Drive Systems - Success Through Interdisciplinary Approaches
Applications of Nanometer-Level Precision Motion Control Solutions
Zone Picking vs. Wave Picking: Which Method is Best?
SCARA Robots - The Next Move in Automotive Sector; Towards the Automation!
The Perfect Storm of Automation, Autonomous Machines and Artificial Intelligence
Concept Systems and ATI Deburring Tools Reshape Aluminum Manufacturing Processes
Electromechanical Linear Actuators in Robotics & Autonomous Vehicles
New Collaborative Robot Vacuum Tool
Güdel Integrates Tool Changers in Multi-Purpose Metal Forming Solution
The cornerstones of Zimmer Group's Industry 4.0 success in production
ATI F/T Sensors Give Hirebotics a Better Feel for the Job
maxon motor - Formulae Handbook for Design Engineers
5 Big Innovations in Robotic End of Arm Tools Landscape
Looking for a Robotic Gripper?
Robot Modularity - Q&A with Víctor Mayoral, CEO of Acutronic Robotics
Records 646 to 660 of 1963
First | Previous | Next | Last
Industrial Robotics - Featured Product
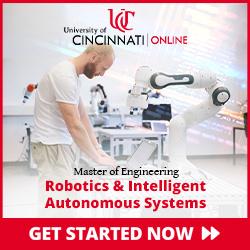