Machine vision is used in a variety of industrial processes, such as material inspection, object recognition, pattern recognition, electronic component analysis, along with the recognition of signatures, optical characters, and currency.
What is Machine Vision?
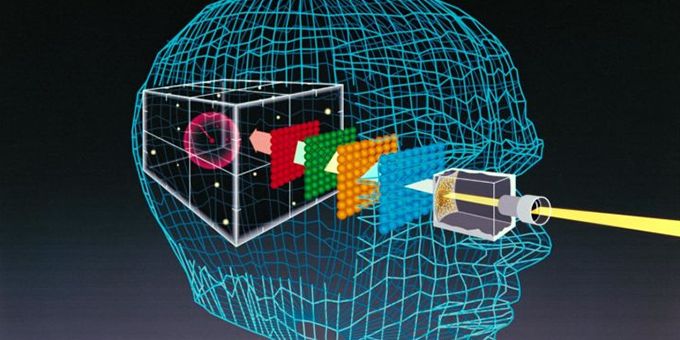
Len Calderone
Machine vision is the capability of a computer to perceive the environment. One or more video cameras are used with analog-to-digital conversion and digital signal processing. The image data is sent to a computer or robot controller.
Human eyes are responsive to electromagnetic wavelengths from 390 to 770 nanometers, while video cameras can sense a range of wavelengths much wider than this with some machine vision systems functioning at infrared, ultraviolet, or X-ray wavelengths.
Machine vision is usually linked with a computer's ability to see. The term, computer vision, is used to designate the technology in which a computer digitizes an image, processes the data, and takes some type of action.
A machine vision system uses a sensor in the robot for viewing and recognizing an object with the help of a computer. Machine vision is used in a variety of industrial processes, such as material inspection, object recognition, pattern recognition, electronic component analysis, along with the recognition of signatures, optical characters, and currency.
Besides material inspection, machine vision systems have several other applications. Systems that are used for visual stock control and management, such as barcode reading and counting, often use machine vision systems. Industrial product runs use machine vision systems to evaluate the products at various stages in the process. Even the food and beverage manufacturers apply machine vision systems to monitor quality. In the medical field, machine vision systems are used in medical imaging and examination procedures.
Machine Vision System (Wikimedia)
A robot’s vision system consists of a number of essential components, which include the camera that captures a picture, to the processing mechanism that provides and communicates the result. For any machine vision system to work dependably and produce results that can be repeated, it is important how these essential components interact.
Lighting is very important to machine vision as it illuminates the part to be viewed so that its features stand out allowing the camera to see clearly. The lens captures the image and communicates it to the sensor in the form of light. The sensor in a machine vision camera translates this light into a digital image, which is then relayed to the processor for analysis.
Vision processing employs algorithms that review the image and extricate the required information, run the required inspection, and make a decision. Finally, communication is accomplished by either a discrete I/O signal or data transmitted over a serial connection to a device that is logging or using the information.
RobotWorx - 3D Vision
A robot’s vision system is sorted into three main categories based on the color of the objects. These are (1) binary image, which consists of black and white images; (2) gray images; (3) images based on the colors of red, green or blue. An electronic image is established using pixels classified into these three categories. If an image does not fall into any of these categories, then the category that is closest to the image is selected.
Editors Recommendation "Artificial Intelligence Drives Advances in Collaborative Mobile Robots"
Sensitivity and resolution are significant specifications in any vision system. Sensitivity is the adeptness of a machine to see in low light conditions, or discover imperceptible impulses at invisible wavelengths. Resolution allows a machine to distinguish between objects. Sensitivity and resolution are codependent. Increasing the sensitivity decreases the resolution, and increasing the resolution deceases the sensitivity, if all other factors remaining constant.
The development of industrial robots has radically enhanced production efficiency. While employees still change jigs or settings according to a plan, calibrate the system, and perform tests and modifications before starting production, vision guided robots have been getting attention as a way to abolish this time-consuming work.
Most of the industrial robot manufacturers have built-in their own control programs. If you are looking for a robot, be sure that your image processing system is compatible with the control program of the robot. Even with a compatible system, setting up may require a lot of time and labor. The rationale of introducing a vision-guided robot is to improve production efficiency or reduce costs. So, if the system setup requires extra time and labor, the configuration is another aspect to contemplate.
Without a vision guidance system, robots would be blind, and unable to properly handle objects. There are vision guided robots that can be setup with minimal labor. They have predefined settings such as pick, place, and grip correction. You can achieve the setup by following the instructions of the camera setting for resolution and sensitivity, then selecting which robot will be connected, the calibration, search setting, and corrective action that needs to take place.
An operator needs to identify the coordinates manually using teaching assistance for today’s conventional industrial robots. The machines had to be readjusted every time the target or tooling was changed. The accuracy differed, subject to the operator. Vision guided robots that have auto-calibration can accomplish the calibration at the press of a button, without manual control.
There are systems that can achieve the needed accuracy, using a search tool that can isolate targets at high speed with superior accuracy, even in complex conditions. They are sturdy through misalignment correction, overlapping elimination, and distortion correction. Image enhanced filters that have shading correction and noise isolation allow for precise detection and isolation. They support diverse processes, which include appearance and dimension inspection, as well as OCR based character identification.
“Pick and place” is a conventional operation for which vision guided robots are used. Manually boxing, which is done for some products, can be automated using machine vision to recognize position and orientation. Machine vision robots can also reduce the labor for picking. Machine vision is used to detect the position of targets and send the position information to the robot so that it can complete picking without using a positioning pallet. The product can simultaneously be inspected during this process.
Fanuc pick and place robot 200iD
Machine vision guidance systems can scan objects in two or three dimensions. Unless the application necessitates three-dimensional vision guidance, two-dimensional systems work well. Purchase the simplest machine vision guidance system that meets the demands of the application.
As machine vision systems become more powerful and compact, they will routinely include tracking and traceability functions, such as the pharmacy applications, where each pill and bottle is tracked through the manufacturing process.
The machine vision market is primed for long-term growth. New non-industrial applications are growing, and with the ease of use, machine vision has an exciting future.
For additional information:
If you like this article you may like "Smart Gripper for Small Collaborative Robots"
The content & opinions in this article are the author’s and do not necessarily represent the views of RoboticsTomorrow
Comments (0)
This post does not have any comments. Be the first to leave a comment below.
Featured Product
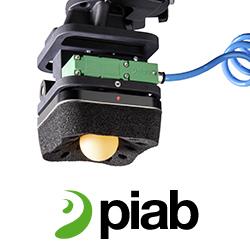