The palletizing magnet design recently modified by Goudsmit Magnetics consists of modules that vary in design. The low-maintenance magnet is suitable for palletizing and depalletizing cans, aerosols, canisters and glass jars with steel lids.
Low-maintenance Palletizer Magnet Saves Robot and Manpower
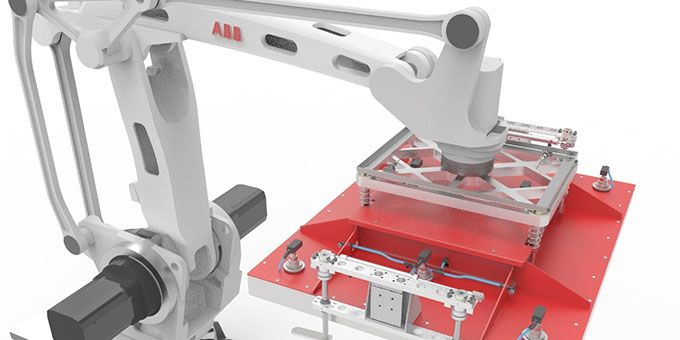
Case Study from | GOUDSMIT Magnetics
The modular construction offers users, such as integrators, packaging companies, food producers or pharmaceutical companies, a number of choices that save on an extra robot and manpower. For example, a lightweight version, or the choice of a spring suspension unit. This is a spring suspension unit that provides a flexible spring path, prevents product damage and enables correct positioning. The options vacuum system and/or pallet gripper ensure that actions such as removing a pallet, laying down or removing an intermediate sheet between a layer of cans can be performed by one robot. The costs saved by the user ensure a quick return on investment for this new system. The palletizing magnet is shown at the Automatica 2022 in Munich.
Implementation
The central scissor mechanism consists of two cylinders that ensure an even switch-on and switch-off of the palletizing magnet and drive the sheet in one go. This ensures a parallel force distribution, which is not always the case when four cylinders are used. The integrated vacuum system is designed to pick up and process any format and type of intermediate sheet. The parallel switching mechanism guarantees a low-maintenance, trouble-free production process, even when loaded unevenly, for example when picking up an uneven layer. The magnet can be equipped with several pole systems. This makes the field stronger at the surface for light cans or aerosols and deeper for heavier loads, such as filled (canning) cans.
Safety and durability
The palletizing magnet is easy to operate with pneumatics and is equipped with sensors for on/off detection. The spring suspension unit makes positioning easy and prevents product damage. In addition, it is equipped with sensors that prevent tilt (canting) and jamming, as well as the robot crashing in case of irregularities. In an automated environment, safety is an important aspect. The use of a permanent magnet means that the load remains on the magnet even when energy is lost. This greatly reduces the chance of unsafe situations and damage. Switching with only an air pressure pulse also makes it a very durable and energy-efficient solution.
Maintenance
The palletizing magnet has a long life, is very maintenance friendly and uses little air. Any wear parts are easy to replace. The company supplies the lightweight palletising magnet to various customers worldwide. In some places the system runs continuously for 24 hours a day. Even then maintenance is minimal.
The content & opinions in this article are the author’s and do not necessarily represent the views of RoboticsTomorrow
Comments (0)
This post does not have any comments. Be the first to leave a comment below.
Featured Product
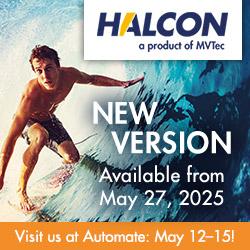