Robotic Disruption in US Workforce Leads to New Opportunities and Challenges
The U.S. workforce has faced a fair amount of disruption in the past few years. From mass layoffs to the work-from-home revolution and now labor shortages, the employment landscape keeps shifting. Amid all of this change, more companies have started embracing robotics.
North American industrial companies ordered a record 29,000 robots in the first nine months of 2021. That’s a 37% increase over 2020, and considering how automation adoption has steadily risen over the years, this trend won’t likely slow down. As companies across industries continue to struggle with workforce shortages, robots provide an ideal solution.
The workforce is becoming increasingly robotic, and that shift is happening faster than many anticipated. Here’s a look at the opportunities and challenges that creates.
Opportunities With Robotic Disruption
Naturally, employing robots comes with significant advantages. If it didn’t, there wouldn’t be so many companies investing so heavily in it. That said, this technology is still relatively new, and misconceptions about it abound. While every company may have its own motivation for automating, here are the most substantial benefits of robotic disruption.
Increased Productivity
The leading advantage of robots is their efficiency. Repetitive and data-heavy tasks often pose a challenge to humans who get tired and bored. Robots don’t face those obstacles and can perform some tasks as much as 500% faster than human workers. That efficiency is hard to overlook.
Robots’ speed and repeatability alone aren’t the only factors that improve productivity, either. Since they automate tasks that humans previously performed, they free employees to focus on other workflows. Companies can then accomplish more work in less time with the same number of workers.
These productivity gains have become increasingly valuable as companies faced labor shortages amid the Great Resignation. On average, more than 3.98 million workers quit their jobs each month in 2021. With dwindling staff numbers, companies needed ways to maximize productivity and robots provided the answer.
Improved Safety
Robotic automation also makes many workplaces safer. Industrial workplaces are often full of hazards. Working on a car, for example, can include exposure to toxic chemicals, extreme heat, sharp edges and the risk of being crushed under the vehicle. The safest way to manage these hazards is to remove them entirely.
Assigning robots to the most dangerous work keeps a safe distance between human workers and hazards. While measures like training and personal protective equipment (PPE) help mitigate these risks, automation addresses the root issue. Dangerous processes aren’t technically dangerous if there’s no one nearby to get hurt.
These safety improvements do more than protect employee health and wellness, too. They also save companies time and money. Fewer accidents result in less lost productivity and time, and businesses won’t lose as much to worker’s compensation payments and related expenses.
Mitigating Human Behavior Issues
Integrating robotics into the workforce can also help overcome issues related to human behavior. The most prominent example of this is how they reduce errors, an almost unavoidable human characteristic. Even the most well-trained employee can make mistakes, especially if they’re tired, bored or distracted, but robots deliver consistent results with high repeatability.
Robots also don’t face behavioral problems that can cause conflict within the workplace. Substance use disorders can cost between $2,600 and $13,000 per employee, and their presence is often outside of businesses’ control. It’s impossible for a robot to work while intoxicated, so these machines mitigate that vulnerability.
Robotic workers also won’t get into relational disputes with human coworkers, which often hinders productivity in traditional workplaces. Using robots to maintain a healthy distance between some employees can help reduce the impact of existing workplace conflicts.
Downsides to the Robot Workforce
The benefits of robotic disruption in the workforce are hard to ignore. As the shortcomings of conventional workplaces have become more clear to businesses, more have realized these advantages. However, robots come with unique downsides, too.
Robots’ disadvantages don’t necessarily disqualify their benefits altogether, but they demand attention. Companies considering implementing robots or upscaling their robotic efforts should think about the downsides to these technologies to make the best decisions. The most effective and fair robot initiatives balance the opportunities with the challenges.
Wage and Employment Disruption
The most significant challenge of an increasingly robotic workforce is the resulting disruption in jobs and wages. Recent studies reveal that the longest-standing fear around automation is coming true: people are losing jobs to robots. For every robot added per 1,000 workers, employment-to-population ratios decline by 0.2%, which may not seem like much, but has resulted in 400,000 lost jobs so far.
Average wages drop even faster than employment in areas that adopt more robots. Salaries fall by 0.77% for every robot added per 1,000 workers. This drop in pay could result from employers seeing human workers as less valuable when compared to robots. Even if that sentiment isn’t accurate, the results have real impacts on real people.
Despite these short-term losses, studies also show that robots have a positive impact on employment over time. As automation takes some jobs, it creates new employment opportunities elsewhere. Some experts predict that by 2025, robots will create 97 million new jobs while displacing 85 million.
Of course, that still means that 85 million people could lose their jobs in the short term. The new careers that open are often in different locations and require different skills, so thinking of it as an exact one-to-one ratio isn’t entirely accurate. If employers want to minimize job displacement, they must focus on upskilling and reskilling workers who could lose their jobs to robots.
Over-Application
Businesses also risk over-applying robots beyond their capabilities. While robots’ abilities do surpass humans’ in repetitive and data-heavy tasks, they’re not a perfect replacement for human workers. Humans are far more adept at any work that requires nuance or adaptability.
The best way to implement robots is to help employees in their work, not replace them. Viewing these machines as better alternatives to workers will result in more risk than reward, harming both employment and businesses’ finances. As robots become increasingly popular and affordable, companies must ensure they don’t think they’re more capable than they are.
Robots Will Change the Workforce for Good
Robots have already changed the face of the workforce in many areas. That trend will grow and spread, and if businesses keep the relevant challenges in mind, it can be beneficial in the long run.
Like any new technology, robots come with impressive benefits and equally substantial risk potential. Companies need to recognize and address these downsides to ensure robotic disruption in the workforce is positive and not harmful.
Comments (0)
This post does not have any comments. Be the first to leave a comment below.
Featured Product
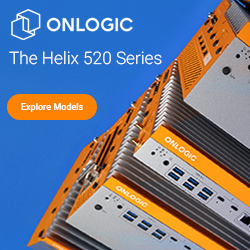