Always more, always faster, always further everything needs to arrive at the right time at the right place – the global goods cycle keeps the economy running and is a challenge for everyone involved.
Without Micromotors Global Logistics Would Be Lost
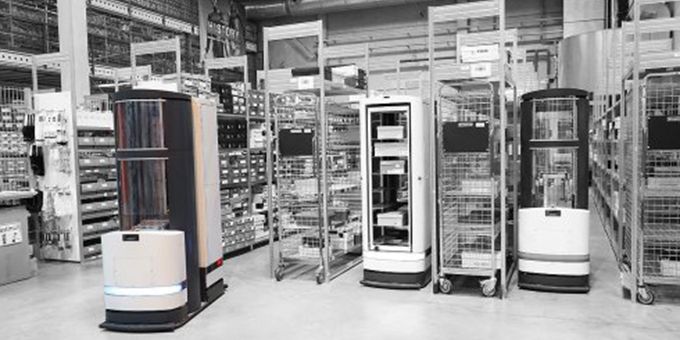
Article from | FAULHABER MICROMO
Despite sounding similar and being closely related, the term “logistics” does not originate from the same ancient Greek root word as “logic”, but rather from French military jargon. Since the end of the Middle Ages, the “maréchal de logis” – the quartermaster – was responsible for providing marching and fighting troops with somewhere to sleep and rest. The quartermaster’s range of tasks grew with time and began to extend to many other parts of the overall supply chain. So what started out as simply providing “logis”, i.e. accommodation, became extremely complex military logistics.
The quartermasters originally belonged to the cavalry because the transmission of information has always been key to logistics. Until the 19th century, horses were used to relay information as fast as possible. Nowadays, electromagnetic waves that are propagated through the ether and along cables perform this task somewhat more quickly. Today, the largest data volumes are transmitted using fibre optic cables. They form the backbone of the global logistics network: The cables pass on the necessary information by means of light signals – from the online order, through shared just-in-time production in smart factories to express doorstep delivery.
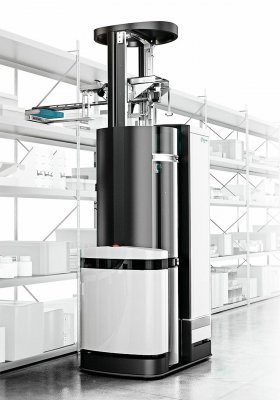
Toru Robot
Connections with nanometre precision
Two fibre optic cables must be joined together fibre for fibre. This is extremely delicate work because each individual optical fibre is as thin as a human hair. The optical core is even thinner and has a diameter of just five microns.
When two such optical fibres are joined together, the two ends must line up precisely with each other so that the signal can then later be transmitted cleanly without impairment. On construction sites, the precise alignment is carried out by small mobile machines. The individual fibre ends are first cut to length with an exact 90 degree cut, the protective insulation is stripped away and the fibres are then placed in the device. The device automatically and accurately aligns the two pieces with each other in three dimensions so that the flat ends meet precisely. They are welded together and then insulated again. Connection of the fibres and unimpeded flow of the signals are now guaranteed. The nanometre-precise alignment is performed by means of positioning drives from FAULHABER, e.g. with DC-micromotors of the 1524…SR series, with gearhead and lead screw as well as a high-resolution encoder. Drives that work with high-precision stepper motors are also used here.
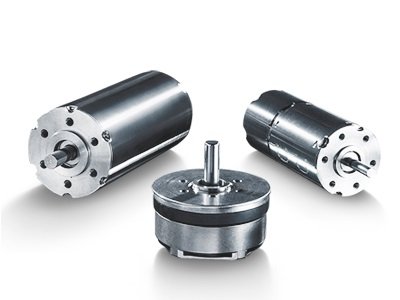
BXT Motors
High degree of automation in warehouse systems
Thanks to this technology, the fibre optics can transmit the signals for a digital order over long distances without errors and at the speed of light. Orders can be sent by an end customer to an online shop, but just as easily by a production plant to a supplier. In both cases, a whole series of processes are set in motion. Ultimately, these processes result in products being retrieved from a storage facility and made ready for shipping.
Today, an increasing number of work steps involved in storing items in warehouses as well as retrieving these items and preparing them for dispatch are being taken over by automatic storage and retrieval machines, driverless transport systems and intelligent logistics robots. The computer-controlled machines receive a work order and then move automatically to the target rack space in order to deposit or collect an item there. To enable this, they are – depending on the type of rack system – equipped with lifting columns, telescopic arms or grippers which grip and move the packages or trays.
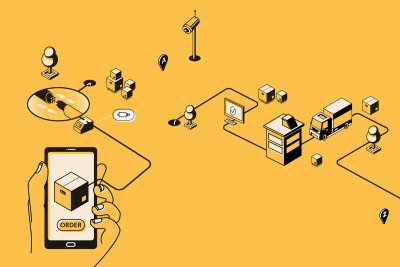
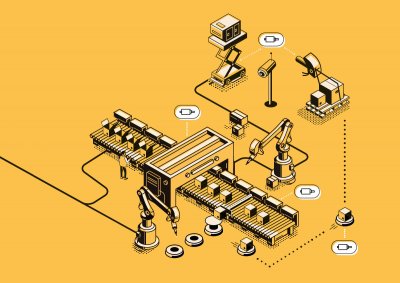
Logistics Robots
On board these automatic devices, there normally is not much space for the motors that are needed to drive them. The motors are frequently installed directly in the handling elements. There, despite their delicate proportions, the motors often have to lift considerable weights. Speed also plays a role: In the huge storage facilities of e-commerce companies, many thousands of orders are processed every day. Therefore, the individual steps must be performed rapidly.
Precision, power and speed
A typical unit comprising a lifting column and gripper used on a robot contains a drive unit consisting of brushless DC-servomotors of the BX4 series with Motion Controller and planetary gearhead from FAULHABER. When used in the lifting column, for example, this combination ensures precise positioning, exact retrieval and reliable processes during continuous operation with constant load changes. The automated processes are monitored to some extend by camera systems. FAULHABER motors are again frequently used to drive high-quality, moving cameras.
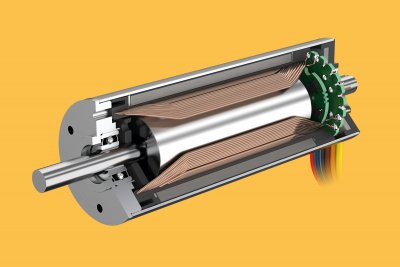
BX4 Motor
After retrieval, the item is usually deposited on a conveyor belt or roller conveyor. These generally have track switches, paddles or pushers to separate individual packages or elements and to move them onto the desired processing path. In large warehouses in which thousands of packages per hour are transported on such conveyor systems, the speed of the automatic sorting systems is a key factor. The track switches must be moved to exactly the right position in a fraction of a second. DC-micromotors of the 2237…CXR and 2342…CR series in combination with a gearhead are frequently used for this task.

CXR Motor
Transport tasks are also often performed by automated guided vehicles (AGV). These vehicles are equipped with mounted modules for handling their cargo: Moving levers, clamps and pins ensure that the items are fixed securely while they are being transported. The moving elements each are equipped with a drive.
Economical packaging
The items are transported to the packing station where they are put into a shipping box. In modern systems, however, “where they are packed in a made-to-measure shipping box” would be more accurate because automated packing stations use sensors to detect the dimensions of the item to be shipped and fold an appropriately sized box from a cardboard sheet. This not only saves material, but also shipping costs because the logistics service providers set their prices according to volume as well as weight. The actual folding work is performed by small levers and paddles in the packaging machine. Servo drives with integrated Motion Controller from FAULHABER are optimally suited for moving these elements.
If packages are stacked on pallets for shipment, they need to be fixed securely in place. Straps made of fibre-reinforced plastic are usually used for this. They are attached using so-called strapping tools. These tools tension and weld the strap so that it is tight against the stack and holds it securely. Individual packages can also be additionally stabilised in this way. As the tools are handheld, weight is a particularly important factor – every gramme saved helps protect the health of employees. For this reason, the motors used for tensioning need to be as small as possible, e.g. the 3274 …BP4 brushless DC-servomotor. It weighs just 320 grammes, but can achieve a peak torque of over 1 Nm, which ensures that even heavy loads are secured safely.
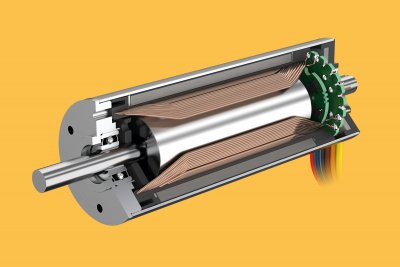
BP4 Motor
“Our motors are used in virtually every area of the logistics chain,” says Rolf Schmideder, Business Development Manager at FAULHABER. “Our drives and the typical requirements – maximum power, speed and precision with minimum volume and weight – are simply the perfect match. And the range of possible applications will be even greater if in future drones and robots are also used for delivering individual items.”
The content & opinions in this article are the author’s and do not necessarily represent the views of RoboticsTomorrow
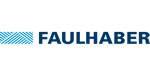
FAULHABER MICROMO
Since 1961, FAULHABER MICROMO has partnered with OEMs to deliver high precision, high performance, custom micro motion system solutions to markets such as medical, robotics and automation in North America. FAULHABER MICROMO's tradition of innovation started decades ago in Germany. The groundbreaking invention of the FAULHABER coreless winding started it all for a market that produces millions of motors today. How can the FAULHABER MICROMO team help you deliver your next innovation to market first? Learn more about MICROMO's solutions for the most demanding applications, our diverse motion products and technologies, online ordering, Engineering and R&D teams, Clean Room Assembly, Machining Center and other services at our Clearwater, FL facility at https://www.faulhaber.com.
Other Articles
Walking naturally with artificial foot
Testing drive systems virtually - Simulink library for development and digital twin.
At least 60 million strokes
More about FAULHABER MICROMO
Comments (0)
This post does not have any comments. Be the first to leave a comment below.
Featured Product
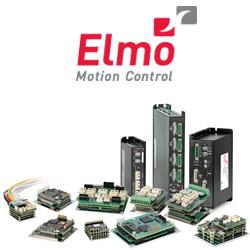