed specifically for safe human-robot interaction, whereas traditional and light industrial robots require physical barriers or additional safety measures.
Technical support and maintenance
Consider the availability and quality of technical support and maintenance services provided by the robot manufacturer or supplier. Ensure that there is prompt assistance in case of issues or breakdowns to minimize downtime and keep the packaging process running smoothly.
Space requirements
How much floor space is available in the manufacturing facility? Robots that require safety fencing have a larger footprint than collaborative robots, which can work safely next to humans. So make sure to choose robotic hardware that fits within the allocated space without hindering other operations or workflows.
Integration with existing systems
Assess the compatibility of the robotic packaging solution with your existing systems, such as production lines, conveyors, or warehouse management systems. Seamless integration can streamline operations and optimize overall efficiency.
Training and skill requirements
Consider to what extent training and upskilling of your staff are necessary to deploy, operate, redeploy and maintain the robotic packaging application.
Cut down deployment time by 80% with D:PLOY
In the past, we would have recommended you choose a collaborative robotic packaging solution for its easier programming. But thanks to D:PLOY, OnRobot’s groundbreaking automatic programming platform, you can now deploy light industrial as well as collaborative robotic packaging applications in less than a day. And you can redeploy them for new applications in under two hours.
Comparison of first deployments of Packaging applications with conventional programming and D:PLOY Packaging
In our test, the first deployment of the packaging application went from taking 2.5 days to 4 hours with D:PLOY.
Time-saving on redeploying Packaging applications with D:PLOY Packaging for changes in production items, positions or locations.
The redeployment for a new packaging application, which took 1.5 days with conventional programming, took only 1.5 hours with D:PLOY.
2. How to design your packaging application
Determine your pick-up strategy
Robotic packaging is a type of material handling or pick and place application. This means the robot arm must pick up the work item from the same position every time. The items are then placed in a container in a predetermined pattern.
In most cases, the work items are transported on a conveyor belt. To ensure that the robot can pick up the item, the item can either be stopped at the end of the conveyor belt, or a vision system can communicate the location of the items to the robot arm.
Choose your robotic hardware
As explained above, for low-volume, high-mix manufacturing you should look for a robotic packaging solution that offers flexibility, quick changeovers, and easy programming.
That means you can either choose a light industrial robot or a collaborative robot. The main differences are that light industrial robots can handle higher payloads, whereas collaborative robots can work safely alongside human operators.
Consider the payload, speed, footprint, and safety of the robot arm. Also consider how well the robot integrates with your existing systems. OnRobot’s no-code deployment platform, D:PLOY, takes care of most of the actual integration programming so you can deploy and redeploy the packaging application in just a few hours with no prior programming experience.
3. Choose the most suitable end effectors for your packaged products
The style of end effectors or grippers is determined by the size, weight, shape, fragility, and surface qualities of the work item you wish to package.
Perhaps you need a food grade certified gripper or a gripper for particularly delicate items such as glass. Or you may need a gripper that can easily pick up work items of different sizes or shapes.
Choose from a wide range of robot arm grippers such as: magnetic gripper, finger grippers (or jaw grippers), vacuum grippers, gecko grippers, and soft silicone grippers.
D:PLOY seamlessly manages the programming of the end of arm tools for the robotic packaging application.
See which end of arm tools we recommend for material handling applications
Sources:
1. Ajewole, Femi, Ani Kelkar, Dylan Moore, Emily Shao, and Manju Thirtha: Unlocking the industrial potential of robotics and automation. McKinsey & Company, 6 January 2023. https://www.mckinsey.com/industries/industrials-and-electronics/our-insights/unlocking-the-industrial-potential-of-robotics-and-automation#/
The content & opinions in this article are the author’s and do not necessarily represent the views of RoboticsTomorrow
Comments (0)
This post does not have any comments. Be the first to leave a comment below.
Featured Product
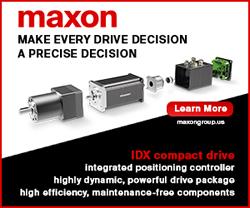