Why Human-Controlled, Force-Multiplying Robots Are the Future of Work on Earth
Ben Wolff, CEO of Sarcos via IEEE Spectrum: When most people think of robots, they picture an R2-D2-like droid, providing critical information to assist humans and courageously rescuing them from dangerous situations. While we are, in my view, decades away from having robots that can function like a “Star Wars” character due to the limitations of artificial intelligence, a new class of robots that are mobile, dexterous, and capable across multiple operational regimes will soon be available to augment human performance.
This will happen through a combination of human intelligence with machine strength and precision. In this symbiotic relationship, the multi-tasking robots rely on humans for direction while simultaneously safeguarding them from dangerous environments and tasks. These robotic “guardians” are the future of work on Earth and, yes, in space, too.
We are at a point in history where decades of research and development coupled with ever-improving technological performance and lower component costs are combining to make yesterday’s science fiction a reality. Imagine a machine that is your personal proxy, controlled by you, leveraging your intelligence, knowledge, instincts, intuition, and judgment while able to physically perform in the same manner as your own body, but safely, and with super-human strength, endurance, and precision. This vision is at the core of the Guardian robot systems concept developed at my company, Sarcos Robotics, based in Salt Lake City, Utah. Full Article:
Comments (0)
This post does not have any comments. Be the first to leave a comment below.
Featured Product
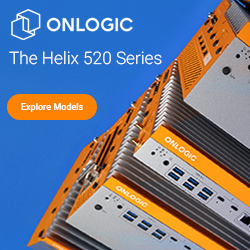