This cell is divided into 4 stations: A manual loading/unloading station and three process stations where tank openings are cut and numerous components welded on.
Contributed by | Axium
The objective of this finishing line is to process multi-layer HDPE fuel tank shells fabricated in a blow molding press. This cell is divided into 4 stations: A manual loading/unloading station and three process stations where tank openings are cut and numerous components welded on.
The operation sequence begins with an operator loading the tank and all the parts to be welded on the fixture. Once he scans the bar code and exits the cell, the rotary table rotates 90 degrees and the fixture is brought to the first processing station. Once all processes are completed by the robots at each station, the rotary table indexes once again. Fully processed tanks return to the manual loading/unloading station where an operator manually unloads the tank. This cell can process two different models of tanks with a fully automatic tool change and manual fixture changeover. The system can be easily retooled to process a third tank model by replacing the fixtures and tooling thereby keeping capital cost down.
Axium
Axium is specialized in robotic material handling and assembly. Axium designs, manufactures and installs a complete range of automated solutions for robotic material handling (palletizing, depalletizing, case packing, and peripheral equipments) and transformation of plastic products. Axium solutions meet all clients’ needs as for factory and manufacturing automation, in most industries: Food, dairy, consumer goods, beverages, tissue, distribution centers, folding carton, automotive.
The content & opinions in this article are the author’s and do not necessarily represent the views of RoboticsTomorrow
Comments (0)
This post does not have any comments. Be the first to leave a comment below.
Featured Product
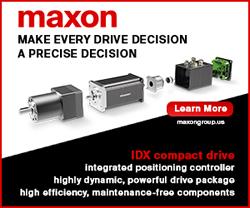