Ansaldo Nuclear uses bespoke robot in latest phase of Italy’s largest decommissioning project
Ansaldo Nuclear recently provided a bespoke robot to effectively extract and recover 2,000 drums of radioactive waste from hard-to-access storage locations at Caorso Nuclear Power Plant, as part of one of the biggest and most complex decommissioning projects in the industry.
Within the decommissioning licence, obtained in 2014, one of the key projects is the treatment and conditioning of around 860 tons of radioactive ion exchange resins and sludges, still contained in two temporary storage buildings at the Caorso facility. This waste represents more than 90% of the contamination inventory at Caorso NPP. The aim of the project is to transform this waste into final packages, with a volume reduction factor of 10, whilst emptying the two storage buildings in order to refurbish them.
Ansaldo Nuclear was contracted in 2015 by Società Gestione Impianti Nucleari SpA (Sogin) for the retrieval, transport, treatment and conditioning of the spent resins and sludges as part of a joint venture with JAVYS. This will see the firm transporting a total of 5600 200kg drums of Caorso's radioactive waste to the JAVYS waste storage facility at Jaslovské Bohunice in Slovakia, to be stabilised via incineration and finally conditioned.
To enable the retrieval project to commence in January 2020, Ansaldo Nuclear conceptualised, designed, manufactured, installed and operated a bespoke Machine Retrieval System (MRS) robot to safely retrieve 2,000 drums of radioactive waste which were stored in a variety of niches within the temporary storage facilities at Caorso.
Overseeing the project was Francesca Maggini, Project Engineer and Bid Technical Manager at Ansaldo Nuclear, who commented: "The extent of the logistical challenge presented by this phase of the Caorso decommissioning project cannot be underestimated. The unique nature of nuclear decommissioning means it is important to face each decommissioning project as an entirely new challenge. You cannot simply repeat the successes of the past - you must pioneer and develop bespoke solutions in order to see the best results. Through effective innovation and installation, we have enabled the decommissioning of Caorso to continue. Ansaldo Nuclear has been involved with the decommissioning of Caorso since 2000, and we're proud to remain on this substantial project today."
The MRS robot, which was used to retrieve, verify, seal and pack the radioactive drums, took six months to build and install. Controlled remotely, with a double operating system in place in case of system failure, it is capable of self-recovery in the event of earthquakes or other external safety issues.
Francesco Orzelli, Designer and Structural Analyst at Ansaldo Nuclear, was instrumental in developing the robot's design. Speaking about the unique nature of the project, Francesco noted how it was important to maintain a proactive attitude in the face of logistical difficulties: "The MRS robot used for the automatic recovery of radioactive drums at Caorso was extremely effective, having been designed from the start with safety, efficiency and adaptability as key priorities. One of the key challenges was that we were unable to access the area to take detailed measurements, so the robot had to be constructed to be as compact as possible to allow enough clearance. In doing this, we first created a fully-functioning, 3D model, complete with all mechanical components, to allow us to develop a small machine with significant capabilities.
"We received only the boundary conditions from the Customer. This meant Ansaldo Nuclear not only had to manufacture and install an automated retrieval robot, but develop the solution as well - a process which took two years. Through proactive planning and careful implementation we were able to develop a robot with the freedom and adaptability to retrieve all the drums required, which has allowed Caorso to continue its decommissioning process on schedule."
Featured Product
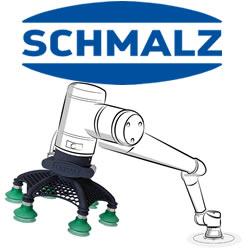