AGILOX Autonomous Mobile Robots are substantially saving costs by applying Artificial Swarm Intelligence
Swarm Intelligence (SI) and bio-inspired computing have attracted great interest in almost every area of science and engineering, including robotics, over the last two decades.
Being an innovative manufacturer of autonomous mobile robots (AMRs), AGILOX directs most of its effort into developing one of the most unique robotic material handling features on the market - completely decentralized autonomy. AGILOX Intelligent Guided Vehicles (IGVs) are completely independent, self-controlled, and intelligently designed to handle failover, recovery, and deadlock prevention perfectly. Our SI system can provide real-time solutions to impossibly complex optimization problems in the most efficient way possible, often in ways that a human designer could never anticipate. The swarm can also handle unexpected changes in dynamic environments without any human intervention.
AGILOX vehicles automatically exchange information about the environment and the current work order situation with each other via WiFi several times per second. Based on virtual transport costs, which each participant constantly recalculates for all pending orders, it is automatically decided which vehicle fulfills an order and which path that vehicle can take to fulfill this order in the shortest amount of time.
All of this is possible with almost no overhead cost to the end-customer. There are no expensive server systems, no wires added under the floor, no reflector or beacon installations - no hardware of any kind, other than your regular 2.4 or 5 GHz WiFi network and the charger. There is no software to install or maintain, no version numbers to keep up with, and no licenses with ongoing subscription fees.
The nature of our Swarm Intelligence also provides another massive advantage in terms of setup cost. Once the first AGILOX unit learns its environment and workflow details, the system becomes immediately infinitely scalable. Adding additional vehicles to the swarm to increase throughput is as simple as turning on the power and assigning an IP address. Within minutes, the new vehicle will automatically download all of its configuration information from the swarm and begin working, no additional commissioning or programming required.
AGILOX represents a total departure from the traditional approach to material handling processes. We apply the principles of our decentralized IGV system to our entire business model from top to bottom as well, by providing our customers with the training and tools to perform their own maintenance and expand or modify the system as they see fit.
With open interfaces, infinite flexibility, and unrivaled collective intelligence, the possibilities for your AGILOX implementation are limited only by your imagination. Welcome to the future of logistics automation.
For further information, please visit us at www.agilox.net
About AGILOX
AGILOX is an innovative, fast-growing company that develops and manufactures intelligent logistics robots (AGV’s, AGC’s, AMR’s) that use "swarm intelligence" to intelligently navigate through warehouses and factories, delivering pallets and totes where they are needed. Headquartered in Austria, AGILOX was established in 2009 by a group of visionary engineers. Presently, the company continues its growth and expansion with offices in 15 countries worldwide, including Atlanta, USA.
All aspects are developed in-house, from mechanical design, electrical engineering, navigation, and related software. This allows for faster reactions to changing requirements and customization depending on the customer’s requirements.
Comments (0)
This post does not have any comments. Be the first to leave a comment below.
Featured Product
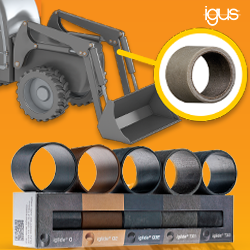