New technique eases production, customization of soft robotics
Scott Schrage, University of Nebraska-Lincoln via Phys.org: By helping rubber and plastic stick together under pressure, University of Nebraska-Lincoln chemists have simplified the production of small fluid-carrying channels that can drive movement in soft robotics and enable chemical analyses on microscopic scales.
The technique, which creates a stronger chemical bond between silicone and an unprecedented array of plastics, could greatly reduce the time, complexity and expense needed to produce and customize the microfluidic devices.
"We're really excited, because we're providing a (technique) to successfully integrate different materials in a way that is streamlined and supports numerous practical applications," said Stephen Morin, assistant professor of chemistry. "We think that can really offer new opportunities to the community."
In demonstrating those opportunities, the team used a basic software program to design microfluidic networks and a standard laser printer to map those channels onto a transparent Mylar sheet. After exposing the plastic sheet to ultraviolet light and submerging it in a solution, the researchers laid the sheet atop a silicone film and applied heat.
The plastic and silicone bonded strongly—except where pathways had been marked by the printer's ink. When the team pumped air or liquid into those unbound sites, the fluids flowed through them at rates dictated by the pressure being applied—pressures several times higher than what previous bonding techniques have withstood. Full Article:
Comments (0)
This post does not have any comments. Be the first to leave a comment below.
Featured Product
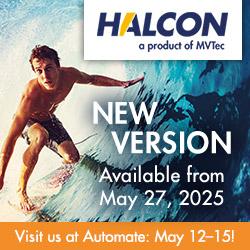