Wachendorff Automation: Accurate positioning ... for marking systems
Measuring system LMSLA12 for marking and labeling
(Geisenheim, 04.05.2015) Accurate positioning ... for marking systems
The position of the product to be labelled is determined based on this measurement. As a last stage of the packaging process, the product labelling or marking system uses this exact positioning information to mark, among other things, cardboard, packaging, labels, bottles and other materials accurately and in a superior print quality. Codes of any kind, brand logos and graphic designs, batch and lot numbers and sell-by dates are applied using inkjet processes or special inks, for example.
The components of the measuring system are perfectly matched and guarantee utmost precision and a long service life:
- With their IP65/67 protection, the encoders in the WDGI series are designed and adapted for use in harsh industrial environments.
- With a permissible radial load of 220 N on the shaft, the measuring system can be mounted securely without slipping and has a high pretensioning force.
- The specially selected surfaces of the different Wachendorff measuring wheels guarantee non-slip properties in all areas of application - even at very high production speeds.
- The encoder holder is a special development with two slot holes for flexible mounting.
- Exceptionally high repeat accuracy combined with a very high resolution of the WDGI encoder of up to 25,000 PPR (0.008 mm/pulse) guarantees an accurate marking position.
More information at: www.wachendorff-automation.com/
Featured Product
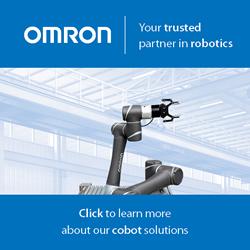
Discover how human-robot collaboration can take flexibility to new heights!
Humans and robots can now share tasks - and this new partnership is on the verge of revolutionizing the production line. Today's drivers like data-driven services, decreasing product lifetimes and the need for product differentiation are putting flexibility paramount, and no technology is better suited to meet these needs than the Omron TM Series Collaborative Robot. With force feedback, collision detection technology and an intuitive, hand-guided teaching mechanism, the TM Series cobot is designed to work in immediate proximity to a human worker and is easier than ever to train on new tasks.