Rutgers Researchers Create a 3D-Printed Smart Gel That Walks Underwater, Moves Objects
Rutgers University–New Brunswick engineers have created a 3D-printed smart gel that walks underwater and grabs objects and moves them.
The watery creation could lead to soft robots that mimic sea animals like the octopus, which can walk underwater and bump into things without damaging them. It may also lead to artificial heart, stomach and other muscles, along with devices for diagnosing diseases, detecting and delivering drugs and performing underwater inspections.
Soft materials like the smart gel are flexible, often cheaper to manufacture than hard materials and can be miniaturized. Devices made of soft materials typically are simple to design and control compared with mechanically more complex hard devices.
“Our 3D-printed smart gel has great potential in biomedical engineering because it resembles tissues in the human body that also contain lots of water and are very soft,” said Howon Lee, senior author of a new study and an assistant professor in the Department of Mechanical and Aerospace Engineering. “It can be used for many different types of underwater devices that mimic aquatic life like the octopus.”
The study, published online today in ACS Applied Materials & Interfaces, focuses on a 3D-printed hydrogel that moves and changes shape when activated by electricity. Hydrogels, which stay solid despite their 70-plus percent water content, are found in the human body, diapers, contact lenses, Jell-O and many other things.
Comments (0)
This post does not have any comments. Be the first to leave a comment below.
Featured Product
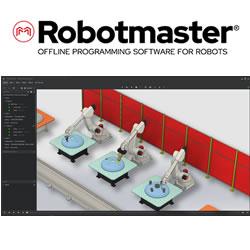