Three-quarters of total robot sales are currently attributed to just five countries — China, the Republic of Korea, Japan, the United States and Germany.
Who’s Winning the Robot Race?
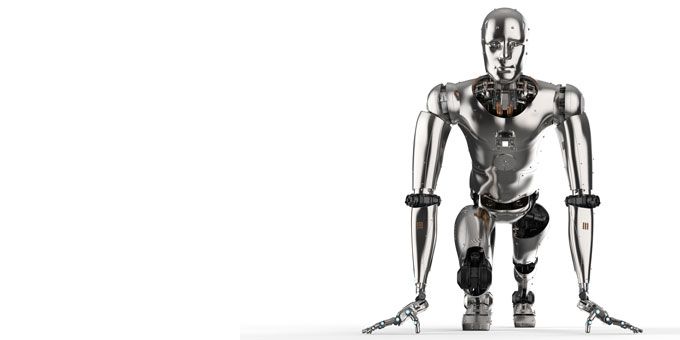
Nigel Smith | TM Robotics
Until a few years ago, the phrase ‘Industrial Revolution’ was largely associated with radical engineering changes that transformed industry. Two centuries later, we’re experiencing another shift in the manufacturing landscape, the Fourth Industrial Revolution (4IR). Nigel Smith, CEO and president of industrial robot distributor TM Robotics, investigates who is leading the way in the race for automated production.
Statistics from the International Federation of Robotics (IFR) prove that the number of industrial robots used in production is increasing rapidly. However, three-quarters of total robot sales are currently attributed to just five countries — China, the Republic of Korea, Japan, the United States and Germany.
Asia has long remained the strongest market for robotics. Of the record breaking 380,550 robot units sold globally in 2017, a significant percentage of these will have been deployed to Asian factories. In fact, the region reported record-breaking robot sales for the past four years in a row, rising by 19 per cent in 2017.
Asia has pulled out all the stops to remain at the forefront of this arena. Back in 2015, the Chinese government announced Made in China 2025 (MiC2015). The national initiative aims to reboot the country’s manufacturing sector, with an objective of China becoming the world’s largest user of robots.
Similarly, Japan launched its own transformation project in 2017, named Society 5.0. The scheme aims to go beyond Germany’s 2011 Industrie 4.0 initiative by considering the challenges that these new technologies will bring to society, rather than solely focusing on their use in manufacturing.
Regardless of the phrase or buzzword used to describe these changes in manufacturing, almost every nation is upping their game.
According to the World Robot Statistics, 74 robots per 10,000 employees is the world’s average robot density. The United States sits comfortably above this, at 189 robots per 10,000 employees. In 2016, the country began to climb the robot density ranks and today, the US ranks seventh in the world, behind South Korea, Singapore, Germany, Japan, Sweden and Denmark.
This figure has been significantly boosted by the necessary modernization of US production facilities, as well as a growing demand for products made in the US. What’s more, robot sales in the country are expected to increase by at least 15 per cent per year between now and 2020.
Europe, the world’s second largest market for industrial robot sales, has also increased its volume of robot deployment. Purchasing 56,000 units in total, the continent reached a new peak for robot sales for the third year in a row. That said, much of this deployment was attributed to Germany, currently the fifth largest robot market in the world.
Much of Europe’s deployment of robotic technology is related to the automotive industry. It’s therefore no surprise that the champions for robotics in Europe are those with a strong automotive presence — Germany, Italy and Sweden.
Automotive manufacturers have long used six-axis robots in their production. Looking to the future, increasing the volume of robot deployment will rely on the small to medium-sized companies also investing in automation.
To reach this market, industrial robots must become more accessible, in relation to both cost and user experience. The results of TM Robotics’ Global Robotics Report 2018 stated that simple programming was one of the most important features when choosing a SCARA, Cartesian or six-axis model —79 per cent of respondents named this as a top five consideration.
Easy robot programming is not only an attractive feature for new users, but provides established users with reduced programming time. Growing demand for easily programmable robots is also evident in the rapid increase in sales of collaborative models — robots that can work without protective barriers between machine and employee.
Collaborative robots, or cobots, currently account for 3 per cent of the total robotics market, but this figure is expected to reach 34 per cent by 2025. These machines have been marketed as easy to program, but despite this, they should not be considered as a total alternative to traditional industrial robots.
While cobots do boast some impressive responsive features, these machines generally cannot tackle the dangerous, repetitive and heavy-duty tasks usually associated with industrial robots — and respondents to the Global Robotics Report agree. 55 per cent do not believe that cobot technology is advanced enough to deliver the performance require for manufacturing, and a further 25 per cent are unsure of their capabilities.
There is no one-size-fits-all solution for automating a facility. While the growth in the cobot market represents cobots as an ideal first step towards automation, there’s more than one route to deploying robotics in a facility.
Unlike the first Industrial Revolution, today’s manufacturing industry is fiercely competitive. Not only are nations contending to increase the volume of robots they deploy in their facilities, but new types of robotic technologies are emerging to take on new tasks and operations.
The IFR predicts that the industry will experience a further boom in 2019, with an estimated 2.6 million robot units set to be deployed. There’s no denying that Asia is currently dominating the robotics market, but with such rapid changes happening in a relatively short period of time, there’s scope for other nations to catch up.
The content & opinions in this article are the author’s and do not necessarily represent the views of RoboticsTomorrow
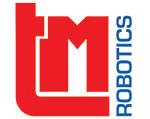
TM Robotics (Americas) Inc
TM Robotics, in partnership with Shibaura Machine, formerly known as Toshiba Machine until 1st April 2020, offers a comprehensive range of industrial robots ideally suited for high-precision assembly, machine loading/unloading and material-handling applications that can be dust proof, clean room, or IP65/67. The company's extensive product line starts with a Cartesian solution available in thousands of combinations from single actuators to four-axis solutions; six-axis solutions that can include precise vision-control; and a complete range of SCARAs from low cost to the industry-leading SCARA with 1200-mm reach that can carry up to 20 kgs. TM Robotics sells and services robots throughout Europe, the Middle East, India, Russia, and Africa, as well as North, Central, and South America, from headquarters in Hertfordshire, England and Elk Grove Village, IL, USA. For more information, visit www.tmrobotics.com or follow us on Twitter, LinkedIn and YouTube.
Other Articles
Giving lens cleaning cloths a robotic hand - Robotic automation for textile processing
Investing in the UK’s injection moulding sector - The case for all-electric machines and robotic integration
Robotic solutions for pharmaceutical packaging - Automated system addresses key limitations of manual processes
More about TM Robotics (Americas) Inc
Comments (0)
This post does not have any comments. Be the first to leave a comment below.
Featured Product
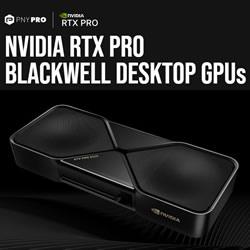