4 Ways Soft Gripper Robots Improve Food Processing
Food processing plants deal with high product volumes while maintaining tight regulatory standards. Many executives have invested in soft gripper robots that bring them numerous advantages. Any decision-maker considering this approach should think about their goals, time frame and budget. Figuring out those specifics makes it easier to determine which robots to buy and how many to use. Knowing about the most common benefits can also motivate people to invest in these high-tech machines.
1. Increased Productivity
Soft gripper robots allow companies to dramatically increase productivity by enabling assembly lines to process more items per hour. That’s particularly beneficial with many food processing companies experiencing labor shortages and high turnover rates. Some people find the work too repetitive, boring or strenuous, depending on their roles. Individuals seeking employment may not immediately consider manufacturing or processing positions as options, especially if they’ve never worked in similar environments.
Industry projections suggest food industry revenue will reach $996.40 billion in 2023. That’s good news for leaders, but they must find practical ways to address their workforce needs. Soft gripper robots are accessible, purpose-built possibilities.
The ideal situation involves humans and robots working together. Some advanced machines can pick multiple food items each second. The gripper’s pliable nature also helps the robot grasp unusually shaped products. Many options work with numerous effectors, letting people quickly switch between those accessories to meet various products’ requirements. Making those efficient changes raises productivity by shortening production stoppage times.
Performing the recommended maintenance is a best practice for keeping robot productivity high. Robots may slow down or stop working if parts become worn without people noticing or if the necessary upkeep does not occur. Such events could interrupt workflows, causing companies to lose the previously achieved productivity gains.
2. Reduced Waste
Food processors often deal with challenges when delicate items are mishandled and broken or dropped. Soft gripper robots can tackle this problem, especially since many are specially designed to handle fragile items, such as eggs. Machines that can grasp and move easily breakable items are less likely to become unsellable during production.
One option works when artificial intelligence and 3D images inform the gripper how to handle numerous products based on appearance. It can pick more than 70 doughnuts every minute.
Researchers are also continually searching for soft gripper robot improvements, recognizing the ongoing need for such innovations. One team took inspiration from kirigami, a Japanese art where people turn two-dimensional material sheets into 3D creations. These soft grippers surround the object before lifting it, working similarly to a person’s cupped hands. Experiments showed these creations could handle egg yolks without crushing them.
In another research-based example, a group determined the force required to pick blackberries and not damage them. Their tests involved humans wearing a pressure-sensing apparatus while handling thousands of berries. The results indicated the ideal force was half of 1 Newton — or what’s necessary to lift a candy bar.
In the study’s next phase, the researchers designed a gripper with a guitar string as a tendon. However, it caused more damage to the blackberries than previous versions. This work is valuable for informing future soft gripper designs for robots.
3. Improved Cleanliness and Safety
Many companies also cater to the food processing industry by making soft gripper robots that are easy to clean. That helps businesses maintain strict cleanliness standards and keep customers safe. Food-grade silicones are popular materials because they’re soft and flexible yet durable. There’s also no risk that these options will leach chemicals into the foods.
Developing soft gripper robots that are easy to clean also supports consumer safety. Manufacturers often sell products intended for people sensitive to certain ingredients. However, many allergen-free products are made in factories containing them. Fortunately, thoughtful designs that support cleanliness reduce the risk of cross-contamination. Materials are often easy to hose down after use, and some are even dishwasher-safe.
Soft gripper robots also enhance safety by reducing the possibility of workers getting repetitive strain injuries. Many food processors add automation to their assembly lines and find it minimizes absenteeism. It can also eliminate safety risks caused by employee fatigue. Even though employees may initially fear robots will take their jobs, these benefits highlight valuable reasons for humans and machines to work together.
4. Enhanced Flexibility
Food processors often work with dozens of products in each facility, making it easier to maintain marketplace competitiveness. If consumers become less interested in one offering, processing plants can pivot to ramp up the production of something more in demand.
Soft gripper robots can adapt to meet users’ changing needs. In one instance, a researcher incorporated machine learning into an adaptive robotic gripper for fruit harvesting. The project resulted in an innovation that achieved up to 98% accuracy while recognizing and grabbing five types of fruit. The researcher built the robot to detect the produce and automatically use the appropriate force to grasp it.
The team with the kirigami-inspired gripper further improved their invention and gave it impressive versatility. They went with a substantially different design in this more recent effort and changed the grippers’ trajectory. This new soft gripper is gentle enough to pick up a water drop, but it can also hold more than 14 pounds. Experiments also proved it could grasp microfilms 20 times thinner than a human hair strand.
Another team developed a soft robotic attachment to pick, hold and scoop items. Tests indicated it could pick items only 300 microns thick or scoop up couscous and rice.
Something that makes this invention stand out is the use of multimodal actuation in the design. That enables rapid workspace changes to support payloads of various contact areas. This gripper can expand its workspace volume by nearly 400%, giving it a broad range of grasping capabilities.
Soft Gripper Robots Are Appealing Options
These are some of the many advantages company leaders experience after investing in soft gripper robots for food processing tasks. Even after recognizing the benefits, some executives may want to bring these machines into the workplace gradually and only scale up once they see positive results. That’s a popular option, and one that can provide confidence, especially when people start using these machines for the first time.
Comments (0)
This post does not have any comments. Be the first to leave a comment below.
Featured Product
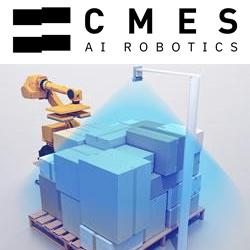