AMRs can pick up waste (scrap material, packaging, manufacturing by-products) from various points throughout the facility and automatically take it to the nearest waste disposal zone.
Article from | Milvus Robotics
One of the most appealing features of AMRs is their ability to complete various different tasks and navigate virtually any environment. They are flexible and adaptable – allowing for a wide variety of use cases in distribution centers, manufacturing facilities and warehouses. Here are some of the most common use cases for AMRs across a variety of industries.
Delivering Raw Materials
In manufacturing facilities, AMRs can move raw materials and components from the warehouse area to the desired location within the facility. They can be equipped with attachments allowing them to transport pallets, containers, shelves and more.
Work-In-Process Movement
Small, agile autonomous mobile robots are useful for moving packaging, materials, or partially-finished goods without getting in the way. This allows for consistent material flow in non-linear production jobs.
End of Line Handling
At the end of the line, AMRs can take finished goods from the factory floor to the next step in the process – whether that is QA, finished goods warehousing, or another location. They can automatically transport pallets from the palletizer to the stretch wrapper and to the shipping dock.
Transporting Waste Materials
AMRs can pick up waste (scrap material, packaging, manufacturing by-products) from various points throughout the facility and automatically take it to the nearest waste disposal zone.
Case Picking
AMRs can be employed to pick cases of a product in the desired quantity from a variety of storage mediums. This reduces the need for human labor in warehouses and distribution centers.
Transporting Picking Containers
AMRs can navigate narrow aisles to safely, autonomously transport picking containers and take them to the correct shipping lane.
Moving Packed Pallets
Heavy-duty robots can safely, securely move packed pallets from one point to the next. When equipped with lifting attachments, they can reduce the need for forklifts. This is particularly useful in areas where people are working and other equipment must be navigated, as forklifts are more likely to cause damage or injury.
Staging Loads for Shipping
AMRs have advanced sensing capabilities, allowing them to move with precision and stage loads for less-labor-intensive, more-efficient outbound logistics.
Delivering/Replenishing Empty Pallets
AMRs with pallet platforms are adept at delivering and replenishing empty pallets at the appropriate time so that pallets are always in the right place when they are needed.
Cross Docking or Dock-to-Aisle
With their sensing capabilities, maneuverability, and ability to work alongside people and other vehicles, AMRs can be used in shipping docks for cross-docking or dock-to-aisle material handling.
Long Haul Material Transport
AMRs can replace fork trucks or other vehicles as a safer method of long-haul transport in large facilities.
On-Demand Material Transport
While many of these use cases are autonomous and recurring, AMRs can also be used for custom, on-demand transport missions.
How Can Autonomous Mobile Robots Fit into Your Material Transport Workflow?
Milvus Robotics engineers are here to develop a solution that accomplishes your goals and facilitates safe, reliable, efficient material transport workflow. We offer a range of AMRs designed for different use cases and payloads, along with a variety of attachments so that you can customize your robots for pallet handling, lifting, delivering materials, moving shelves or containers, and more.
The content & opinions in this article are the author’s and do not necessarily represent the views of RoboticsTomorrow
Comments (0)
This post does not have any comments. Be the first to leave a comment below.
Featured Product
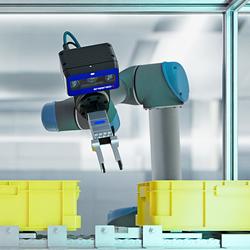