A Step Closer to Self-Aware Machines - Columbia engineers create a robot that can imagine itself
New York, NY—January 30, 2019—Robots that are self-aware have been science fiction fodder for decades, and now we may finally be getting closer. Humans are unique in being able to imagine themselves—to picture themselves in future scenarios, such as walking along the beach on a warm sunny day. Humans can also learn by revisiting past experiences and reflecting on what went right or wrong. While humans and animals acquire and adapt their self-image over their lifetime, most robots still learn using human-provided simulators and models, or by laborious, time-consuming trial and error. Robots have not learned to simulate themselves the way humans do.
Columbia Engineering researchers have made a major advance in robotics by creating a robot that learns what it is, from scratch, with zero prior knowledge of physics, geometry, or motor dynamics. Initially the robot does not know if it is a spider, a snake, an arm—it has no clue what its shape is. After a brief period of “babbling,” and within about a day of intensive computing, their robot creates a self-simulation. The robot can then use that self-simulator internally to contemplate and adapt to different situations, handling new tasks as well as detecting and repairing damage in its own body. The work is published today in Science Robotics.
Video of Columbia Engineering robot that learns what it is, with zero prior knowledge of physics, geometry, or motor dynamics. Initially the robot has no clue what its shape is. After a brief period of “babbling,” and within about a day of intensive computing, the robot creates a self-simulation, which it can then use to contemplate and adapt to different situations, handling new tasks as well as detecting and repairing damage in its body.
To date, robots have operated by having a human explicitly model the robot. “But if we want robots to become independent, to adapt quickly to scenarios unforeseen by their creators, then it’s essential that they learn to simulate themselves,” says Hod Lipson, professor of mechanical engineering, and director of the Creative Machines lab, where the research was done.
For the study, Lipson and his PhD student Robert Kwiatkowski used a four-degree-of-freedom articulated robotic arm. Initially, the robot moved randomly and collected approximately one thousand trajectories, each comprising one hundred points. The robot then used deep learning, a modern machine learning technique, to create a self-model. The first self-models were quite inaccurate, and the robot did not know what it was, or how its joints were connected. But after less than 35 hours of training, the self-model became consistent with the physical robot to within about four centimeters. The self-model performed a pick-and-place task in a closed loop system that enabled the robot to recalibrate its original position between each step along the trajectory based entirely on the internal self-model. With the closed loop control, the robot was able to grasp objects at specific locations on the ground and deposit them into a receptacle with 100 percent success.
Even in an open-loop system, which involves performing a task based entirely on the internal self-model, without any external feedback, the robot was able to complete the pick-and-place task with a 44 percent success rate. “That's like trying to pick up a glass of water with your eyes closed, a process difficult even for humans,” observed the study’s lead author Kwiatkowski, a PhD student in the computer science department who works in Lipson’s lab.
An image of the deformed robotic arm, deformed by using a 3d printed piece as a replacement for one of the standard arm parts to extend and change the angle of the gripper.
The self-modeling robot was also used for other tasks, such as writing text using a marker. To test whether the self-model could detect damage to itself, the researchers 3D-printed a deformed part to simulate damage and the robot was able to detect the change and re-train its self-model. The new self-model enabled the robot to resume its pick-and-place tasks with little loss of performance.
Lipson, who is also a member of the Data Science Institute, notes that self-imaging is key to enabling robots to move away from the confinements of so-called “narrow-AI” towards more general abilities. “This is perhaps what a newborn child does in its crib, as it learns what it is,” he says. “We conjecture that this advantage may have also been the evolutionary origin of self-awareness in humans. While our robot’s ability to imagine itself is still crude compared to humans, we believe that this ability is on the path to machine self-awareness.”
Lipson believes that robotics and AI may offer a fresh window into the age-old puzzle of consciousness. “Philosophers, psychologists, and cognitive scientists have been pondering the nature self-awareness for millennia, but have made relatively little progress,” he observes. “We still cloak our lack of understanding with subjective terms like ‘canvas of reality,’ but robots now force us to translate these vague notions into concrete algorithms and mechanisms.”
Lipson and Kwiatkowski are aware of the ethical implications. “Self-awareness will lead to more resilient and adaptive systems, but also implies some loss of control,” they warn. “It’s a powerful technology, but it should be handled with care.”
The researchers are now exploring whether robots can model not just their own bodies, but also their own minds, i.e. whether robots can think about thinking.
###
Columbia Engineering
Columbia Engineering, based in New York City, is one of the top engineering schools in the U.S. and one of the oldest in the nation. Also known as The Fu Foundation School of Engineering and Applied Science, the School expands knowledge and advances technology through the pioneering research of its more than 220 faculty, while educating undergraduate and graduate students in a collaborative environment to become leaders informed by a firm foundation in engineering. The School’s faculty are at the center of the University’s cross-disciplinary research, contributing to the Data Science Institute, Earth Institute, Zuckerman Mind Brain Behavior Institute, Precision Medicine Initiative, and the Columbia Nano Initiative. Guided by its strategic vision, “Columbia Engineering for Humanity,” the School aims to translate ideas into innovations that foster a sustainable, healthy, secure, connected, and creative humanity.
Comments (0)
This post does not have any comments. Be the first to leave a comment below.
Featured Product
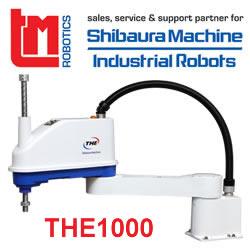