AI-Powered Kindred INDUCT Automates Induction of One Million Items with 95% Accuracy
Kindred, part of Ocado Group, has released the results of an 18-month beta test of its INDUCT AI-powered robotic induction system. INDUCT automated the induction of more than one million items at 95% accuracy in a grueling, fast-paced global logistics center where the beta trial was held.
“This was the most intense and demanding real-world scenario we could test in, and INDUCT emerged triumphant,” said Marin Tchakarov, CEO of Kindred. “By succeeding here, we have proven INDUCT can be successfully deployed now in any type of facility that uses induction.”
Kindred INDUCT is a high-speed robotic workcell built on Kindred’s proprietary CORE/AutoGrasp™ artificial intelligence (AI) platform. It combines machine vision, grasping, and manipulation algorithms to automate the induction process for a variety of item sets, including boxes, envelopes, parcels, and packages. Because it’s powered by Kindred’s reinforcement learning-based AI algorithms, INDUCT workcells become smarter, faster, and more efficient over time. To see a video of how the INDUCT system works, visit www.kindred.ai/solutions/induct.
At the end of the 18-month beta program, INDUCT had achieved the following performance rates:
- 1 million packages processed through the induction cycle
- 1,800 picks per hour (PPH) average throughput
- 2,000 PPH at its peak
- 95% of items processed were placed accurately onto the moving conveyor system
- 96% barcode scan rate
- 99% complete autonomous worktime
Passing the Ultimate Induction Test
The beta test was designed to put the INDUCT system through its paces in the most grueling and fast-paced logistics environment over the course of two peak seasons. An INDUCT workcell was incorporated into an existing induction line at a global logistics facility and transportation hub where 200,000 small parcels are sorted each hour, and up to 400,000 parcels are processed during the peak holiday season. The 18-month beta allowed the workcell to operate in numerous peak seasons and measure performance over a significant period.
Items ranging from time-sensitive legal documents to fragile packages arrive at the facility by plane or truckload. Within two hours, these items must be quickly, delicately, and accurately unloaded, sorted, and reloaded to be transported to final delivery points, within guaranteed timelines.
Packaging approaches and strategies are ever-changing, and Kindred engineers made adjustments to the workcell and algorithms to handle new packaging materials and form factors that would appear in the item flow.
“We will use the vast amount of data collected during the INDUCT beta to expand and strengthen our CORE/Autograsp™ AI platform, the foundation of all Kindred systems,” explains Tchakarov. “This will help us expand the type of item sets our other product lines, such as SORT, can handle in the future, widening the addressable market for the company.”
Integrating Into Existing Induction Settings
INDUCT workcells are commercially available now and integrate seamlessly into facilities that process and handle item sets, including boxes, envelopes, parcels, and packages. Multiple workcells can perform collaboratively along the same fulfillment line for maximum productivity and alleviate capacity shortages for parcel, post, logistics, delivery, and e-commerce supply chains, distribution centers, and warehouses.
INDUCT is compatible with a wide range of communication protocols, customizations, and customer and warehouse management systems. Kindred’s integration team can develop customized performance statistics and parameter configurations for ease of implementation.
Since INDUCT is offered as a Robots as a Service (RaaS) model, companies can realize immediate financial returns and minimize the capital investment of working with robotic systems by paying per item handled.
Request more information and watch the INDUCT system in action at www.kindred.ai/solutions/induct.
About Kindred
Founded in 2014, Kindred, part of Ocado Group, is a robotics and artificial intelligence (AI) company contributing to the workforce of the future through human-robot collaboration. Kindred’s cutting-edge CORE/AutoGrasp™ reinforcement learning platform is the foundation of its proprietary technologies, including AI-enabled SORT and INDUCT robots. Kindred robots continuously improve becoming faster and more accurate over time so clients can automate e-commerce fulfillment and supply chain operations while increasing throughput. The company is co-located in San Francisco and Toronto and is part of the UK-based Ocado Group plc. For more information, visit www.kindred.ai.
Comments (0)
This post does not have any comments. Be the first to leave a comment below.
Featured Product
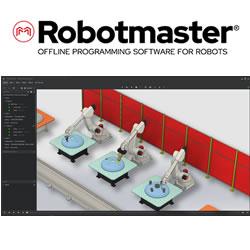