Companies considering a new material handling system are often simultaneously evaluating warehouse management systems (WMS) or have already implemented a WMS. When considering an automated material handling solution such as the Kiva Mobile Robotic Fulfillment System, companies often ask how the systems will work together.
Kiva Systems provides a new approach to automated order fulfillment using a fleet of mobile robotic drive units, moveable shelves, work stations and sophisticated control software for pick, pack, and ship operations. To pick orders, operators stand at stations around the perimeter of the building while inventory is stored on mobile shelving racks, called pods. These pods are arranged in a grid pattern in the interior of the building; when an operator requires an item for an order, a mobile robot brings the pod containing that item to the worker’s station. The worker picks the items they need out of the pods and places them into the orders they are working on. Once the items have been picked, the mobile robots return each of the pods they are carrying to a storage location on the grid floor (which is frequently a different location than the one it picked the pod up from). Each worker is usually supported by 5-10 mobile robots so they are kept continuously busy filling orders. The Kiva system is useful for both split-case and full-case picking, and for fast as well as slow moving stock, across a wide range of product categories and industry verticals. All the inventory in the Kiva System is mobile so every worker has access to all products to fill complete orders at anytime.
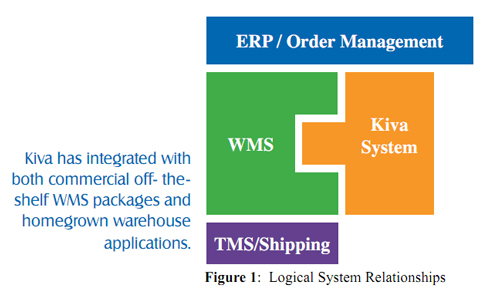
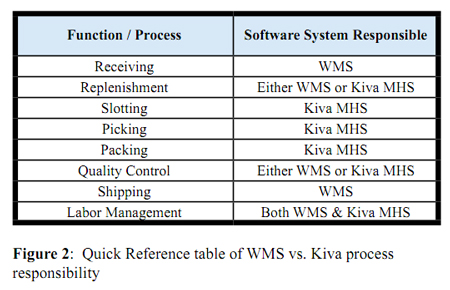
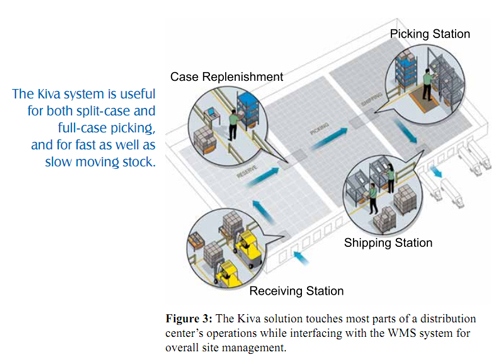
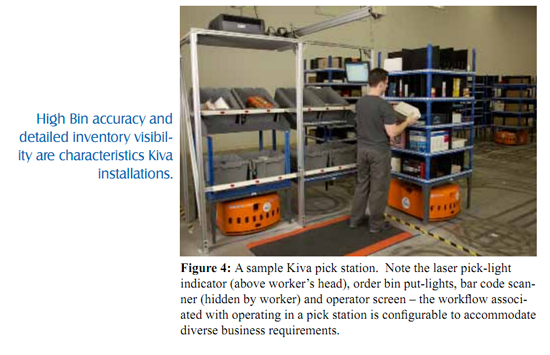
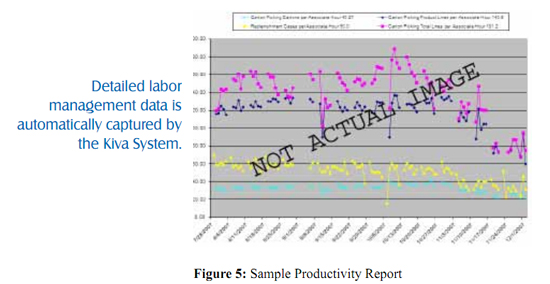
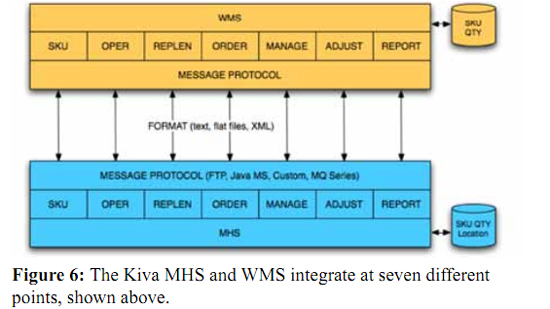
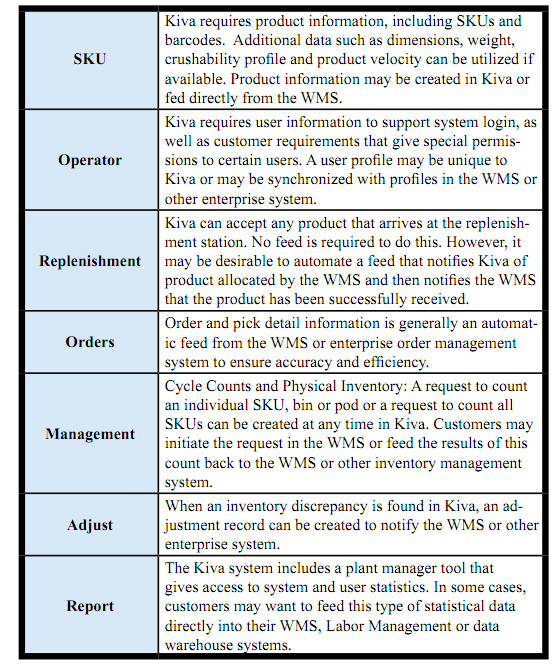
The content & opinions in this article are the author’s and do not necessarily represent the views of RoboticsTomorrow
Comments (0)
This post does not have any comments. Be the first to leave a comment below.
Featured Product
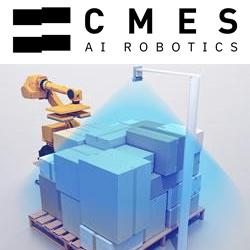