An exoskeleton must be lightweight, compact, powerful, reliable, and easy to use – what could be easier? Many developers around the world dabble in this discipline with different degrees of success.
How to Design an Exoskeleton
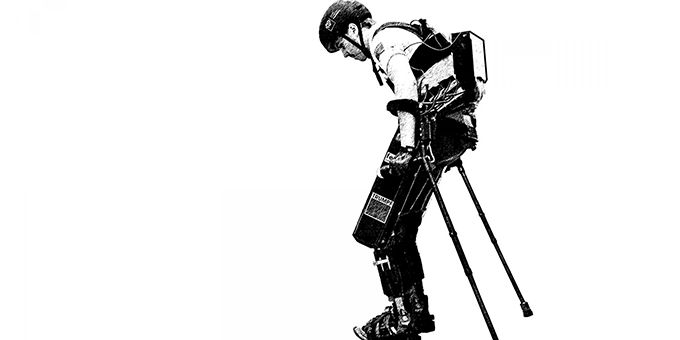
Article from | maxon group
Mechanics
“Emulating the human gait with mechatronic systems is a huge engineering challenge. The structure that supports the person must be as light as possible yet also robust, as every additional kilogram has an impact on the drive systems. For this reason, lightweight materials such as carbon are often used. It is also important that the exoskeleton is not too broad, as the pilot must be able to pass through any door without difficulty.”
Drives
“The drive systems, consisting of a motor and gearhead, must deliver high torque. Enormous forces are at work, especially when walking up and down stairs. At the same time, a high level of dynamics is required, as the motors must constantly change the direction of rotation due to the walking movement. The final item on the wish list is a compact design that takes up as little space as possible.”
User interface
“The pilots need to have complete control over their locomotion, so the movement controls must be easily accessible and intuitively designed. Furthermore, to ensure that the nterface reliably transmits the large forces at play while also protecting the sensitive skin of the pilot, it must be individually adjusted to the pilot’s legs and torso.”
Pilot and experience
“This is arguably the most important point. How well an exoskeleton works in practice depends primarily on the pilot, who must get used to the robotic assistance and learn how to use it to best effect. Some people rely more on strength, others more on technique. Either way, it requires a huge amount of training.”
Degrees of freedom
“How many degrees of freedom should there be? That’s a tricky question. Exoskeleton designers often opt for two degrees of freedom per leg, so only the hip and the knee move. The benefits of this are: less weight, a simpler control system, and therefore fewer sources of error. However, it is possible to have three or four degrees of freedom. This means that you can have lateral movement, for example, or additionally actuate the ankle. This gives the pilot extra freedom of movement and increased stability on uneven ground. On the other hand, this makes the entire system heavier and more complex, and also decreases the battery life.”
Software
“At first glance, controlling fewer degrees of freedom seems simple. However, when you get down to the detail, the implementation is rather more complex. This is because many different movements must be controlled and accidents prevented by safety features. In addition, the entire exoskeleton should be developed further in cooperation with the pilot. This can only be achieved with a viable software architecture.”
Christian Bermes is Team Leader at VariLeg enhanced and Professor for Automation and Mechatronics at HSR University of Applied Sciences, Rapperswil.
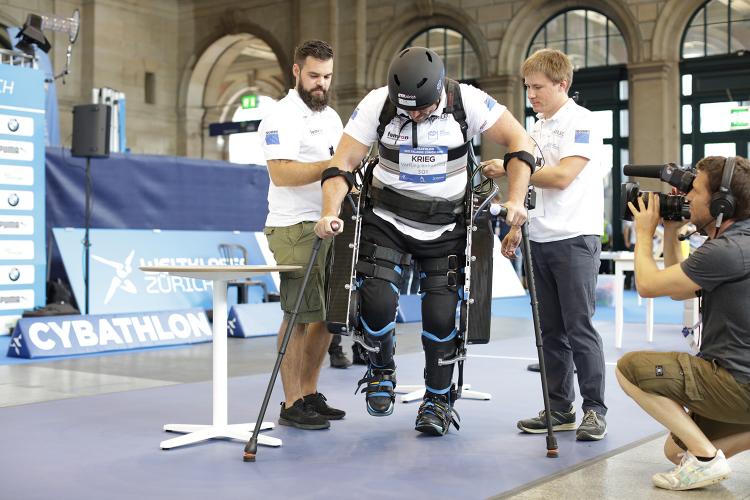
New VariLeg exoskeleton with motors twice the power
The VariLeg enhanced team is developing and building an exoskeleton for the Cybathlon 2020. However, the ongoing project has little to do with the VariLeg team from ETH Zurich that took part in 2016. The current exoskeleton was developed as a student project. A mixed team from ETH Zurich and the HSR University of Applied Sciences Rapperswil is now working on the completion of the robotic system. The system has two degrees of freedom. There are two brushless flat motors from maxon on each side to move the hips and knees. These deliver up to 600 W of power.
The content & opinions in this article are the author’s and do not necessarily represent the views of RoboticsTomorrow
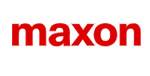
maxon group
maxon is a leading supplier of high-precision DC brush and brushless servo motors and drives. These motors range in size from 4 - 90 mm and are available up to 500 watts. We combine electric motors, gears and DC motor controls into high-precision, intelligent drive systems that can be custom-made to fit the specific needs of customer applications.
Other Articles
Multi-axis motion control drives pipe-based robots
Automate 2025 Q&A with maxon group
Understanding Torque and Speed in Electric Motors
More about maxon group
Comments (0)
This post does not have any comments. Be the first to leave a comment below.
Featured Product
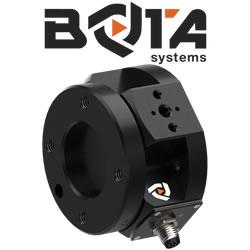