Elmo to Display Full Motion Solution at Major U.S. Trade Shows
Automation Industry Association Criticizes 60 Minutes Segment 'March of the Machines'
Roboteq Launches Revolutionary Sensor for Guiding Robotic Vehicles along Invisible Magnetic Tracks
Neato Robotics Ramps Up for Accelerated Growth in 2013 With Appointment of Consumer Electronics Veteran Larry Wuerz
Lucintel Report Indicates Increasing Security Threats and Border Control to Drive the UAV Industry Globally
HDT Global Announces New Leadership at HDT Expeditionary Systems Group
United States Army Awards AeroVironment, Four Other Companies Small Unmanned Aircraft Systems Contract Worth Up To $248 Million
Wynright Automates Receiving with New Robotic Truck UNloader
Stäubli Completes Offline Development Offering with Visual Components Simulation
Lincoln Electric Introduces 2013 Equipment Catalog
KAIROS AUTONOMI COMPLETES THE FIRST PHASE OF DELIVERIES FOR NATIONAL GUARD BUREAU MOVING GROUND TARGET CONTRACT
Intelligrated celebrates grand opening of headquarters expansion in Mason, Ohio
Vanderlande Industries' Makes Debut at ProMat 2013
Inventor Dean Kamen Announces New Season Robotics Game at the 2013 FIRST® Robotics Competition Kickoff
FIRST® ULTIMATE ASCENTSM 2013 Robotics Game Revealed
Records 10636 to 10650 of 12237
First | Previous | Next | Last
Industrial Robotics - Featured Product
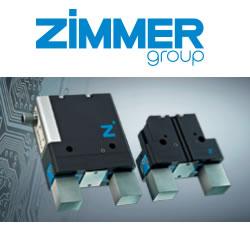