'Pick and mix' smart materials for robotics
The new designer materials integrate the structure of two or more separate functions at the nanoscale, while keeping the individual materials physically separate.
Researchers from the University of Cambridge have developed a simple 'recipe' for combining multiple materials with single functions into a single material with multiple functions: movement, recall of movement and sensing -- similar to muscles in animals. The materials could be used to make robotics far more efficient by replacing bulky devices with a single, smarter, life-like material. The results are published in the journal Advanced Materials.
The new designer materials integrate the structure of two or more separate functions at the nanoscale, while keeping the individual materials physically separate. The gaps between the individual elements are so small that the final material is uniformly able to perform the functions of its component parts.
The materials are synthesised either in a one-pot reaction, with or without solvents; or through a series of sequential reactions, where the component parts are synthesised separately one by one, and sequentially infiltrated and cross-linked at the nanoscale.
'We're used to thinking of synthetic materials as structural, rather than functional things,' said Dr. Stoyan Smoukov of the University's Department of Materials Science and Metallurgy, who led the research. 'But we're now entering a new era of multi-functional materials, which could be considered robots themselves, since we can program them to carry out a series of actions independently.'
Smoukov's group had previously demonstrated combined movement and muscle memory in a single material, but this is the first time that materials have been specifically designed and synthesised to perform multiple functions.
Smart polymers were first developed several decades ago, but multiple functions have not been effectively combined in the same material, since previous efforts have found that optimising one function came at the expense of the other.
In these new materials, the individual functions are integrated yet kept separate at the nanoscale. The researchers combined two different types of smart materials: an ionic electro-active polymer (i-EAP), which bends or swells with the application of voltage and are used in soft robotics; and a two-way shape memory polymer (SMP), which can be programmed to adopt and later recall specific shapes, in a type of muscle memory.
The resulting combined material is what's known as an inter-penetrated network (IPN). Due to the fact that the separate components are meshed at the nanoscale, there are unbroken paths within each component from one side of the material to the other, yet there are nanoscale boundaries between them as well. Such IPNs are highly resistant to cracks, making them very mechanically stable. Rather than stop at mechanical stability, the researchers were interested in using these structures to make multi-functional artificial muscles, which can move, sense, and also report on their environment.
The movement in these hybrid materials can be controlled in several different ways, including by light, temperature, chemicals, electric field or magnetic field. These various stimuli can be used to make the materials change colour, emit light or energy, or change shape.
Making IPNs has been tried before with a type of plastic known as a block copolymer, but it has been difficult to fine-tune their exact structure because of difficult synthetic procedures. These difficulties limit the types of functionalities that can be combined, and those that are made are sometimes too costly for practical applications. In this case the researchers were able to use phase separation combined with ordinary polymer syntheses to achieve the complex structures.
According to the researchers, utilising this technique may open up a whole new avenue for smart materials, since materials that have been designed for other, single, purposes could create a large variety of multi-functional combinations. Much like choosing from an array of starters, main courses and desserts in a restaurant menu to create a multitude of dinner options, materials that perform different single functions can be combined in a mix-and-match approach to perform a myriad of tri-functional combinations. And in theory, according to the researchers, more than three intertwined components are achievable as well.
'It's sort of like proteins, where using just 20 amino acids, you can get 8,000 different combinations of three amino acids,' said Smoukov. 'Using this method, we can pick and choose from a menu of functions, and then mix them together to make materials that can do multiple things.'
The capabilities of these materials could make them very useful in robotics -- in fact, said Smoukov, these types of materials could even be considered robots on their own.
'We're trying to design materials that approach the flexibility of living things,' said Smoukov. 'Looking at the functionality of living things, we then want to extract that functionality and find a way to do it more simply in a synthetic material. We're peeling back some of the layers of mystery that surround life.'
Featured Product
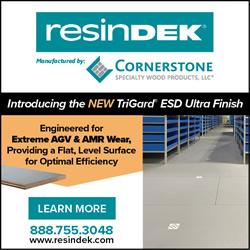