Preventing worker discomfort and addressing early signs of injury are proven to save companies time and money, all while improving worker satisfaction and reducing turnover.
Decrease Downtime: Ergonomic Process for Healthier, More Productive Workplace
Article from | Briotix Health
Worker discomfort is costing companies time and money.
According to research published by American Medical Association, workers with musculoskeletal pain lose an average of 5.5 hours of productive time every week costing companies billions of dollars each year. Surprisingly, most of the time lost (76.6%) is due to reduced work performance by employees experiencing physical discomfort, not absenteeism.
Preventing worker discomfort and addressing early signs of injury are proven to save companies time and money, all while improving worker satisfaction and reducing turnover. By using an ergonomic process, you can identify and alleviate the ergonomic risk factors present in your workplace to:
- Safeguard Your Workforce: Protect employees from injuries and ensure a safe work environment.
- Boost Productivity: Increase efficiency and reduce downtime with ergonomic equipment and a safe work setting.
- Reduce Turnover: Enhance morale and satisfaction by prioritizing comfort, safety, and well-being.
- Reduce Costs: Lower expenses related to work injuries and lost time.
What are the five most important steps to identify and address ergonomic risk factors in the workplace?
These five steps are the playbook for your success to identify and address ergonomic risk factors in your workplace.
- Conduct a workplace analysis
- Evaluate work postures, movements, and forces
- Review workers’ feedback and complaints
- Develop and implement control measures
- Monitor the effectiveness of the control measures
These measures can help cultivate a work environment that prioritizes occupational safety and productivity for you and your coworkers. Let's take a deeper look at each of these steps.
(1) Conduct a workplace analysis
This step involves reviewing the work environment to identify repetitive tasks and work activity that may pose greater ergonomic risks. In this first step, you will be looking at the physical and organizational characteristics of the work environment, such as the layout of the workspace, lighting, temperature, noise, and pace of work.
Review workers’ compensation claims, incident and injury reports
- Worker's compensation claims can provide valuable information on the types of injuries workers are experiencing and the tasks and activities associated with those injuries. By delving into incident and injury reports, you can discover additional trends and patterns that may reveal areas of concern. This can allow you to zero in on specific tasks and activities that pose potential ergonomic risks and address them before they become major problems. With a little detective work, you can help create a safer, healthier, and more ergonomic workplace.
Survey workers
- Unlock valuable information about potential ergonomic risks by surveying workers and exploring their experiences and concerns. By asking the right questions, you can uncover critical details about tasks and activities that may be causing frustration, discomfort, or pain, giving you the information needed to address inefficiencies and potential.
Walk through the workspace
- By physically walking through the workspace, you can get a firsthand sense of the layout, lighting, temperature, noise levels, and pace of work. This can enable you to spot potential hazards lurking beneath the surface such as poor lighting that can lead to eye strain, tripping hazards that can cause falls and injuries, or excessive noise levels that can damage workers' hearing and increase stress. Armed with this information, you can take proactive steps to address these hazards and create a safer, healthier, and more ergonomic work environment for everyone. So why not take a stroll and see what you can discover?
|
FREE RESOURCE Manufacturing Workplace Safety Checklist
Start with a plan! Use this free Briotix Health checklist to help you identify potential hazards on your workplace analysis walkthrough.
|
Complete an ergonomic assessment of work tasks and equipment
- Ergo evaluations involve analyzing the design and layout of the workspace, evaluating the use of tools and equipment, and assessing workers' exposure to ergonomic risk factors such as excessive force, repetitive motions, and awkward postures to identify potential ergonomic concerns. It can be done with observation, interviews with workers, and specialized equipment to measure physical stress on the body.
|
SAMPLE REPORT Or, Leave the Assessment to the Experts!
Download our complimentary sample Industrial Ergonomics Assessment Report to see what all it entails - and how our comprehensive workplace assessment could benefit your organization!
|
(2) Evaluate work postures, movements, and forces
Once the work environment has been assessed, it is necessary to consider the physical demands of individual job tasks on workers' bodies. This includes evaluating the postures, movements, and forces required to perform their tasks to identify ergonomic risk factors. This step may involve observing workers performing their duties, performing interviews, or using specialized equipment to measure physical stress on the musculoskeletal system.
Complete a job analysis
- A job analysis involves breaking down the tasks associated with a job and identifying the physical demands associated with each one. This can be achieved through observation, interviews with workers, and specialized equipment to measure physical stress on the body. A thorough job analysis allows you to see exactly what the physical requirements of a job are and identify any areas of concern that increase risk of injury – such as performing repetitive work in awkward postures or lifting heavy loads without adequate support. Job analysis is necessary to be able to develop solutions that decrease the prevalence of those movements or eliminate those hazards.
- To get the most out of your job analysis data, store it in a digital system that is equipped to sort and analyze the data. A system like Briotix Health’s JOBABLE™ goes even further by providing powerful search and reporting features that assist your return-to-work and accommodations decision making and more.
|
SAMPLE REPORT Get Detailed with Job Analysis
Download our complimentary sample Job Analysis Report to see what all it entails - and how an expert analysis could benefit your workforce.
|
Consult with experts
- You can consult ergonomic experts to understand the risks associated with a job's physical demands better. Experts are better equipped to provide recommendations for improvements based on their experience and expertise.
(3) Review workers' feedback and complaints
No one knows the challenges of the work and the work environment as well as the people who do the job. It is essential to consider workers' feedback and complaints as well as injury data to identify potential ergonomic issues that may not be visible during your workplace analysis. Some tasks may not be directly causing injuries but are causing needless fatigue or harming productivity unnecessarily. Addressing these concerns can have a big impact on your worker satisfaction and productivity.
Hold focus groups
- Focus groups can be used to gather more detailed information on workers' experiences and concerns regarding ergonomic hazards. This can provide a deeper understanding of workers' issues and help identify potential solutions.
Encourage workers to report concerns
- By encouraging workers to report matters related to ergonomic hazards, you can gather information on potential issues that may not have been observed during the workplace analysis. This can be accomplished through several means, including but not limited to suggestion boxes, hotlines, or scheduled meetings with supervisors.
Perform private interviews
- Allowing workers to share their experiences and concerns related to ergonomic hazards in a more private setting can help identify potential issues that workers may be hesitant to share in a group setting.
Facilitate a safety culture survey
- A safety culture survey involves surveying workers to gather information on the organization's safety culture and the workers' attitudes toward safety. This can help identify potential barriers to reporting ergonomic concerns and develop solutions to address those barriers. An anonymous system can help encourage workers to report ergonomic concerns without fear of retaliation or negative consequences.
|
ADDITIONAL READING 9 Essential Steps to Build Safety Culture
Is your safety culture as strong as you would like it to be? Read more on the Briotix Health Blog about how to strengthen your safety culture.
|
(4) Develop and implement control measures
After identifying ergonomic risks, the next step is to develop and implement control measures to reduce or eliminate these risks. This may involve redesigning workstations, providing ergonomic tools or equipment, modifying work practices, or implementing training programs to educate workers on safe work practices.
Prioritize how you will address ergonomic hazards with a risk assessment
- Risk assessments help identify the risk associated with specific ergonomic hazards. Prioritizing the associated risks based on their severity and likelihood of occurrence helps you develop a plan that addresses the most pressing issues first.
Develop specific goals and objectives
- Developing specific goals and objectives for addressing identified ergonomic risks can help ensure that the plan is focused, measurable, and achievable. When developing your goals, use a decision-making framework that considers the level of risk, the feasibility of implementation, and the projected outcome to ensure that control measures are prioritized comprehensively and effectively with ROI in mind.
Use a team-based approach
- Involving a team of experts from different departments or disciplines can help ensure a more comprehensive and practical plan to address identified ergonomic risks. Involve feedback from workers for additional insights into the feasibility of implementing specific control measures and help prioritize efforts most likely to be accepted and effective.
- When working with multiple departments, it is especially important to assign responsibilities and timelines for addressing identified ergonomic risks to ensure that everyone is clear on their role and that the plan is executed efficiently.
Redesign workstations
- Redesigning workstations can involve adjusting the height of work surfaces, changing monitor angels, or providing adjustable chairs to reduce movements or postures that increase the risk of developing musculoskeletal disorders.
Provide ergonomic tools or equipment
- Providing ergonomic tools or equipment, such as anti-fatigue mats, wrist supports, or lift-assist devices, can help decrease the physical demands of the job and the risk of injury and discomfort.
Modify work practices
- Modifying work practices can involve adjusting the pace of work, rotating tasks, or providing rest breaks to reduce physical stress on the body and prevent injuries and fatigue.
Implement training programs
- Training programs can help educate workers on safe work practices and the importance of ergonomics in reducing the risk of injury and discomfort. Provide initial training on the use of ergonomic tools and equipment when they are first introduced to help ensure that workers understand how to use them properly and incorporate this training into onboarding and refresher training for your team.
- Ongoing training and education on ergonomic hazards and control measures can help maintain awareness and promote a culture of safety among workers. Using hands-on demonstrations can be more effective than verbal instructions alone.
Establish a clear process for reporting and addressing ergonomic hazards
- By creating a clear and accessible process for reporting ergonomic hazards, workers are more likely to identify and report potential issues in a timely manner. This can help prevent the occurrence of more serious ergonomic hazards and may also lead to the early identification of emerging issues that can be addressed before they become a problem.
(5) Monitor Effectiveness of Control Measures
The final step of an ergonomic process is to monitor the effectiveness of the control measures and continuously reassess and improve the ergonomic program. This may involve follow-up assessments, analyzing incident and injury data, or soliciting worker feedback to identify improvement areas. Maintaining a continuous monitoring, review, and improvement cycle is essential to ensure the ergonomic program remains effective over time.
Perform regular inspections and ergonomic audits
- Routine inspections of workstations and equipment can help identify potential new or ongoing ergonomic hazards. Audits can provide a more comprehensive evaluation of the ergonomic program and help identify areas that may need different or more robust control measures.
Use data-driven decision-making
- Using data to monitor the effectiveness of control measures and continuously reassess the ergonomic program can help ensure that decisions are based on objective evidence rather than subjective opinions. Benchmarking your results against industry norms or other organizations can help identify areas for improvement and best practices to address identified ergonomic hazards.
Identify trends and patterns in new incident and injury data
- Analyze the root cause of new incidents and injuries to identify underlying causes and contributing factors that may not be immediately apparent from an incident. Watch for trends and patterns in incident and injury data that highlight areas for improvement, such as particular workstations, tasks, or types of injuries. Comparing incident and injury data across time periods can help identify improvements or areas needing additional attention.
Nurture a continuous feedback loop with your focus groups and workers
- Whether you gather feedback in the form of surveys, anonymous suggestion boxes, or have meetings and one-on-one discussions with your workers, feedback is an essential tool to help assess the effectiveness of your new control measures and determine whether any additional steps are needed to help workers embrace the changes and champion your safety culture. Be sure to provide anonymous ways for workers to report concerns.
- Don’t disband your focus groups once changes are made. Continue to seek their feedback for more in-depth follow-up discussions of what is and isn't working and more potential areas for improvement.
Incorporate ergonomic review of new processes and procedures
- Don’t wait for a new problem to address it. By incorporating an ergonomic review of new methods and strategies, you can help ensure that potential hazards are identified and addressed before they are introduced to your workplace.
Periodic ergonomic program assessments
- Regular program assessments help ensure that the ergonomic program is meeting its intended goals and identify areas for improvement that can be incorporated into the ongoing monitoring, review, and improvement cycle.
Technology can help you manage your ergonomic process in-house
Managing an ergonomics program in-house is no small task – regardless of the size or your organization. If you are considering managing your ergonomics program yourself, ensure that you have the tools you need to be successful.
Industrial Ergonomics Software can help by providing the critical infrastructure you need to organize, execute, and manage your ergonomics process.
With advanced Industrial Ergonomics Software, like ErgoPlus Industrial, you can leverage technology to execute a first-rate ergonomics program.
- Train your team with on-demand lessons
- Assess risk using best practice assessment tools including computer vision and motion capture assessment
- Plan and quantify the value of recommended ergonomics improvements
- Measure progress with leading and lagging ergonomics metrics
- Scale your ergonomics solutions across any number of worksites
The benefit of using an all-in-one system to manage every stage of your ergonomic process leads to superior ROI and a healthier workforce. Check it out and request a demo at ergo-plus.com/software/!
Let’s make it better!
As an employer or employee, it is essential to take action to address ergonomic hazards in the workplace. By adhering to the guidelines presented in this article and instituting a proficient ergonomic program, you can assist in diminishing the chances of injury and discomfort among workers, fostering a more productive and efficient work environment, and maintaining conformity with applicable regulations and standards. Creating a safe and comfortable work environment is essential for a happy, healthy, and productive workforce.
For ergonomics consulting, job analysis, Industrial Ergonomics Software, and more, check out our website and send us a message (Briotix.com). We would love to work with you on a customized ergonomics solution for your workplace.
The content & opinions in this article are the author’s and do not necessarily represent the views of RoboticsTomorrow
Comments (0)
This post does not have any comments. Be the first to leave a comment below.
Featured Product
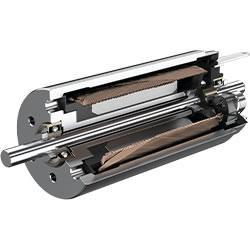