Plug-and-play cobots offer a perfect transition from manual handling or assembly to more automated operations. But, it is important to choose one with a powerful and safe grip!
Choose Your Cobot Vacuum Gripper Wisely
Josef Karbass | Piab
Thinking about investing in a helping hand in the form of a cobot? Plug-and-play cobots offer a perfect transition from manual handling or assembly to more automated operations. But, it is important to choose one with a powerful and safe grip!
Collaborative robots or cobots are robots that have been designed to work alongside humans. Equipped with grippers, sensors and vision technology, this latest robotics technology is safe and easy to use in almost any setting. Little wonder that they are quickly becoming a familiar sight in industry
Cobot equipped with Piab’s piCOBOT®—
a plug-and-play compressed air driven vacuum ejector unit
Plug-and-play models specifically targeted at small workshops or businesses, where so far work has been carried out manually, are being promoted by several different manufacturers. However, depending on their design, the capacity and capability of these different cobots and end-effectors can vary significantly. In fact, some vacuum end-effector grippers have ten times the lifting capacity of others.
The secret behind a successful cobot vacuum gripper is its vacuum flow. Without a powerful and continuous vacuum flow, the cobot vacuum end-effector will fail to grip and securely lift whatever it is you want it to handle. Having a cobot with an insufficient lifting capacity will be both frustrating and unsafe. A “weak” cobot will drop and damage parts, compromising the working environment and increasing the risk of industrial accidents.
This is why it is important to look at how the vacuum is generated in the cobot and gripper unit you are about to choose. However, let’s start from the beginning:
The vacuum does the work
Often thought of as a completely empty space, vacuum is an ideal and elusive state. For practical reasons engineers will instead usually view vacuum as negative pressure, as this describes the force that can be harnessed to do work.
In a vacuum system, it is the difference between the atmospheric pressure (equal to the weight of the air above your head) and the vacuum (negative) pressure that provides the ability to perform actions such as lifting, holding, moving, and so on.
Different cobots use different vacuum pumps
In engineering, vacuum is usually created using a vacuum pump, and although there are several different types of vacuum pumps, two main types are used in cobot vacuum end-effectors – miniature electro mechanical pumps and compressed air driven pumps/ejectors.
Vacuum pumps are rated according to their ability to generate vacuum flow. The vacuum flow is the induced air drawn into the pump’s body from atmospheric pressure. This figure is usually expressed as normal litres per minute (Nl/min) or cubic feet per minute (cfm).
Miniature electro mechanical pumps provide less flow
Some of the plug-and-play cobot vacuum grippers offered on the market today use miniature electro mechanical vacuum pumps. This might be the only alternative in settings without access to compressed air. Or, if the cobot is intended for use on a highly mobile truck.
However, miniature electro mechanical vacuum pumps provide significantly less vacuum flow compared to compressed air driven vacuum pumps.
Better lifting capacity with compressed air
As the lifting capacity depends on the vacuum flow, cobots fitted with compressed air driven vacuum pumps will provide between four and ten times the lifting capacity of cobots that use miniature electro mechanical pumps.
The simplest type of compressed air driven vacuum pump is known as a single stage ejector. Vacuum is generated by forcing compressed air through a small orifice or ejector nozzle at very high speed, resulting in negative pressure building up inside the system. From the outside of the system, atmospheric pressure attempts to balance this negative pressure and reinstate equilibrium. This creates the vacuum flow or induced air flow.
Multistage ejectors are even better
In so called multistage ejector pumps, compressed air enters the pump and is fed through a system of ejector nozzles and chambers of varying sizes that act as a “pressure amplifier”. Multistage vacuum ejectors make optimum use of the energy stored in the compressed air through specially designed air nozzles in a series of progressively larger ejectors that allow the compressed air flow to expand in controlled stages.
Multistage ejector principle.
Multistage ejector vacuum pumps offer many benefits over both single stage ejectors and mechanical or electro mechanical vacuum pumps. They are quiet, have few moving parts, and generate no heat or vibration, resulting in virtually maintenance-free operation.
A wise choice
Plug-and-play cobot vacuum grippers that use multistage vacuum ejectors offer the ultimate vacuum flow, which translates into the best lifting capacity and the ability to handle a large variety of products, including objects difficult to grip, such as flexible packages. This is why choosing a compressed air driven “strong” cobot vacuum end-effector is a wise choice for anyone investing in the latest of co-working tools.
About Piab
Piab provides smart solutions for the automated world, helping thousands of end users and machine producers in e-commerce logistics, food, pharma, automotive and other manufacturing industries to improve energy-efficiency, productivity and working environments. With 430 employees and SEK 1 bn in sales 2017, Piab is a global organization, serving customers in almost 70 countries from a network of subsidiaries and distributors. By leveraging the ongoing technological development in automation and robotics, and targeting high-growth segments and geographies, Piab's vision is to become the global leader in gripping and moving solutions.
The content & opinions in this article are the author’s and do not necessarily represent the views of RoboticsTomorrow
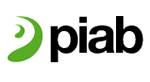
Piab Inc.
Piab provides smart solutions for the automated world, helping thousands of end users and machine producers in e-commerce logistics, food, pharma, automotive and other manufacturing industries to improve energy-efficiency, productivity and working environments. By leveraging the ongoing technological development in automation and robotics, and targeting high-growth segments and geographies, Piab's vision is to become the global leader in gripping and moving solutions.
Other Articles
ProMat Q&A with Piab
Reinventing Intralogistics
The dm Drugstore Distribution Center Relies on Piab Suction Cups
More about Piab Inc.
Comments (0)
This post does not have any comments. Be the first to leave a comment below.
Featured Product
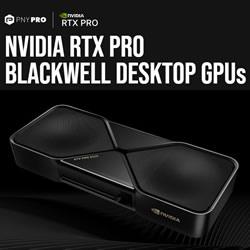