When faced with a multi-axis alignment and positioning application, motion engineers typically assemble a system from a stack of individual linear and rotary stages. This approach works well for applications when only a few degrees of freedom are involved (e.g. XYZ).
What is the Difference between Hexapod 6-DOF Alignment Systems vs Conventional Stacks of Stages?
Contributed by | Physik Instrumente
When faced with a multi-axis alignment and positioning application, motion engineers typically assemble a system from a stack of individual linear and rotary stages. This approach works well for applications when only a few degrees of freedom are involved (e.g. XYZ). But as applications become more complex, so do the equivalent stacks-of-stages, and very real and practical considerations begin to come into play.
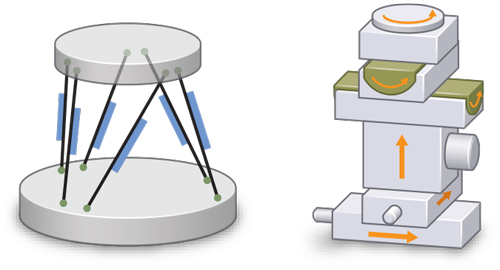
- Stiffness. Some stage manufacturers publish stiffness specifications in terms of axial deviation per unit force, but this is of little utility in estimating the dynamic performance of a stage …or a stack. A more pertinent metric is the resonant frequency, as it integrates both the effective coefficient of stiffness of a mechanism and the summed mass of its construction. (Accordingly, knowing Fres means you can easily estimate the possible step/settle time for a well-tuned closed-loop stage: approximately [3 Fres]-1). In our experience, most high-quality conventional linear stages will exhibit resonant frequencies on the order of 75-120Hz, unloaded. Stack them, and the resulting structure can have significantly limited responsiveness and long settling times.
Hexapods with cardanic Z-offset joints combine high stiffness with high precision as shown in the graphs above. Here, Y-axis motion of an H-811 hexapod is measured with a laser interferometer, to determine linearity and repeatability. For full travel moves, the RMS repeatability is ±71nm and ±55nm for 2mm travel. The X and Z performance is on the same level. (Image: PI) Learn more
- Inconsistent dynamics. The bottom stage in a stack carries the mass of the entire stack, and so on up to the top stage, which carries only the application load. So tuning is a laborious, axis-by-axis process, with different settings for each axis… and consequently different responsiveness.
Watch “Hexapod 6-Axis Systems for Micro Manufacturing / Fiber Alignment Operation” Video
- Inflexible rotation-centerpoint placement. Stacked stages place the center of their tip/tilt and rotation motions at the geometric centers of each rotation-stage and goniometer bearing. These can sometimes be arranged to coincide at a desired point in space (for example, at the focal point of a lens) via custom adaptor plates and fixtures, but this takes time and effort and is inflexible should application needs change. And significant changes can alter the dynamics of the stack, necessitating a re-tuning of each axis… again.
- Cabling. Cables are a fact of life in motion control, and managing them deserves more attention than it often gets. To begin, cables can be a conduit for vibration that can impact an entire application setup in un-obvious ways. Even one’s choice of draping the cables off an isolation platform can influence an application’s overall stability and performance in profound ways. As a stage moves, any cable being dragged along can contribute to parasitic motions and other errors. Stiff cables can do so even if arranged in a non-dragging manner. Cables can break and snag and come loose, contributing to premature failures that can be hard to diagnose. And generally, these problems scale with the number of axes in a user-stacked system. (Manufactured stacks sometimes benefit from integrated cable management.)
- Central aperture. Many applications–especially in optics–benefit from transmissive construction of the motion stack. This is difficult or impossible to achieve with a stacked structure of many axes.
- Size, weight and fragility. Simply stated, stacks can be substantial in height and mass. And since the bottom stages bear the burden of the entire tall stack, their bearings are vulnerable to brinelling and other damage from inadvertent forces. Besides inviting damage from elbow-knocks when set up, this often necessitates disassembly for shipping, adding cost and hassle and introducing variability when reassembled.
- Orthogonality and parasitic errors. Stacked axes interact in complicated ways; for example, runout in the X axis is seen as unwanted motion in the Y and Z axes; angular deviation of an axis similarly imparts motion in the travel-directions of the other axes, with magnitude proportional to the distance to the moving axis. And in stacks, that multiplicative lever-arm can be large.
Prototype of a novel labeling machine designed by PI in cooperation with Tirelli – watch video
Solution: Attack the Stack
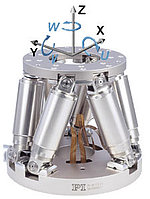
It may seem like hyperbole, but all these issues can be avoided by utilizing principles of parallel kinematics. Instead of a tall stack of all the necessary axes with the workpiece perched on top, such systems support a single workpiece in parallel by a tripod or hexapod structure, forming a much stiffer yet lighter-weight structure than is possible by stacking. The best examples of the breed utilize non- or minimally-moving internal cables with conveniently integrated cabling to the controller. User tuning requirements can be eliminated while providing precision and accuracy that can surpass the performance of some of the best available single-axis stages.
Today’s Easy-to-Use Controls
In prior years, the main obstacle to choosing this class of mechanism was the challenge of controlling the workpiece in a user-friendly way, using familiar Cartesian coordinates (X, Y, Z, θX, θY, θZ). This changed with the introduction of PI’s first hexapod two decades ago. That instrument utilized a fully-integrated industrial PC-based digital controller running clever firmware that transparently managed the coordinate transformation process, providing unprecedentedly flexible control in all six degrees of freedom with a programmable rotational center-point, settable by a single software command. A variety of software tools is available now for motion simulation and dynamic patterned motion generation in 6 degrees of freedom, such as used for vehicular simulation and airborne platform simulation and test. Read more: Patterned Motion Generation: Precision in the Time Domain
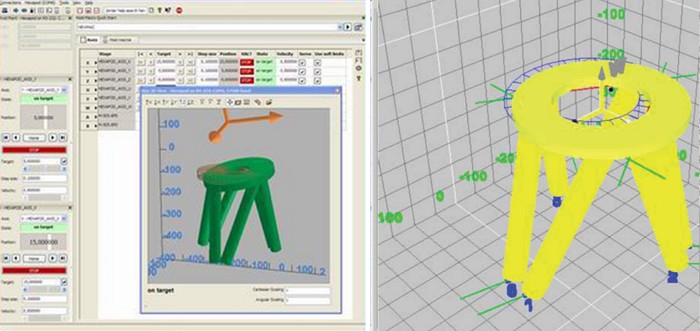
Simulation tools allow easy calculations of workspace and load limits, when hexapods are used in different orientations, or when loads are cantilevered. Collision avoidance software imports external objects and makes sure that critical positions are excluded by the controller.
One Stop, Many Solutions
These innovations set the tone for PI miCos’ broad array of parallel kinematic mechanisms: innovative solutions that can actually cost less than stacks of six stages of commensurate performance. Today’s offering benefits from years of continuous advancement in mechanical design and controls engineering. Our newest controller integrates an ultra-modern, industrial-class real-time operating system and provides such features and options as TTL motion triggers, analog position-waveform definition, standard internal data recorder with optional analog input, and a high-speed network interface for integration into factory automation systems and remote access. Its sophisticated software support includes comprehensive LabVIEW libraries, MATLAB support, a convenient GUI for setup and test, and well-documented dynamic libraries for Windows, Linux and OS X.
Two Families of Parallel Kinematics
PI offers two basic architectures for six-DOF mechanisms: six-legged hexapods, and three-legged planar parallel manipulators.
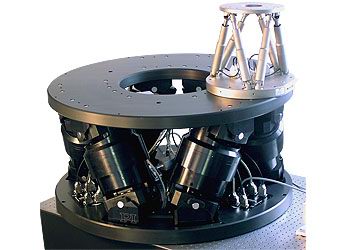
Hexapods
The hexapods utilize a variety of motion technologies for the actuator legs, ranging from brushed or brushless DC servo-motors to high-force PiezoWalk™ non-magnetic actuators. Both fixed- and extendable-strut designs are utilized depending on application needs.
Planar Parallel Manipulators
These innovative parallel mechanisms utilize three fixed-length legs in a tripod configuration, driven by three XY actuation modules which provide extended transverse travels for the assembly. Motion technologies can include piezomotors, rotary and linear DC servomotors, and stepper motors. Application story in x-ray diffraction imaging
Hexapod Systems Overview
Many Roles for Stacks
There is nothing wrong with serial kinematics. They work well for many applications and PI offers a large variety of standard and custom designs with stepper motors, piezo motors, and linear motors / air bearings. However, when 4+ degrees of freedom are required, the superior performance of a hexapod or hybrid tripod warrants a close comparison. A PI motion control engineer can help you evaluate advantages and shortcomings of both designs for your application. The benefit of a deeper toolbox and a global team with experience across a multitude of disciplines helps them draw on that experience in consultation with customers, choosing (or custom-developing) optimal solutions and cross-pollinating from related applications in other fields.
.jpg)
(left) Miniature XY-Rot stage (Ø20mm) based on Q-motion piezo motors (right) Multi-axis stacked stage based on stepper motors
A Closer Look at “Impossible” Requests!
Maybe they are impossible… or maybe they just require a fresh approach, or a trick from another application field. Mission-critical PI technology is at the heart of much of today’s cutting edge technology, including semiconductor manufacturing and metrology, photonics packaging and test, genomics, single-molecule biophysics, and ultra-resolution microscopy. Put our experience to work on your problems!
Experience
When we started working on parallel kinematic systems in the late 1980’s and early 1990’s, they were a novelty to many in the field of motion control. The persistent work of our engineers has led to easy to use, highy reliable systems. PI’s first international recognition for hexapod technology dates back to 1995 for the M-800 hexapod system.
1995 Photonics Circle of Excellence Award by Photonics Spectra Magazine for PI’s M-800 commercially available Hexapod 6-axis micropositioning system with controller and software.
The content & opinions in this article are the author’s and do not necessarily represent the views of RoboticsTomorrow
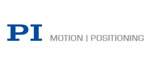
PI USA (Physik Instrumente)
PI is a privately held company that designs and manufactures world-class precision motion and automation systems including air bearings, hexapods and piezo drives at locations in North America, Europe, and Asia. The company was founded 5 decades ago and today employs more than 1700 people worldwide. PI's customers are leaders in high-tech industries and research institutes in fields such as photonics, life-sciences, semiconductors and aerospace.
Other Articles
High-Throughput PIC Production Needs Precision Alignment Equipment for Photonics Arrays, Fibers, Lenses
Fast Hexapod Improves Aircraft Manufacturing Process
Fiber Alignment and Photonic Chip Test & Assembly Just Got Easier
More about PI USA (Physik Instrumente)
Comments (0)
This post does not have any comments. Be the first to leave a comment below.
Featured Product
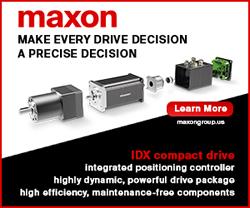