BitFlow's BitBox™ Simplifies Integration and Control of Multiple Machine Vision Devices in High I/O Applications
Machine makers in high-density I/O vision applications are challenged daily to find cost-effective, reliable ways to continuously control dozens of devices such as strobes, solenoids, and actuators, as well as to acquire data input from equipment ranging from photo detectors to triggers. Until now, the answer has been to purchase an I/O card yet this step requires additional costs, software, system complexity, and the use of a PC slot.
WOBURN, MA, JUNE 1, 2016 -- Machine makers in high-density I/O vision applications are challenged daily to find cost-effective, reliable ways to continuously control dozens of devices such as strobes, solenoids, and actuators, as well as to acquire data input from equipment ranging from photo detectors to triggers. Until now, the answer has been to purchase an I/O card yet this step requires additional costs, software, system complexity, and the use of a PC slot.
To meet this challenge, BitFlow has launched a revolutionary new I/O box that outperforms traditional I/O cards. The BitFlow BitBox™ provides an unprecedented 36 inputs and 36 outputs in a compact, DIN-rail mounted form factor that supports TTL, LVDS, open collector, opto-isolated and 24V signaling. Amazingly simple to deploy, the BitBox™ is controlled solely by a BitFlow frame grabber, using the same API, driver and manual. As a result, the machine maker achieves significant cost savings, while reducing space requirements and flattening the learning curve for customers. In addition, this arrangement isolates noisy, high-voltage signals generated by the PC away, keeping them away from the machine where they could cause data drops, video problems, malfunctions and random network errors.
Traditional I/O cards put all transmitters and recievers on the actual board in the PC. This requires bringing I/O wires from their sources to the PC, which is often located quite a distance from other equipment. With the BitBox, all transmitters and recievers are situated right in the BitBox, on the rail, close to the other equipment. A small high-speed 15-wire cable runs between the BitBox™ and the frame grabber. Maximum length cable is a generous 10 meters, providing maximum flexibility in positioning equipment within the machine.
The BitBox™ contains 12-pin connector blocks that can be added or removed easily, but still lock securely in place for factory floor reliability. Blocks are logically grouped by signal type and have snap-in connectors that allow the fabrication of a harness without directly wiring the BitBox™.
The BitBox was designed with maximum flexibility in mind. For example, outputs can elected to be driven either to the static level via software API or configuration files, or from a frame grabber's internal signal generators. Likewise, inputs can be routed to a number of different blocks on the frame grabber. Input signals can also be routed to other outputs, including to the camera where it can also cause an interruption, or start/end acquisition.
The BitFlow BitBox™ is scheduled to ship in the third quarter of 2016. For more information, please call 781-932-2900 or visit www.bitflow.com.
About BitFlow
BitFlow has been developing reliable, high-performance Frame Grabbers for use in imaging applications since 1993. BitFlow is the leader in Camera Link frame grabbers, building the fastest frame grabbers in the world, with the highest camera/frame grabber densities, triggering performance, and price. With thousands of boards installed throughout the world, into hundreds of imaging applications, BitFlow is dedicated to using this knowledge and experience to provide customers with the best possible image acquisition and application development solutions. BitFlow, located in Woburn, MA, has distributors and resellers located all over the world including Asia, the Americas, and Europe. Visit our website at www.bitflow.com.
# # #
Featured Product
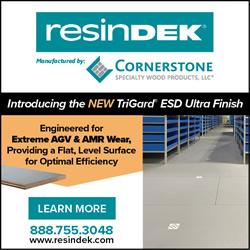