Given the proliferation of warehouses, distribution centers, direct to consumer (D2C) business models, fleets of AMRs, questioning the validity of innovation is worthy of examination.
AMR Innovation Arrives at MODEX 2020
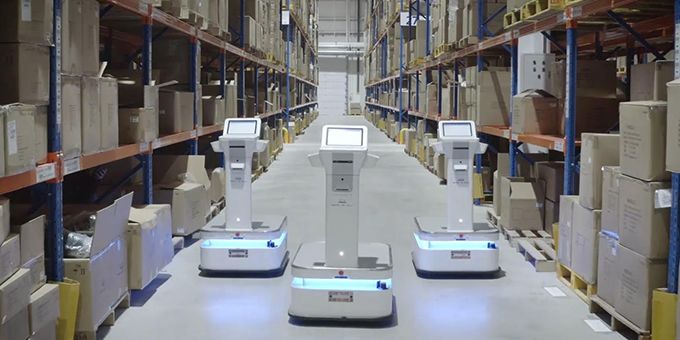
Nic Temple, VP of Sales for the Americas | ForwardX Robotics
With MODEX 2020 just next month, (March 9 - 12 in Atlanta) first time attendees, repeat attendees, and members of the media are asking the question: What’s new in the material handling arena? Both new and long-time exhibitors proclaim a new product innovation; rarely has the new product been thoroughly field tested or old products are merely a repackaged version of what was introduced at ProMat in Chicago last year.
Given the proliferation of warehouses, distribution centers, direct to consumer (D2C) business models, fleets of AMRs (Autonomous Mobile Robots), questioning the validity of innovation is worthy of examination. Unlike in prior years when attendees would walk the show floor for days, many are using the MHI MODEX app and visiting for just a single day. For that reason, a compelling innovation from ForwardX (Booth 1207) should be the first stop for serious AMR decision-makers.
Innovation differences with MODEX 2020 AMRs
While there will be many AMRs on display at MODEX 2020, only ForwardX provides a Visual Autonomous Mobile Robot. Rather than relying on LiDAR SLAM (Simultaneous Localization And Mapping) like most competitors on the market, ForwardX’s robots depend on a sensor fusion solution with Global Award-winning Computer Vision (CV) being the primary source for localization and obstacle avoidance with LiDAR, Encoder, and IMU data as secondary feedback to the control loop. LiDAR is 2D, so 3D CV technology offers a richer source of data, and a more robust solution far better-suited to ever-changing warehouse, distribution center, and cellular manufacturing environments.
© 2020 ForwardX
Integration with WMS, MES, and ERP via Robot Computing Systems
Another innovation element that will be on display at MODEX 2020 will be ForwardX’s Edge/Cloud based architecture. At the edge, Robot Computing System (RCS) includes the multi-sensor fusion, computer vision based deep learning, local path planning ability based on V-SLAM and reinforcement learning. In the cloud resides the Robotic Process Manager (RPM). The RPM includes a multi-agent cluster scheduling system. It receives tasks from operators, such as Warehouse Management Systems (WMS), Manufacturing Execution Systems (MES) and ERP (Enterprise Resource Planning).
The robots holistically assign global tasks and intelligent paths for the robots, greatly increasing efficiency, improving throughput and reducing downtime.
© 2020 ForwardX
The AI innovation critical for fleets of AMRs
For smaller operations with one or two AMRs, perhaps Artificial Intelligence (AI) could be less important. When there are 10 to 100 AMRs navigating a large material handling operation AI is not an option.
ForwardX robots depend on V-SLAM with Deep Learning techniques for positioning and navigation. This allows the robot to adapt more readily to changing environments that LiDAR-only based robots cannot handle. The ability to “learn on the fly” allows the big data gathered to predict velocity and direction of obstacles using Deep-Q-Learning and Asynchronous Advantage Actor-Critic techniques. This creates a more intuitive nature in these robots which drives a more collaborative and efficient local path planning.
Furthermore, by analyzing the paths that are typically taken in a facility the neural network becomes more intelligent. This means the robots will start to predict what the next delivery solution might look like and therefore be better prepared to accommodate peaks and troughs of delivery requirements. For the user, this simply means a more efficient delivery system with a lower cost per delivery or more deliveries made per hour.
Applicability
Visual AMRs with Deep Learning improve pick time and double UPH in any goods to person or person to goods application within ecommerce, manufacturing, and order fulfillment even in a retail environment and can be installed and running in one week, performance guaranteed, as well as an average 30% cost reduction in picking costs.
The ROI calculation
ROI (return on investment) in less than two years allows for affordable large mass deployment of innovative technologies. The rapid ROI includes a full turn-key solution, supplying not only the technology, but also a team of deployment engineers and project managers to ensure rapid, effective, and efficient delivery. The innovative technology is backed by agreed upon UPH improvements needed to make an investment in a fleet of AMRs.
About Nic Temple
Nic Temple is the Vice President of Sales for the Americas at ForwardX Robotics, a vision based autonomous mobile robot (AMR) and technology company. For 15 years and counting, he develops relationships with customers to address their business’s performance improvement requirements by applying world-class cutting-edge technology. Temple helps guide them through potential pitfalls of being early-adopters to ensure that they are successful and ultimately increase their competitiveness in the market. He holds a BSME from Virginia Tech and an MBA from the Australian Graduate School of Management (AGSM).
The content & opinions in this article are the author’s and do not necessarily represent the views of RoboticsTomorrow
Comments (0)
This post does not have any comments. Be the first to leave a comment below.
Featured Product
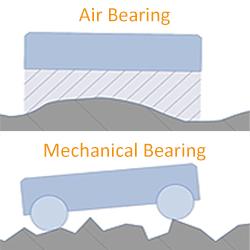