On the surface, anti-static sounds like the right choice. Anti-static means no static, right? Not quite. Read on to learn the key differences between anti-static flooring and electrostatic dissipative (ESD) flooring.
Electrostatic Dissipative Flooring vs. Anti-Static Flooring: Which Flooring is Right for Your Facility?
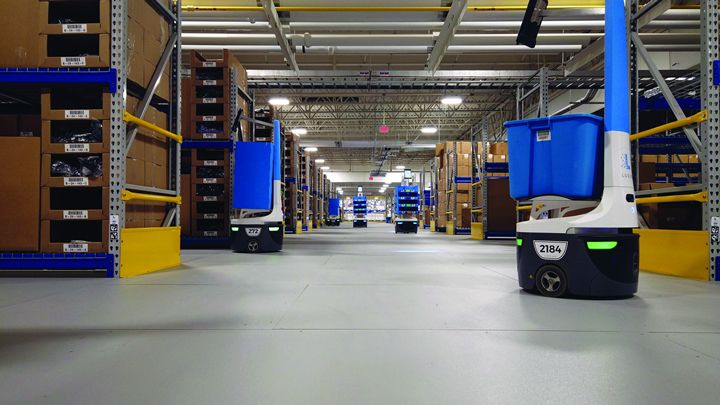
Article from | Cornerstone Specialty Wood Products
The risk of unwanted static discharge can range from a person experiencing an uncomfortable static shock - to the damage of expensive equipment - to a spark that could cause an explosion in a flammable environment. Anti-static flooring and ESD flooring both prevent a person from building up a charge as they walk across the floor, so they do not get shocked when they touch something that conducts electricity.
On the surface, anti-static sounds like the right choice. Anti-static means no static, right? Not quite. Read on to learn the key differences between anti-static flooring and electrostatic dissipative (ESD) flooring.
What is Anti-Static Flooring?
Anti-static flooring conveys its purpose in its name. This type of flooring does not create static. It does not mean the floor will eliminate static buildup or dissipate static that may have already been built up. It simply prevents the creation of new static from the friction between an object or person moving across the surface. Anti-static flooring typically keeps the voltage buildup under 3000 volts, the amount required for someone to feel a shock, although some people may feel static at 2000 volts.
What is Electrostatic Dissipative (ESD) Flooring?
ESD flooring (also known as conductive flooring) greatly reduces the elimination of static buildup and dissipates triboelectric charges. In fact, ESD flooring provides controlled dissipation and grounding of triboelectric charges with direct pathways of statically generated charges. The intentional flow of electrical current and discharge helps to immensely eliminate the potential of accidental electrostatic discharge, which can damage sensitive equipment. ESD limits the discharge to under 50 volts.
Do I need ESD Flooring and Anti-Static Flooring?
If you work in an industry where electrostatic buildup could be detrimental and lead to damage of products, such as electrically sensitive devices or equipment that is susceptible to damage such as robots, then ESD flooring is nonnegotiable. The protection it provides is invaluable. The same is true for employers that want to protect their employees from static shock. In industries where static is more of an inconvenience and employees spend little time on the floor then anti-static flooring is often sufficient.
Fortunately, ResinDek flooring panels are available with ESD protection. ResinDek Gray Diamond Seal ® 2 ESD is a fully compliant, certified ESD floor. It is often used in distribution centers that store clothing or use large amounts of electronics and automation. For industries that use Autonomous Mobile Robots (AMR) or Automated Guided Vehicles (AGV) we recommend ResinDek flooring panels with our TriGard coating. ResinDek with TriGard is engineered specifically to endure the consistent, repeated travel patterns associated with AMRs and the defined travel paths of AGVs. The TriGard coating has a 5x wear resistance over our commonly used Gray Diamond Seal 2 coating and is designed to withstand 10 years of high-frequency, repeat traffic. The TriGard finish comes standard with ESD.
For facilities that do not require a fully compliant ESD floor but want to limit static buildup, then ResinDek with Gray Diamond Seal 2 is your flooring solution. ResinDek with Gray Diamond Seal 2 has an anti-static solution applied to the panel during the coating process.
The content & opinions in this article are the author’s and do not necessarily represent the views of RoboticsTomorrow
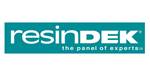
ResinDek / Cornerstone Specialty Wood Products
As the manufacturer of ResinDek® panels, we have been at the forefront of testing and innovating flooring panels for the Material Handling Industry since 1994. In 2007, we began providing ResinDek panels for automated warehouse distribution robots. Much of our initial research and development occurred with Automated Guided Vehicles. In the last decade, we have provided a variety of ResinDek engineered flooring products to numerous Automated Guided Vehicles (AGV) and Autonomous Mobile Robot (AMR) manufacturers for their testing labs. As a result, millions of square feet of ResinDek panels are in service worldwide with robotic traffic in distribution centers, warehouses, microfulfillment centers, and retail environments.
Other Articles
Upgrade Your Mezzanine Flooring While Avoiding Timely and Costly Replacement
Sneaker and Sportswear Retailer’s New Mezzanine and Ground Floor Feature ResinDek Robotic Flooring
Investing in AGVs or AMRs? 6 Ways Engineered Mezzanine Flooring Maximizes Implementation Success
More about ResinDek / Cornerstone Specialty Wood Products
Comments (0)
This post does not have any comments. Be the first to leave a comment below.
Featured Product
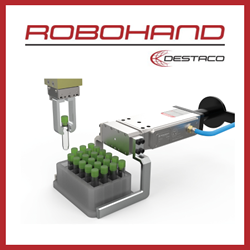