There is an increasing demand for collaborative robots that can work autonomously and adapt to changing production conditions. This requires reliable sensors that detect human presence and can overcome future challenges with the development of collaborative technologies.
White Paper from | SICK
|
|||||
|
|||||
Click here for more White Papers from SICK |
|||||
|
The content & opinions in this article are the author’s and do not necessarily represent the views of RoboticsTomorrow
Comments (0)
This post does not have any comments. Be the first to leave a comment below.
Featured Product
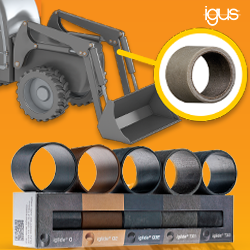