Last month, Stäubli introduced 5 new models of tool changers to round out our MPS product line. These new models open up much of the smaller payload robots to using tool changers.
Staubli Rolls Out 5 New Models of Robotic Tool Changers
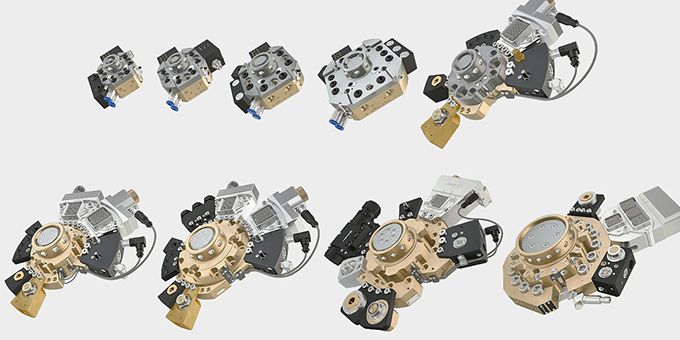
Q&A with Denny Savage, Robotic Tool Changer Business Unit Manager | Staubli
Tell us about yourself and your role with Stäubli.
I have been involved with automation components for 35 years and I am currently the robotic tool changer Business Unit Manager for North America with Stäubli Corporation. I’m responsible for all projects related to the tool changer product line.
Give us some details about robotic tool changers and where they are being used?
It is a mechanical quick disconnect device that structurally handles the robot load while having the capability to switch out different EOAT. With that, it passes the utilities required to operate the EOAT. Tool changers offer additional flexibility to robots. The flexibility comes from a single robot changing tools to handle multiple operations. Another major consideration when deciding on whether to include robotic tool changers in your factories is when floor space is not available or at a premium.
Tool changers are being used whereever robots are used. With the expected expansion of robots into new markets it opens up all industries to the use of tool changers.
What is new in the Stäubli world of robotic tool changers?
Last month, Stäubli introduced five new models of tool changers to round out our MPS product line. This expansion opens up much of the smaller payload robots to using tool changers. These applications will be ones that call for high accuracy along with the normal pick-and-place and vision requirements.
What do you feel sets a Stäubli robotic tool changer apart from the others?
High accuracy, product flexibility, many standard modules to transfer utilities to the tool along with quick delivery at a budget-friendly price.
Can you share some real world examples of tool changers in use.
One of the most common is in the automotive industry body shop. Robots are changing out weld guns, riveting heads, dispensing wax and material handling (grippers/clamps) to simply move product in and out of a given process.
Another growing area is the increase use of servo drives on tooling. This has been more common in the Aerospace/Defense industry where high levels of accuracy and repeatability are demanded. The Staubli tool changers provide the precision required and the flexibility to mount numerous electrical connectors for the utilities required to operate the servo tooling. Flexibility and modularity of design becomes paramount in this environment.
What are some of the barriers to using robotic tool changers and how can they be overcome?
A common barrier is cycle time. The cycle time required to hand-off a tool and pick up a new one needs to be accounted for. Keep in mind a need for manufacturing flexibility must be present. A large volume, high speed, dedicated production line isn’t necessarily going to be a good candidate for tool changers. The space required for tool stands and the unused tools needs to be considered in the design phase, along with the maintenance of any added component needs to be part of a good PM plan.
Take a look down the road a few years, what new technological advancements do you see coming out for robotic tool changers? Do you see new applications for them?
Any new applications will be only limited by where robots are being installed. We have a tool changer for most robots on the market. New advancements will be in the area of Smart Tool Changers. Staubli is developing tool changers that will assist in the early detection of component failure which leads to costly downtime. These devices will count cycles, send alerts for maintenance, transfer information to the controlling PLC, etc. All valuable to the Industry 4.0 smart factory.
If a company is interested in robotic tool changers, what is involved?
I suggest contacting one of our Stäubli MPS Specialist via phone or email (thru the Stäubli website). The application can be discussed including the tooling requirements and then a number of solutions will be provided. Stäubli can quote catalog standard components that are in stock and/or custom components for the best possible solution.
For more information click here or call 313 549 4636.
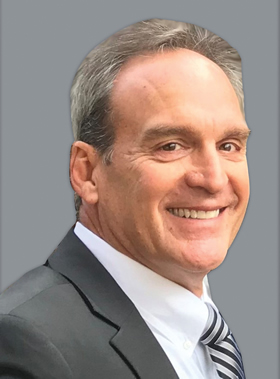
Denny Savage graduated from Michigan Technological University with a Bachelor’s degree in Mechanical Engineering. He started with Staubli in 2015 and has been involved with robotic automation for 35 years.
The content & opinions in this article are the author’s and do not necessarily represent the views of RoboticsTomorrow
Comments (0)
This post does not have any comments. Be the first to leave a comment below.
Featured Product
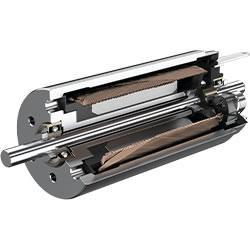