5 Transportation Solutions for Fragile Robots
Robots are some of the most essential tools an industrial business can have. Many manufacturers understand this, so many know the importance of keeping these machines in optimal condition for as long as possible. However, transportation introduces some new concerns into the equation.
Businesses may need to move robots for one of many reasons. They could move to a new facility, place some robots in storage during slow seasons or have to move newly purchased machines themselves. Whatever the specifics, shipping these machines can be an intimidating prospect.
While robot prices have steadily fallen, they could still cost more than $10,000 apiece in 2025. Some of these highly specialized, complicated machines may also be fragile. Here are five transportation solutions businesses must consider to move this equipment safely.
1. Appropriate Packaging
The first solution to consider is the packaging. That applies to both the container that will store the robot and the insulating materials within it. Which material and container type are best varies between specific use cases, but there are some general guidelines to follow.
Packaging strength is one of the most important factors to go over, considering robots’ weight. A robot with just 7 kilograms of lifting capacity will weigh around 300 kilograms on average, rendering lighter materials like cardboard insufficient. Wood crates are ideal — even then, companies should ensure their carrying capacity is far beyond their robots’ weight.
Protecting the robot from bumping into the crate itself is also vital. A mix of rigid insulation-like styrofoam and more flexible solutions such as bubble wrap could yield the best result. Anti-static insulation is also crucial, as it prevents electrical hazards during shipment.
2. Secure Trailers
Next, businesses need to determine the best type of trailer to move their packaged robots in. Depending on whether companies are using a third-party logistics (3PL) provider or are shipping the robot themselves, their options will vary. However, in either case, they should look for some of the same core factors.
Closed trailers are a must, as open ones introduce too many external hazards for shipments this fragile. Companies should also look at their trailers’ suspension to ensure it will provide a smoother ride, reducing vibrations within the crates. Strong ramps to facilitate easier loading and unloading are also important.
Companies working with a 3PL provider should communicate these needs so the 3PL firm can show them the ideal solution. If businesses are handling the transportation themselves, they can use a guide to understand the best options.
3. Route Planning
Route planning is an easily overlooked but critical transportation solution for fragile robots. Many businesses take route planning seriously, but they look at it primarily as a way to shorten travel times and avoid disruption. As helpful as that is, companies should consider which routes are the safest when shipping sensitive equipment.
More than 40% of American roads are in poor or mediocre condition. That means, without careful route planning, robot shipments may encounter bumps, slick conditions or other hazards that could damage them in transport. Businesses can avoid this by looking at repair factors when planning the route and following the smoothest, most well-maintained roads.
In some areas, companies should also consider factors like sharp turns and steep hills, which may raise transport hazards. Similarly, it’s crucial to review the weather and find the ideal time to ship, as rain, snow and other conditions may make damage more likely.
4. Tracking Solutions
Another transportation solution to consider is vehicle and shipment tracking. Internet of Things (IoT) sensors can offer real-time information about where a robot shipment is, its condition and other information. This insight can help hold transportation partners accountable and enable quick responses to unforeseen circumstances.
Telematics solutions can detect engine problems earlier and inform drivers and other stakeholders. Businesses can then fix the issue before it becomes a more significant problem that may jeopardize the safety of the robots. Similarly, companies can use IoT trackers to monitor vibrations within the trailer, stopping or rerouting the shipment if they get too high.
Tracking solutions also provide needed transparency between 3PL providers and businesses. This accountability encourages drivers to be careful and efficient, helping reduce the risk of human error. Consequently, companies should only work with 3PL firms that offer these tracking services if they aren't handling their own transport.
5. Loading and Unloading
Businesses should also consider their loading and unloading solutions. While the transportation itself may take most of the focus, these seemingly minor processes could damage robots if employees aren’t careful, so they deserve attention. Companies need a defined, thought-out approach to loading and unloading robot shipments to prevent damage.
Given robots’ weight, facilities likely need equipment like forklifts to move containers on and off trailers. Experts expect improper operation of these machines to cause $86 million in damages over the next ten years, so only trained, seasoned and certified employees should use them. Employees must also ensure forklifts and similar machines are in optimal condition before using them.
Businesses may also need to plan forklift routes just as they plan shipment directions. That could entail clearing space in the facility and outlining clear paths for forklift operators to follow so they don’t run into anything.
Other Factors to Consider
These five transportation solutions should be a part of any business’s plan to move fragile robots. However, there are some other outside factors to consider, too.
Some industries may face regulations over how they can ship electronic equipment like robots, which may dictate packaging materials and disassembly. Companies should review any applicable laws and industry regulations to ensure their plans meet these requirements. Even if no rules apply, looking at these can provide a helpful baseline for how to package and move these systems.
Businesses should also consider the cost of moving robots. Shipping anything this heavy and delicate will likely incur high expenses, but how high they are will vary. Companies should compare rates between 3PL providers and rental services to find the best balance between safety and costs.
While it may seem obvious, businesses must also remember to post appropriate labels on their robot packaging. Fragile warnings and other hazard labels will help encourage careful handling.
Transport Fragile Robots Safely
Robots are a significant investment, so they deserve care when handling them in any context. Shipping these machines may seem intimidating, but it doesn’t have to be hazardous if businesses plan appropriately.
Following these steps and considering these factors will help ship robots safely. Companies can then protect their investments and get the most out of this equipment.
Comments (0)
This post does not have any comments. Be the first to leave a comment below.
Featured Product
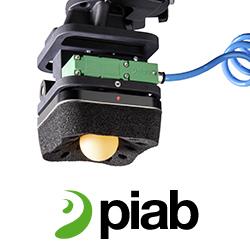