Leveraging third-party hardware, such as a robotic picking arm, and software, such as customized WMS, is crucial if you want true flexibility in your robotics system.
True Flexibility in your Robotics System
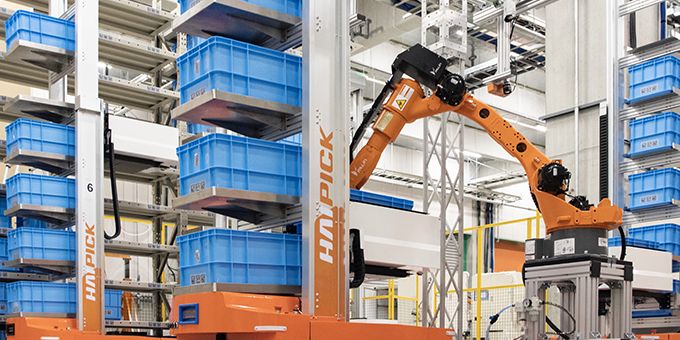
Q&A with Luke Lee, Head of Marketing, Americas | HAI Robotics
Tell us about yourself and your role with HAI Robotics.
HAI Robotics is the pioneer and leader in autonomous case-handling robotic ("ACR") systems, which provide efficient, intelligent, and flexible warehouse automation solutions through advanced robotics and AI, and recently closed $200 million in funding. As the marketing head of the Americas region, I focus on growing our manufacturing and warehouse automation footprint through digital marketing, events, media relations, and other various business development activities.
Before joining HAI Robotics, I led the marketing efforts in the Americas for Geek+, a robotics company, and I received a B.S. in Aerospace Engineering and B.A. in Economics from the University of California, San Diego (UCSD). I am also the current CEO of 4V Inc, a virtual entertainment company specializing in providing a platform for content creators of the future.
A fan of baseball, American football, and soccer ("football" to the rest of the world!), I'm also an avid travel enthusiast, and you may find me scuba diving in a random place on a map.
© HAI Robotics
How reliable and efficient are the latest robotics systems and how does that compare to the first-generation robotic systems that created such a revolution?
Some of the latest solutions feature comprehensive software and intelligent algorithm platforms that ensure reliability, redundancy, and 24/7 monitoring. Conversely, many older systems are very hardware-centric with single points of failure and are challenging to monitor and upgrade.
How would you describe the evolution of those initial, groundbreaking robotics systems to what's available in the market today?
The initial robotics systems tended to be big and bulky, hardware-centric, relatively inflexible, and required long deployment times that took months to years, depending on the design, let's say, for a warehouse. Fast forward to some of today's that feature comprehensive & advanced software platforms, flexible architectures, and deployment time in a matter of weeks.
Why is it so important that robotic systems work ("play nice") with other robotic systems and do you see this occurring yet?
Because not everyone uses the same thing, and different customers have different requirements. While some are designed intentionally as a closed system, leveraging third-party hardware, such as a robotic picking arm, and software, such as customized WMS, is crucial if you want true flexibility in your robotics system.
What are the biggest obstacles you are seeing in integrating robotics systems into business?
The biggest obstacles we see are software integration with legacy systems, business process mapping, understanding and addressing the customer's workflow and pain points, and compliance with local regulations and OSHA standards.
So, what's the next "big thing" (technology or otherwise) in the robotics world?
It's all about continued innovation in software. More and more sophisticated software, including AI, machine language, visual capabilities, may enable robots to accurately pick, pack, and ship with 100% automation without an operator present.
I think there are two key tracks for the next "big thing" –
Software – robotics systems driven by sophisticated and comprehensive software platforms featuring AI, advanced vision capabilities, 100% accuracy, and approaching 100% automation without an operator present.
Flexibility and scalability – customizable for the unique warehouse automation transformation requirements of the client and offering the ability to start small and quickly expand as the business dictates.
The net result of that will be breakthrough capabilities for improving operating efficiency and storage density.
The content & opinions in this article are the author’s and do not necessarily represent the views of RoboticsTomorrow
Comments (0)
This post does not have any comments. Be the first to leave a comment below.
Featured Product
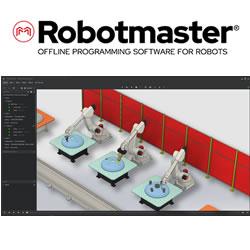