The speed / torque gradient is an indicator of a motor’s performance. The smaller the value, the more powerful the motor and consequently the less motor speed varies with load variations. It is based on the quotient of ideal no-load speed and ideal stall torque.
The Importance of the Speed-Torque Gradient in DC Motor Sizing
Warren Osak | Servo2Go
Often overlooked when sizing DC motors is the Speed-Torque Gradient.
The Speed-Torque Gradient is defined as Δn / ΔM [rpm/mNm] .
The speed / torque gradient is an indicator of a motor’s performance. The smaller the value, the more powerful the motor and consequently the less motor speed varies with load variations. It is based on the quotient of ideal no-load speed and ideal stall torque.
The speed torque-gradient can be considered a measure of the motor strength, which is defined by motor type and size and not the winding selected. Basically it’s how much speed drop the motor will have for each 1mNm of torque applied.
In the figure above, enhancing the load torque leads to a linear reduction of the speed. Thus it becomes clear what the meaning of Δn/ΔM is: It’s the gradient of the speed-torque line.
The content & opinions in this article are the author’s and do not necessarily represent the views of RoboticsTomorrow
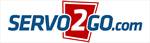
Servo2Go.com Ltd.
Servo2Go.com is an Online E-Store Distributor of Automation & Motion Control Systems & Components including: Servo Motors & Drives, Stepper Motors & Drives, Automation & Motion Controllers, HMIs, Positioning Systems & Actuators, Gearboxes, Couplings, Brakes, Encoders, Tachometers and Linear Displacement Transducers. Servo2Go.com is an ISO9001:2015 Registered Company.
Other Articles
Optimizing Servo System Performance: A Comprehensive Guide to Eliminating Electrical Noise and Enhancing Noise Immunity
Understanding the Motor Constant in DC Motor Sizing
Understanding Torque Ripple in Servo Motors
More about Servo2Go.com Ltd.
Comments (0)
This post does not have any comments. Be the first to leave a comment below.
Featured Product
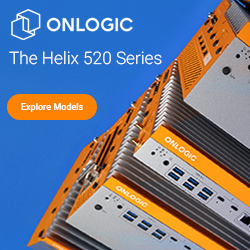