In recent years, the need for a mini ball screws has become more evident through conversations with our customers and feedback from the marketplace. Specifically, the rising demand is for high-quality ball screws that are made in the U.S and available from stock.
Key Factors for Ball Screw Applications
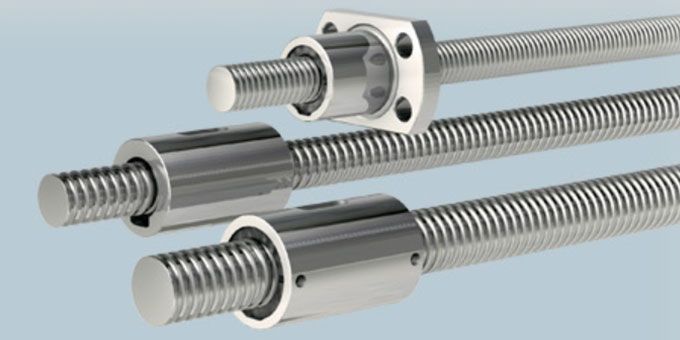
Article from | PCB Linear
Why Ball Screws?
In recent years, the need for a mini ball screws has become more evident through conversations with our customers and feedback from the marketplace. Specifically, the rising demand is for high-quality ball screws that are made in the U.S and available from stock. In response, PBC Linear has answered that call with a six, eight and ten millimeter diameter line of ball screws.
PBC Linear is targeting applications in the medical, lab automation, and semiconductor industries. As Tim Stellmacher states, "These are some of the industries that we believe are going to be hot, with many of the robots that facilitate automation requiring miniature ball screws."
Ball Screw Precision and Accuracy
Within the industry, there can be some confusion on terminology when discussing accuracy and precision. Often, customers refer to those as being interchangeable, but they’re not. They are actually two separate terms that are used to define ball screws and how they're used in an application.
Accuracy is defined by the the screw, and can reflect how it was manufactured. For example, was it rolled or ground? Accuracy is comparable to throwing a dart toward the center and hitting the bullseye. On the other hand, precision defines the nut, and is the repeatability or how often the system hits the intended target.
Ball Screw Orientation
Another factor that engineers tend to forget about is ball screw orientation. Ball screws are designed to perform best when their loads are in the axial position. The reason is that there is usually a profile rail, linear bearing, or rail that is supporting the load while the ball screw itself is doing the motion.
Once that system is turned vertical, the load direction becomes one-unit directional with the forces completely downward. That has multiple effects on the design of the system, including how the ball screw wears during movement in both speed and acceleration. As the device moves up and down, the speed and deceleration adds extra load to the system. The result can be an implied impact load at the bottom, so reversing the load becomes critical to the design of the system.
Ball Screw Speed and Acceleration
Speed is another critical factor, but is best broken down into two parts: ball nut speed and screw speed. The first part applies to the screw itself, and refers to how fast the screw will spin. The length of the screw will often define the limits of screw speed. For example, the longer a screw is, the more vibration is possible. Vibration in the system will lead to corrosion and reduced life. Many designers want loads to move as fast as possible in order to reach the desired position as quickly as possible. Unfortunately, there are limitations with the screw that must be addressed.
The second part of critical speed applies to the nut. Here, critical speed refers to how fast the nut can spin within the limits of the return system, and reflects how fast the internal ball bearings recirculate. Miniature metric screw assemblies from PBC Linear have an internal return that is very smooth, quiet, and capable of higher nut speeds.
Ball Screw Duty Cycles
A duty cycle by itself is not overly critical. Usually it lends itself more into a discussion on screw life, which can get extremely complicated when considering a move profile. A move profile is typically a trapezoidal looking movement where there’s the initial acceleration, then constant motion, and finally deceleration. While these are all very critical, acceleration is one of those items that is typically disregarded. In fact, trying to find ball screw acceleration limitations in reference materials is extremely challenging, so it is often limited to a standard one-and-a-half G’s. That number is more of a guideline because actual max speeds, acceleration and deceleration are really application-based and often need to be defined through experimentation.
One of the great things about ball screws is their defined life. International standards clarify how we define the life of a ball screw. For metrics, it's usually a function of a million revolutions, which is our L10 life and where statistically 90% of ball screws are going to achieve this life. In reality, they may reach much more, but now there is an established minimum value.
Ball Screw Travel
With miniature ball screws, there are a couple different factors related to travel. In short travel scenarios of one or two-millimeters, difficulties arise because the balls are not fully recirculating within the nut. Defining ball screw life under these circumstances along with the design and function of the return system will play a critical role on how that's going to perform. For example, a fluid pump requires extremely short travel range of 10 to 100 millimeters. That last one millimeter of travel will experience the most force, creating possible issues when it comes to defining ball screw life.
Long travel applications can create problems as well. For example, as a six-millimeter ball screw travels one meter, critical speed and prevention of sag become important factors. So between the extreme short and long travel lies the travel middle, or the sweet spot where 100 to 200 millimeters of travel is ideal for these types of screws to best function.
Ball Screw Load Capacites
Ball screws are designed to be loaded 100% axially. If done correctly, the ball screw will last its L10 life. Often when ball screws fail, there’s a deformation of the screw and nut resulting from a load that wasn't properly aligned. A radial load or a moment load on a ball screw can impact that L10 life by dropping the load capacity over 90%. The lesson here is, if there are design calculations in a catalog that recommend a parallel support structure within a specific parameter, it is critical to adhere to that guideline.
The content & opinions in this article are the author’s and do not necessarily represent the views of RoboticsTomorrow
Comments (0)
This post does not have any comments. Be the first to leave a comment below.
Featured Product
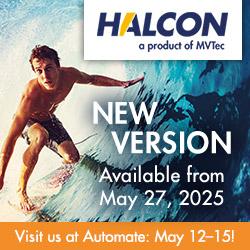