This is our first time at MODEX, so we’re excited to see the latest innovations created for the supply chain to advance automation and overall improve logistics for these companies. Booth #9435
MODEX Q&A with | Mobile Industrial Robots (MiR)
Tell us about your company.
Mobile Industrial Robots (MiR) is a leading manufacturer of collaborative, autonomous mobile robots (AMR). We develop user-friendly, flexible and safe robots to help companies automate and optimize their internal logistics and 3PL applications, and increase the efficiency of their supply chain operations. Our AMRs offer a rapid return on investment, often with a payback period of less than a year.
As a first mover in the field, we have enjoyed rapid, worldwide adoption by global leaders such as Toyota, Ford Motors, Raytheon, ABB and CABKA North America. We have branch offices in Odense (HQ), Frankfurt, Barcelona, Shanghai, Singapore, San Diego and New York, and an extensive global distribution network in 50 countries.
Your company will be exhibiting at MODEX; What is it that makes this an important event for your company?
The autonomous mobile robot industry is still relatively new, so manufacturing and warehouse companies along the supply chain are only beginning to understand the myriad ways in which these robots can benefit their organizations. MODEX is an ideal opportunity for us to meet decision makers in both manufacturing and the supply chain, helping to boost awareness of how AMRs are already automating their material transport, optimizing internal and 3PL logistics, and gaining a competitive advantage, and how MiR’s advanced AMRs specifically stand out as the industry’s safest, most efficient and easiest to deploy mobile robots on the market today. The supply chain specifically is a huge potential market for us and are excited to gather new leads at MODEX this year and beyond.
What makes your booth a must visit for MODEX Attendees?
At MODEX, attendees will see our entire family of user-friendly, powerful and robust AMRs for heavy and light transport that optimize logistics throughout the entire production chain, from the warehouse to the delivery of goods. We’ll share our MiR100 and MiR200—able to carry 100kg (220 lbs) and 200kg (440lbs)—as well as our newest robots designed to automate the transportation of pallets and heavy loads, the MiR500 and MiR1000. These latest additions are collaborative, safe and flexible alternatives to potentially dangerous and expensive fork lifts on the factory floor as well as inflexible conveyor belts and traditional automated guided vehicles (AGVs).
Our team will demonstrate how our AMRs can find their destinations on their own and always take the most efficient route to pick up, transport and deliver pallets autonomously.
MiR will also be highlighting the features that make our AMRs the safest available, with AI capabilities built in, as well as a wide range of top modules that can be customized for different applications, including a conveyor band on the MiR1000, pallet lifts and a delivery station to connect with production lines.
When you get a chance to walk the exhibit hall floor yourself, what is it you will be most interested to see? Any educational sessions, pavilions etc. you plan on attending?
This is our first time at MODEX, so we’re excited to see the latest innovations created for the supply chain to advance automation and overall improve logistics for these companies.
The Supply Chain is undertaking rapid advancements, be it automation, mobile robotics, IIoT or autonomous vehicles, give us an idea on how your company and product is being utilized now in the supply chain.
As the supply chain continues to expand and advances, finding workers who are willing or available to take on a job in logistics, especially ones that might be considered “dull, dirty and dangerous,” can be extremely difficult. Our autonomous mobile robots are solving these issue at facilities worldwide, including at Toyota, Ford Motors, Raytheon and ICM in Denmark (see brief case study here and below). These intuitive, safe and sophisticated AMRs are taking on risk-prone and repetitive tasks, reducing the likelihood of workplace injuries or job dissatisfaction. This creates a safer environment while allowing skilled staff to swap the time spent on less interesting and rewarding tasks, for complex, more appealing ones. This combination helps create a more appealing workplace aiding the recruitment and retention of the necessary workforce. As this article highlights, the AMRs are also optimizing workflow in the internal and highly pressured 3PL industry, using sophisticated programming technology, scanners and cameras to make optimal decisions at all times. In fact, the AMRs remove human error and the need for as many inventory checks, meaning logistics providers are seeing shorter and more responsive workflows with reduced bottle necks. The collaborative nature of the mobile robot also means that it safely work alongside human counterparts, responsibly optimizing productivity.
We’ve also seen that as the need for increased supply chain flexibility and efficiency intensifies, the adoption of AMRs has accelerated. In fact, the latest industry statistics show that by 2021, 58% of logistics providers will use AMR. By 2024, this number is expected to hit 100%.
ICM, one of Scandinavia’s leading suppliers of personal protective and technical equipment and work environment solutions, has actually saved 40 workhours a week with the three MiR1000 AMRs it purchased to take on internal transportation tasks. About 31,000 pallets arrive at its logistics center in Odense, Denmark, every year. They are then processed into about 100,000 orders to send out, most of these next day delivery. ICM needed a way to make the most of their limited space, a way that workers embraced and that also limited downtime in order to optimize output. The three MiR1000 AMRs freed up experienced logistics personnel in the warehouse, so they could focus on solving complex, value-adding tasks. ICM mostly handles pallets of 700-800 kg, so the high payload of MiR1000 (1000 kg) was just what the company needed. The AMRs used sophisticated technology to work harmoniously with workers, trucks and stackers, allowing for a very modern workforce.
The 40 hours saved each week is time that the staff previously spent on moving goods between the receiving area and the positioning areas. Not only does this allow the workers to take on more preferable tasks, the ICM staff responded positively to the MiR AMRs, recognizing an improvement in their working environments.
Give us your thoughts on what the future holds for manufacturers and the supply chain.
Autonomous mobile robots equipped with advanced artificial intelligence (AI) capabilities and adhering to industry safety standards will increasingly be used in even more facilities across the supply chain to optimize logistics, save time and money, and respond more effectively to ever-changing customer demands. AMRs provide significant business value by facilitating a lean, optimized supply chain. In fact, the vast majority of industry leaders we spoke to for a recent report on barriers and challenges surrounding automation in modern manufacturing said they expect AMR to have a positive impact on the future of their industry. In fact, 78% are thinking about implementing AMR in the next two years, with even more considering it as they learn more about the tremendous benefits they offer in increasing efficiency across their logistics with a fast ROI and improved workforce competencies.
If you would like please provide contact information for a reader to setup a booth demo.
To setup an appointment for a booth demo or visit please contact Ed Mullen, VP of sales, Americas, at emu@mir-mobile.com or call +1 (631) 675-1838.
The content & opinions in this article are the author’s and do not necessarily represent the views of RoboticsTomorrow
Comments (0)
This post does not have any comments. Be the first to leave a comment below.
Featured Product
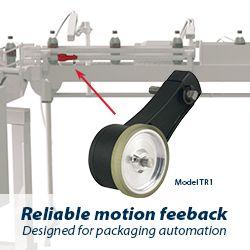