NHL Goal Celebration Hack With A Hue Light Show And Real Time Machine Learning
AGROBOT: Strawberry Harvesters
Rethinks New Robot: Sawyer
Star Wars' BB-8
NASA's Modular Robotic Vehicle (MRV)
3D Robotics' Solo
DJI Phantom 3
QinetiQ North America Introduces DriveRobotics
Gear Generator
Lumipen 2: Robust Tracking for Dynamic Projection Mapping
Festo BionicANTs and eMotionButterflies
Frankenimage
Monoprice's $699.99 Dual Extrusion Printer
Artoo: Ruby on Robots
What You Wanted To Know About AI
Records 1261 to 1275 of 1637
First | Previous | Next | Last
Featured Product
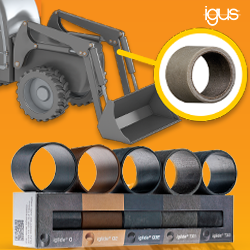