Warehouse automation isn’t brand new, and many units have some degree of automation integrated. The next step, and the key to ultimate efficiency, is to fully automate warehouse logistics.
End to End Automation Will Be Essential to Meet Changing Demands
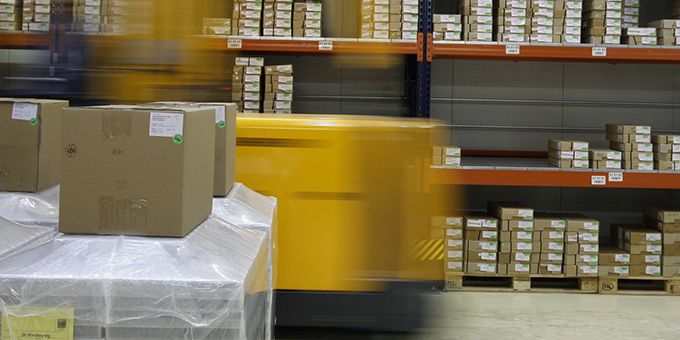
Dave Walsha, sales manager | EMS
According to the National Office for Statistics, online orders accounted for one in four UK retail sales in August 2021. E-commerce is growing, and warehouse facilities must adapt to keep up with rising demand. Here Dave Walsha, sales manager at precision drive system supplier EMS, explores the role automation will play in the future of the warehouse industry.
Restrictions put in place to control the spread of COVID-19 changed the shopping habits of the UK. According to data by YouGov, over half of Brits are more likely to buy clothes online now than they were before the pandemic. The events of the past 18 months have catalysed a shift to a digital world, and has likely changed shopping habits forever.
High demands
The rise of online shopping has had a significant impact on warehousing and logistics. For instance, a 2021 report by real estate company Savills found that online retailers have increased warehouse occupancy by 614 per cent.
It’s not just the volume of online orders that’s affecting the warehouse industry. Consumers are coming to expect express services and next day delivery options as standard. In fact, further data from McKinsey and Company found that 46 per cent of online shoppers abandoned shopping carts online if shipping times were too long or not provided.
To keep up with an influx of online orders and rising consumer expectations, warehouse managers must prioritise efficiency. In addition, with the UK facing a potential supply chain crisis, facility productivity will play an important role in keeping shelves stocked.
While increasing warehouse floor area and hiring new employees can help improve productivity, change can be slow. For instance, according to The World Bank, the average time required to build a warehouse in the UK is 86 days. In addition, many warehouse managers are struggling to hire personnel due to the current UK warehouse worker shortage.
The final piece of the puzzle
Therefore to increase warehouse productivity in line with rising online orders, warehouse managers should focus on accelerating their automation journey. Warehouse automation isn’t brand new, and many units have some degree of automation integrated. The next step, and the key to ultimate efficiency, is to fully automate warehouse logistics.
The development of robots that can successfully load and unload lorries are providing the final piece of the puzzle, making complete warehouse automation possible. Lorry loading and unloading has previously been a difficult step to automate. One reason for this is that artificial vision systems can have difficulty distinguishing where one box begins and another ends in a crowded trailer.
In addition, a robot may find it hard to rummage through a jumble of boxes if they have fallen over in transit, or to pick up an object with a complex shape. There’s also the varying weights and sizes of cargo that the robot must contend with. It must have the ability to forcefully lift something heavy and delicately handle a fragile package.
Lights out
A warehouse unit with end to end automation can become a lights out facility ― where human workers are not constantly needed to maintain productivity, and can therefore warehouses can often operate in complete darkness. Dark warehouses are the epitome of efficiency, with many automated machines working together in perfect harmony.
For instance, a logistics robot can receive an online order and move automatically to a storage rack to collect the relevant item. The item can then be deposited onto an autonomous vehicle or conveyer belt to be moved around the warehouse to the packing station.
Here, an automated packaging machine can use sensors to detect the dimensions of the object, and then pack it into an appropriately sized box made from a carboard sheet — the machine uses small levers and paddles to fold the sheet into a box. The parcel is then transported to the shipment area, where it’s loaded onto a lorry for delivery.
Magnificent motors
Enter an automated warehouse and you’ll be surrounded by a flurry of robots that appear to be running the facility. However, the true driving force of an automated warehouse is the powering motors — and they must meet stringent requirements.
The motors need to be compact so the automated machine can fit into tight spaces between racks. Low weight is another important requirement of the motors, allowing the robot to make quick and agile movements. The motors must also exhibit high power so that the automated machines can move heavy cargo.
EMS is the sole UK supplier of FAULHABER motors, which are renowned for their unbeatable power to weight ratio. In particular, the BXT series can deliver torque up to 134 millinewton metres (mNm) thanks to its innovative winding technology. The multi-pole brushless motors are available in lengths as small as 14 millimetres, making them ideal for robots with small space requirements.
Online shopping is increasing in popularity, and warehouses must evolve to meet new demands. End to end automation allows warehouse managers to increase unit productivity without the need for additional floor space or employees ― accelerating a package’s journey from warehouse floor to customer door.
The content & opinions in this article are the author’s and do not necessarily represent the views of RoboticsTomorrow
Comments (0)
This post does not have any comments. Be the first to leave a comment below.
Featured Product
