There are many reasons to transfer a product from one conveyor system to another. Whether you’re moving a product to another line for further operations, into a repair area, or into a rejection location, different transfer methods might be in order.
Five Methods to Transfer Products with Conveyors
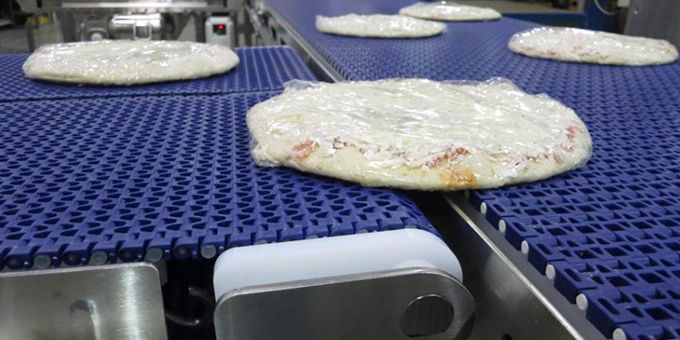
Article from | Dorner Conveyors
There are many reasons to transfer a product from one conveyor system to another. Whether you’re moving a product to another line for further operations, into a repair area, or into a rejection location, different transfer methods might be in order. This is equally the case with different size or shaped products. Knowing what transfer methods are available can help you decide what is required for your application.
Method 5: 90 Degree Transfer
This type of transfer operates from the belt edge to the frame edge of your conveyor system. Although conveyor speed should be aligned closely, it does not have to be
exact. As long as your product is of a size that can easily transfer from one conveyor to a perpendicular one smoothly, this design can offer an easy and inexpensive solution to many applications.
Method 4: Side Transfer
When choosing this type of transfer, be sure to check the design of your chosen conveyor system. Conveyor ends and frames should have minimal to no side protrusions. Not all conveyors are designed in this way. Side protrusions can easily get in the way or completely hinder the transfer of product from one conveyor to another.
Method 3: Inline Transfer
Also called end-to-end transfer, this method is when you butt two conveyors against each other. The most important thing when designing this type of transfer is to be sure that you’ve matched the two conveyor profiles. Also, be sure to pay particular attention to product size when choosing this method, so that the product does not have the potential to fall between the two conveyors, causing damage to the conveyor and the product.
Method 2: Nose Bar Transfer
For in-feed and out-feed to machinery as well as unit handling within a machine, consider a modular plastic belt small-pitch option that provides nose bar transfers as tight as 0.31-in. Traditional conveyors are designed to transfer large items with relative ease, but tight nose bar transfer is ideal for applications that involve small parts transfer from one conveyor to another, or from a conveyor onto a production area for additional assembly or packaging. Nose bars allow for additional clearance around the end of the conveyor, making the end more accessible and creating room for other machinery to be installed.
Method 1: Powered Transfer Modules
Challenges often arise when you need to move product from one conveyor to another in a very smooth operation. Powered transfer modules are available on most chain conveyors. Such modules are slave-driven, which allows the product to be transferred from one conveyor to another while maintaining both motion and speed for smooth inline part transfers. This is a particularly ideal solution when working with small parts because it easily integrates without eating up valuable space.
Wondering which product transfer is right for your system? Contact Dorner today to discuss the best way a transfer can optimize space, time, and efficiency within your application. This article was originally published in Machine Design.
The content & opinions in this article are the author’s and do not necessarily represent the views of RoboticsTomorrow
Comments (0)
This post does not have any comments. Be the first to leave a comment below.
Featured Product
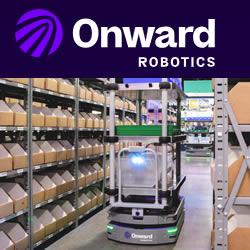