Sheet-Jamming Technology Revolutionizes Soft Robotics Grippers
Designing robots that can handle delicate objects without damaging them has been a challenge for a long time. Suction cups have been the go-to option for industries such as packaging and automobile, but their weight-lifting capability is limited. To improve the performance of suction grippers, a new concept called sheet-jamming phenomena has been introduced in soft suction grippers. This technology has been used to create a suction gripper that is lightweight and can lift almost twice the weight of regular suction cups.
Researchers at the National University of Singapore (NUS), namely Abhishek Bamotra, Pushpinder Walia, Avataram Venkatavaradan Prituja, and Hongliang Ren have developed a novel suction end-effector. The suction gripper is designed to mimic the traditional suction cups' bell-shaped design to create an enclosure with the non-porous surface of an object, creating a pressure difference and initiating negative pressure. All while doubling the lifting capabilities of any traditional suction cup while operating at just -60 kPa.
The gripper is made of multiple sheets of flexible material that experience sliding action when bent, which increases sliding friction when under pressure and increases the stiffness of the stack. The resistive tensile force required to slide layers against each other in one dimension can be calculated using the formula F = μnPWL, where μ is the frictional coefficient, P is pressure, W and L are the width and length of layers, and n is the number of layers.
The design of the suction gripper considers the selection of material, surface area, thickness, and the number of layers of the sheets used to control the stiffness and weight lifting capability. The suction gripper is circular in shape, maximizing attraction force with the object. The fabrication process involves designing and 3D printing molds, fabricating the flexible structure, patterning the sheets, and casting liquid silicone. The molds are designed with various features to ensure effective weight-lifting capability and leak-proof contact between the suction gripper and the object. The flexible tripod-like structure separates the base and top layers of the suction gripper. The suction gripper's support mounts are 3D printed to enhance the manual lifting grip.
The suction gripper's weight-lifting and force capabilities were tested through experiments using objects with weights ranging from 500 g to 5 kg. Interestingly, the suction gripper was able to lift objects 200 times its own weight for flat objects and 154 times its own weight for curved objects. In kilograms, the suction end-effector was able to lift flat objects weighing 5kg and curved objects weighing 4kg with ease. The suction gripper's ability to lift objects and withstand force makes it useful for applications in various industries, such as manufacturing and logistics.
In addition to its applications in manufacturing and logistics, the suction gripper's ability to handle delicate objects has also led to its use in the biomedical field. The research team has successfully tested the suction cup on a human cadaver for invasive surgeries, demonstrating its potential for surgical applications. The use of the suction gripper in surgical procedures could minimize tissue damage and reduce the risk of complications during surgeries, claims the team. This further highlights the significance of sheet-jamming technology in creating versatile and efficient soft robots that can benefit various industries.
The suction gripper is an example of a new generation of soft robotics that uses sheet-jamming phenomena to produce superior suction capabilities. The technology has a wide range of applications, including packaging, automobile, and biomedical fields. Its lightweight and flexible design allows for easy handling of delicate objects, making it an ideal choice for handling delicate and fragile objects. The research results show that the suction gripper can be used for tasks that require the handling of objects with varying weights and sizes. The diameter of the suction gripper can be modified according to the application to grip and lift objects with smaller diameters and sizes better.
Researchers have also published about the first version of their suction gripper. It is interesting to see the enhancements in the gripper and it’s lifting capabilities.
Conclusion
With the increasing need for robotic automation in various industries, the demand for suction grippers has been rising. However, the limitations of traditional suction cups, such as their weight-lifting capabilities and the potential for damaging delicate objects, have created a need for soft suction grippers. According to market forecasts, the demand for soft suction grippers is expected to increase across various industries in the next 5 years. [Yahoo news]
The introduction of sheet-jamming phenomena in suction grippers has revolutionized the robotics industry. The technology has enabled the development of lightweight and flexible suction grippers that can lift almost twice the weight of regular suction cups. The rise in demand for these grippers is a testament to the potential they hold in enhancing the efficiency and effectiveness of various industrial processes. The future of soft robotics looks promising with the integration of sheet-jamming phenomena in grippers, and the possibilities seem endless.
DOI: https://doi.org/10.1115/1.4042630
Previous version: https://doi.org/10.1109/ICARM.2018.8610688
Comments (0)
This post does not have any comments. Be the first to leave a comment below.
Featured Product
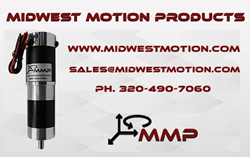