Calculating the ROI of Offline Robot Programming Software
Capital investments in advanced manufacturing environments require careful consideration, especially if that investment is for a new process or technology. If you are looking at investing in OLP here are some things to consider about the potential return on investment (ROI).
Addressing Challenges in Software Solutions for Robots and Physical AI
We leveraged our long heritage and leadership in robotics to create an AI software product that helps our customers overcome the challenges of traditional automation, accelerate set-up and deployment, and achieve greater ROI from their existing automation systems.
Robotic Software Market is Poised to Surpass USD 150 Billion by 2034
With businesses across industries striving to optimize operations, increase efficiency, and reduce costs, robotic software is becoming a crucial component of modern industrial and service applications.
NVIDIA Brings Generative AI Tools, Simulation and Perception Workflows to ROS Developer Ecosystem
Among the reveals were new generative AI nodes and workflows for ROS developers deploying to the NVIDIA Jetson platform for edge AI and robotics.
How Remote Industrial Robotic Control Makes the Most of Automation
Some facilities struggle to achieve a substantial return on investment for their automation initiatives. Remote control systems can change that by making the most of robots' significant advantages while mitigating their biggest challenges.
Have You Looked at Automating Fabrication Tasks in the Past? Why Didn't You?
We recently hosted a webinar titled: "Unlock Value-Stream Productivity with Robotic Cutting". During this webinar, we polled audience members. Our first question: Have you looked at automating fabrication tasks in the past. Most respondents said yes, they had, in fact, explored this.
Why Use Offline Robot Programming Software and How to Get Started
If you have added manufacturing robots to your facility, you are already aware of the advantages they provide and the ROI. Robots do have a downside, however, when it comes to programming-most of the time, they must be offline to be updated or programmed.
Robot Control: Using Native Programming Language or an External Controller?
In service robotics as well as in academia, flexibly designable, use-case specific controllers are used, resulting in the respective robots to mainly act as actuators with low-level control systems but without individual intelligence.
ArtiMinds and ATI Accelerate Technology Implementation with Greene Tweed
Choosing the right automation partners led Greene Tweed to quickly develop, integrate and install a more flexible automated material removal cell.
Virtual to Reality: Delivering Accuracy to The Real World
It's easy to show a robot being programmed in a matter of minutes inside of a controlled virtual environment. But those programs need to translate to something useful in the real robot cell. The points that the robot will follow need to line up with the part properly.
Robotic Plasma Cutting in a 3D World
ARC Specialties designed and built a turnkey solution for 3D robotic plasma cutting with the help of essential offline programming tools. With the right partners by your side, no challenge is too steep.
Readers Choice 2020: Using Mesh Network Applications for Robotics
Many companies make mesh network products for home Wi-Fi systems. Those are indeed valid and popular applications, but there are ample opportunities to use mesh networks for robotics, too.
Standardized Robot Programming - From Lean Entry to Complex Applications
With solutions that enable intuitive and harmonized programming of robots from a wide range of manufacturers using pre-developed programming templates, effort and costs are reduced considerably. This makes their use attractive for more and more companies.
How COVID-19 is Accelerating Robot and Drone Technology for use in Everyday Activities
The COVID-19 pandemic has forced changes to our daily lives, but when it comes to technology, not all changes have been unwelcomed. In many ways, shifting the way we live has accelerated the use of technology to a level that we were only beginning to dip our toes into.
Lights Out Robot Painting
Robots are revolutionizing the visual arts by providing artists with new creative techniques, says Albert Nubiola, CEO of RoboDK, as an exhibition of robot-made paintings opens in the prestigious Ben Brown Fine Arts gallery, London.
Records 1 to 15 of 47
Featured Product
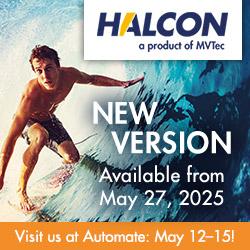
Next-Level Vision with HALCON 25.05
HALCON 25.05 sets new standards for machine vision, introducing Deep 3D Matching for robust bin picking, enhanced OCR accuracy, improved QR code reading on curved surfaces, and smarter camera integration. Meet MVTec at Automate Detroit and experience how the latest deep learning technologies and development tools empower you to create faster, more reliable, and flexible industrial solutions.