Through regular and thorough inspections, faults, wear and tear, and defects can be detected at an early stage and proactively acted upon, thus preventing production downtimes.
Automating Industrial Inspection With Autonomous Mobile Robots
Article from | Energy Robotics
Good maintenance and regular inspections are the be-all and end-all of smooth operation - this applies to one-man businesses as well as large corporations. Through regular and thorough inspections, faults, wear and tear, and defects can be detected at an early stage and proactively acted upon, thus preventing production downtimes. This not only increases safety in operations, but also saves time and money. On the one hand, such inspections are routine tasks, but on the other they require the highest degree of accuracy, consistency and reliability in order to meet safety, environmental and performance standards. And they are time-consuming, especially in sprawling industrial facilities, which means that staff resources are tied up to a great extent. Against the backdrop of an increasing shortage of skilled workers in the coming years, new solutions are needed. This is where automated inspection through autonomous mobile robots come into play.
ROBOTS: NOT JUST TOOLS, BUT INSPECTION TEAMMATES
The demographic figures for the coming years paint a bleak picture: with the baby boomers entering retirement age, about a third of the workforce will retire by 2030, according to Forbes. According to a survey by the VDMA, it is mainly experts such as engineers (78 percent) whose labour and experience will be lost in the future. This poses major challenges for industrial companies, because without adequately trained personnel they are hardly in a position to reliably maintain regular inspection routines. Automated inspection solutions can help here, but these must either be introduced in the company from scratch or integrated into already existing systems. Companies are therefore dependent on holistic solutions that can be rolled out seamlessly and are ready for use within a very short period of time. Digital solutions solely based on IoT sensors provide limited relief. The reason: In addition to the very expensive sensor technology, investments must be made in a corresponding IoT network infrastructure for the energy supply and transmission of data. Furthermore, these IoT sensors will also have to be monitored regularly.
.jpg)
A single robot can read numerous devices and inspect every corner of an industrial plant.
The more cost-efficient alternative for consistent and reliable asset monitoring: autonomous inspection via mobile robots. Robots equipped with the appropriate software and sensor technology are able to perform predefined inspection rounds completely autonomously, collecting high quality data and delivering actionable information. Instead of having to equip an entire industrial plant with hundreds or thousands of new digital sensors, companies benefit here from the robot as a mobile sensor centre. This way, industries are able to maintain high-quality inspection cycles and at the same time relieve employees of repetitive and therefore error-prone tasks, while also preventing them from being deployed in potentially harmful working environments.
END-TO-END SOLUTION FOR AUTONOMOUS ROBOTIC INSPECTION
The core of an automated robotic inspection solution is a software platform that combines three essential components to deliver value to asset owners immediately. A hardware-independent robot control system provides the flexibility needed in the selection of robots to find exactly the right hardware for each asset owner's individual use case. Cloud-based fleet management allows companies to keep track and control a mixed fleet of different inspection robots simultaneously -both on-site and remotely. AI-driven data analysis for industrial inspection tasks ultimately ensures that the robot not only collects inspection data, but also analyses it and converts it into actionable information for asset owners.
The robots, which are equipped with cameras and all necessary sensors, are first trained manually by guiding them to all relevant inspection points along the inspection round. These points are named in the user interface, saved and, in some instances, stored with target values. The operator can then select the inspection points to be monitored by clicking on the points in the Digital Twin (or 3D map) of the site. Once the points or assets are selected on the site-centric user interface, the robot autonomously moves through the site and collects information from these points. Asset monitoring is literally at the fingertips of operators with the latest feature, Click & Inspect. While executing the inspection round, the robot reads the values of the predefined measuring points, analyses the data through AI driven skills, and delivers actionable information to asset owners via an encrypted connection.
Let’s take the use-case of monitoring pressure by reading manometers as a brief practical example. As the image of the manometer would still require a human to read the actual value, the robot not only reads the manometer through our AI skill, but it also forwards the reading with a recommendation for action to the responsible employee. If the value exceeds a critical level, for example, the robot sends an alarm signal to the operator so that he or she can react accordingly.
For even more efficient use, the inspection environment is coupled with a Digital Twin, or 3D map of the site. The user thus benefits from manual command input in order to examine certain inspection points in higher detail. The robot then automatically finds its way there and executes on-demand inspection tasks. A major advantage here is that in the event of a malfunction, workers could move the robot remotely to the point to be inspected and receive critical information of the situation via the sensors and cameras. In this way, mobile robots also protect workers from challenging situations such as adverse weather conditions and from staying in the plant during a potentially dangerous situation.
WHAT NEEDS TO BE TAKEN INTO ACCOUNT WHILE SELECTING A ROBOT?
Given the expansive scope of inspection tasks in different environments, there is no standard one-size-fits-all solution when it comes robots. Every industrial plant is designed differently and therefore has individual needs and different requirements for an autonomous robotic inspection solution - especially with regard to the hardware used. Industries are therefore well advised to take a close look at the site’s infrastructure as well as the existing manual inspection routes before deciding on and implementing an automated inspection solution. These routes are usually designed with humans in mind, therefore industries should make the choice of robot accordingly.
In case of multi-floored facilities where inspection rounds consist of flights of stairs, four-legged walking robots, such as Spot from Boston Dynamics, are a good choice. If, on the other hand, industries consist of potentially explosive ATEX and IECEx zones that need to be monitored, then spark-proof robots that are specially certified for such environments, such as the ExR-2 from ExRobotics, should be used. And if there are inspection points that can only be reached via a ladder or are beyond camera range, then drones are a useful addition to the inspection robot fleet. The hardware-agnostic inspection solution from Energy Robotics allows asset owners to onboard a mixed fleet of different robots adapted to specific environments and tasks, and control all of them through a single platform.
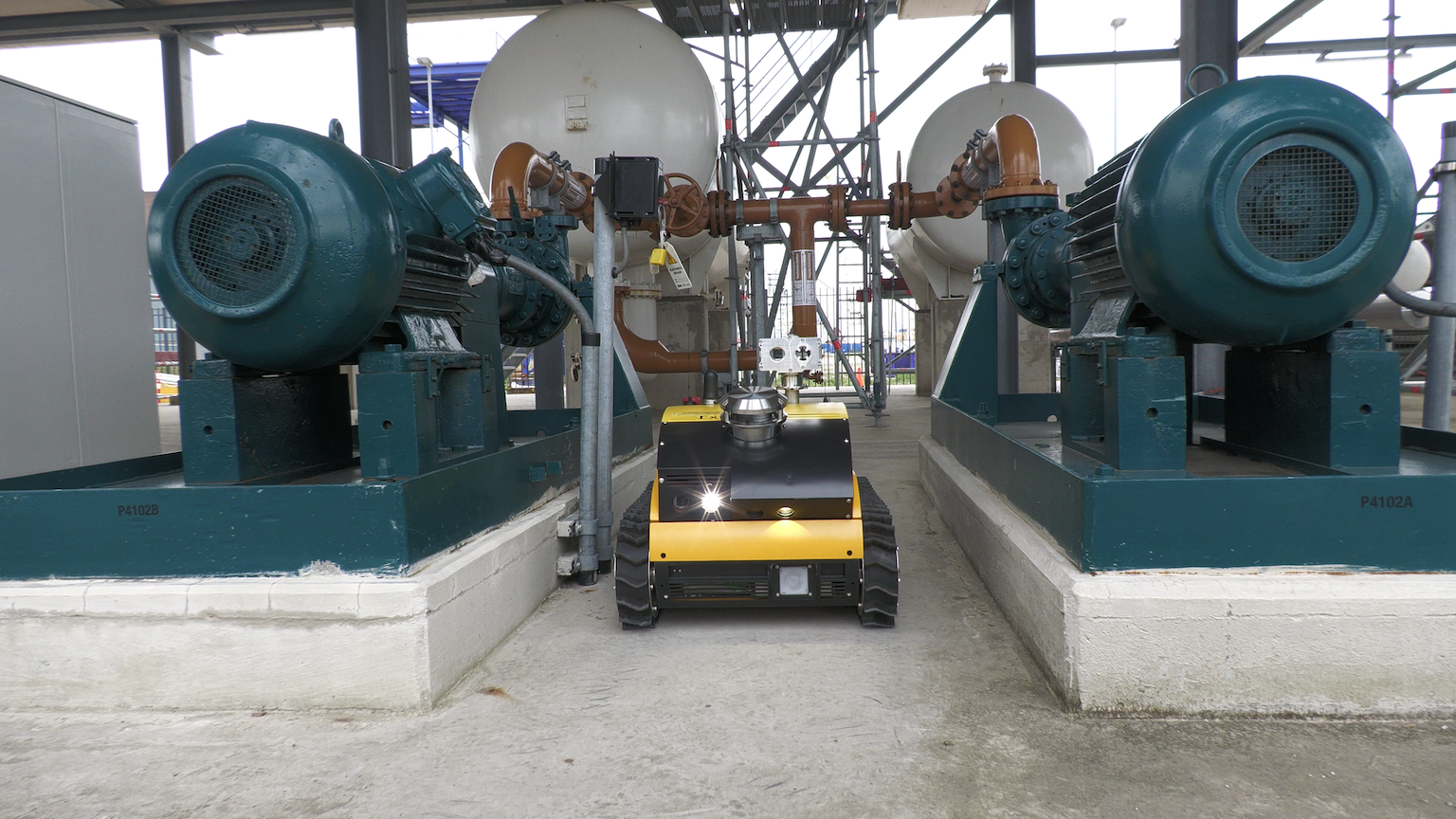
The ExR-2 from ExRobotics is ideal for monitoring ATEX or IECEx Zone 1 areas
Not only the robot itself, but also the sensor technology used must be adapted to the asset owner's individual application. Optical cameras enable the robot to read displays and measuring instruments, whereas thermal imaging cameras can detect defects in pipes and temperature levels. The collected data can be used to detect anomalies such as excessive temperature, leaks or contamination at an early stage. Additionally, flow rates and pressure values can also be read out. Sensors, for example to detect gas or other sensitive substances, ensure that leaks of hazardous substances are detected at an early stage.
THE FUTURE OF INSPECTION IS MOBILE AND AUTONOMOUS
Higher process efficiency with reduced downtimes, greater occupational safety and intelligent data analysis - these are all strong arguments for the use of autonomous robotic inspection solutions in industrial plants. Autonomous robots perform inspection tasks reliably and with consistent quality in demanding environments and record all relevant data. They also harness the power of artificial intelligence and machine learning to analyse the acquired data and transform it into business-critical information. And for the employees, autonomous robots are a real blessing. Instead of pursuing dull and tedious tasks in environments that are hazardous to their health, employees can concentrate on other, more important and fulfilling tasks. This is the true value of industrial automation - and also how the concept of Industry 4.0 becomes real.
Article courtesy of Energy Robotics
The content & opinions in this article are the author’s and do not necessarily represent the views of RoboticsTomorrow
Comments (0)
This post does not have any comments. Be the first to leave a comment below.
Featured Product
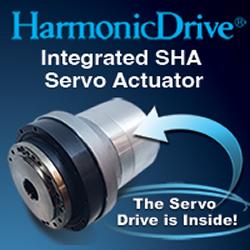