To increase productivity in production, more and more companies are deciding to link and automate their machine tools. The right automation system is crucial here. Robots and the appropriate gripping technology play an important role here.
Robots Automate Machine Tools
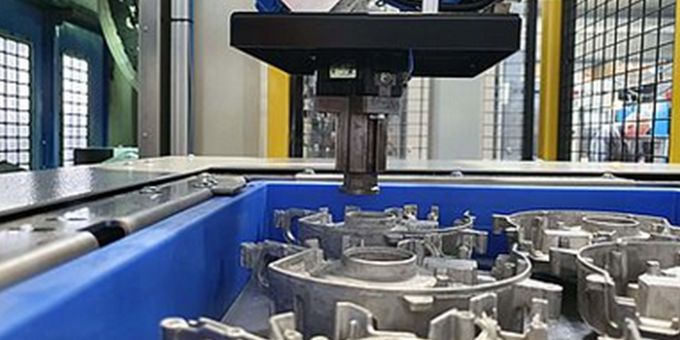
Case Study from | Zimmer-Group USA
Schwab CNC-Metallbearbeitung produces high-quality milled and turned parts for various industries - from prototypes to larger series in the field of aluminum and magnesium die-casting. Two machines for magnesium machining are now to be linked and automated in the company. The "Actuator Housing" workpiece is a magnesium housing component for steering gears in motor vehicles, the annual output is up to 250,000 units.
Both sides of the workpiece are machined one after the other on two machines: four times on the first machining center and individually on the second machine. At the same time, the machining area of the machines should be manually accessible for set-up procedures and to start-up parts. As an additional process, the marking of the workpieces after machining with a data matrix code is to be integrated into the automation sequence. The automation with robots was developed and implemented as a turnkey system by EGS Automatisierungstechnik.
Robots automate machining process
The starting point for the automation process was an existing Brother Speedio S1000 machining center, in which one side of the workpiece is machined in a 4-fold clamping. The existing clamping device, in which the components were previously inserted manually, was to be automatically loaded with as few modifications as possible. The total machining time and workpiece changeover is about 6 minutes for four parts, which was also the cycle time determining specification for the automation. A lateral loading hatch was retrofitted to the machine, which was integrated into both the machine's safety circuit and the safety circuit of the robotic cell.
The reach played a decisive role in the selection of the robot. In order to access all positions on the fixture, the robot must reach relatively far into the machine. Combined with the required precision in handling and inserting the parts and the necessary high travel speed, the choice fell on a Yaskawa GP25 industrial robot with a YRC1000 controller. The second important requirement was the autonomy of the automation system. The system should be able to produce autonomously for 12 production hours. This requires a storage capacity for 480 raw parts and 480 finished parts. The component dimensions of the geometrically complex workpiece are roughly 145 mm x 135 mm x 50 mm, the weight is around 200 g. The Sumo Ecoplex2 from EGS was used for this part storage and supply. This is a palletizing system for workpiece carriers up to a size of 600 mm x 400 mm.
The workpiece carriers are stored in stacks, de-palletized and made available to the robot for part removal, then palletized back after being filled with finished parts. In the version with infeed and discharge belts, the capacity is six workpiece carrier stacks for raw and finished parts. Commercially available and stackable plastic containers were selected as workpiece carriers. The workpiece-specific inlays, in which the components are picked up in exactly the right position, were designed by EGS and manufactured by Schwab using its own production capacities. The correct design of workpiece carriers is essential for the reliability of the subsequent automation.
Grippers for optimal positioning
Another important core component is the gripping technology. Here, gripping modules from the Zimmer Group are used. For example, a pneumatic three-jaw gripper of the GD300-C series was used for each of the systems. The three-jaw grippers consist of a robust housing made of a hard-coated aluminum alloy. They are driven by a double-acting pneumatic cylinder with round piston. The characteristic feature is the power transmission via a synchronized positively guided wedge hook gear; this enables high gripping forces by optimal deflection of the driving force. The three-jaw grippers concentrate on the essentials - on the most economical way of gripping in order to reduce production costs. The T-slot guidance of the GD300-C grippers ensures high force and torque absorption. It ensures high rigidity and combines this with a long service life in a compact design. The second side of the workpiece is machined in a second machine, a Brother Speedio S700. Here, too, automatic loading is carried out laterally through a special loading hatch. The machining of the second side is much less extensive and therefore takes much less time and is done individually here. Since the first machine is decisive for the system cycle, the four machined workpieces must always be removed from it immediately after the end of machining and four new blanks inserted. A combined deposit and turning station with four workpiece holders is used for intermediate storage of the semi-finished parts. Here, the robot places the components and picks them up again, turned, for loading the second machine.
In both machines, the components are largely freed from cooling lubricant after processing and before removal by means of a blow nozzle attached to the robot tool.
Protective device on the gripping tool
Once processing is complete, a data matrix code must be applied to each component using a marking laser. As a system manufacturer, EGS Automatisierungstechnik is responsible for ensuring laser safety. This is achieved by means of appropriate protective devices on the gripper tool and appropriate sensor technology that reliably monitors that the laser can only work if the protective barrier reliably covers the marking area. During the marking process, the workpiece is held securely in position by the robot, and any vapors produced are extracted. After successful marking, the robot places the finished part back into a workpiece carrier, which is palletized onto a finished part stack in the palletizing system. The workpiece carrier stacks of raw and finished parts are set up and removed on one operating side of the system.
Robot controller takes command
All processes are controlled by the YRC1000 robot controller and the entire system is operated via the robot's handheld device. Profinet serves as the interface to the two machines. The system cycle time was even slightly undercut, so that the robot is currently faster than the first machine, which determines the cycle time.
The content & opinions in this article are the author’s and do not necessarily represent the views of RoboticsTomorrow
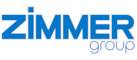
Zimmer Group US, Inc.
Are you interested in premium products in the fields of mechanical and plant engineering? Do you want to learn more about our solutions in the fields of automation, damping, linear, processing, tooling, and machine tooling technology?
Other Articles
Automate 2025 Q&A with Zimmer Group
Converting Passenger Aircraft to Freight Aircraft - the Zimmer Group Is on Board!
Automated Loading and Unloading of CNC Machines
More about Zimmer Group US, Inc.
Comments (0)
This post does not have any comments. Be the first to leave a comment below.
Featured Product
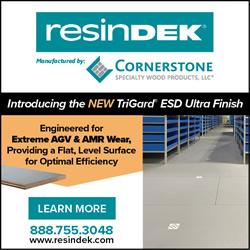