How can industrial robots gain new abilities that can increase their operational value while remaining safe and secure in a factory collaborating with humans?
COMPUTER VISION AND ROBOTICS EXPAND INDUSTRIAL CAPABILITIES
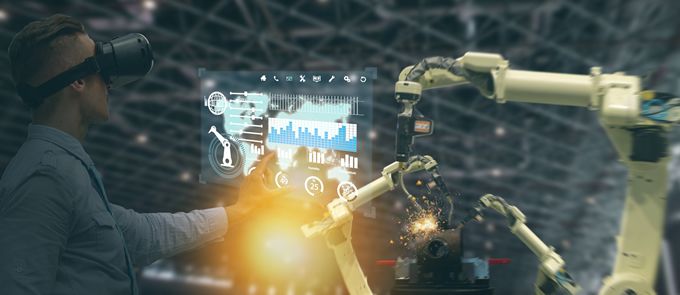
Case Study from | Wind River
Cobots, or collaborative robots, are a new step in industrial robot technology. Unlike most robots, which act as replacements for human workers, cobots are designed to collaboratively work side-by-side with their human counterparts. How can industrial robots gain new abilities that can increase their operational value while remaining safe and secure in a factory collaborating with humans? One way to increase robotic abilities in a safe and efficient manner is to use an innovative new technology: computer vision.
Computer vision technology enables a robot to use a camera or scanner to transform multidimensional inputs into data it can process, “perceiving” its surroundings and mimicking sight. Computer vision coupled with machine learning and/or artificial intelligence gives the robot or cobot increased technical abilities and the opportunity to perform more complex tasks. This data can be communicated rapidly via 5G technology to speed data to enable fast actions to enable safe interactions and reactions to the surroundings and humans working close by.
To learn how computer vision is allowing “cobots” to work securely, safely and innovatively with human workers, read this Wind River use case, “Computer Vision and Robotics Expand Industrial Capabilities”.
The content & opinions in this article are the author’s and do not necessarily represent the views of RoboticsTomorrow
Comments (0)
This post does not have any comments. Be the first to leave a comment below.
Featured Product
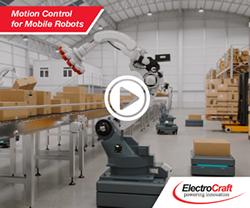