While traditional robotics systems have successfully served the food sector for many years in palletizing (and some packaging) applications, it is only in recent years that it has become possible for robots to handle delicate food items directly.
New Robotic Grippers Transforming the Food Sector
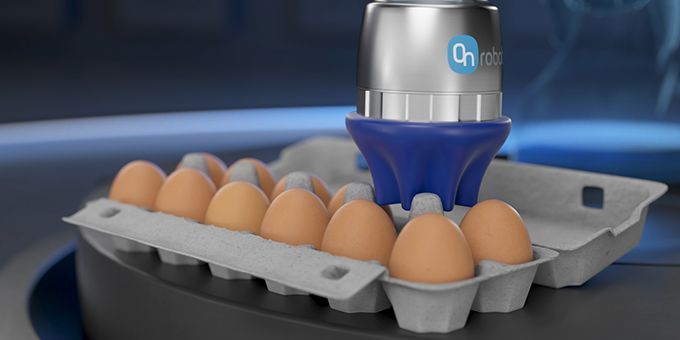
Kristian Hulgard, General Manager, Americas Division | OnRobot
The current world population is estimated to be 7.8 billion. And with the United Nations Population Division predicting that number will reach 10.9 billion by the end of the 21st century, the need for food manufacturers to embrace automation in order to keep pace with demand is urgent and growing.
Demographics is just one driver of automation adoption in the food sector, however. Worker safety, stringent food safety regulations, a rise in the popularity of processed foods and the need to improve output while reducing production costs all play a part in increased automation adoption.
Until recently, food processing was something of a final frontier for robots.
Traditional automation excels in automotive manufacturing scenarios, where metal meets metal, leather and plastic. But traditional automation struggles to cope with some of the unique demands of the food sector, where product often requires a soft touch, regularly arrives in irregular shapes and orientations and is destined for human consumption.
While traditional robotics systems have successfully served the food sector for many years in palletizing (and some packaging) applications, it is only in recent years that it has become possible for robots to handle delicate food items directly.
The arrival of new and improved gripper technology accompanied by innovative vision systems changed everything. Advancements in gripper technology that mimic human touch make it possible for robots to pack fruits and vegetables.
Meanwhile, vacuum grippers enable robots to successfully perform packaging tasks with a delicacy that's beyond the capabilities of traditional grippers. And soft grippers enable the direct handling of foods with a finesse that ensures product is not damaged or bruised during the automation process.
As a result, secondary food processing applications are now well within the abilities of automation systems. From picking and placing of soft fruits to handling fancy chocolates and bakery items, the food sector is embracing new gripper technologies at a remarkable pace.
A recent report from consultancy firm ING found that the number of food manufacturers adopting automation increased by 50% between 2014 and 2019. And The Association for Packaging and Processing Technologies predicts that the global food packaging market will grow at a CAGR of 4-5% to reach USD400 billion by 2025.
So, what are the benefits of automation in the food sector and what are the issues manufacturers need to keep in mind when selecting a gripper for food-related applications?
Worker safety and retention
With food manufacturers and workers facing challenges related to COVID-19, including new hygiene and social distancing regulations, it's a good time to consider supplementing your human workforce with automation. Robots can step in to fill those roles that are no longer safe or feasible for humans, plus robots can can operate 24/7 without tiring.
Additionally, the arrival of collaborative robots provides manufacturers with a way to tackle the long-standing issue of worker retention. Collaborative robots allow production managers to reassign workers to more interesting tasks, while the robots take over the dull and dirty jobs --from heavy lifting to repetitive pick and place operations-- that can lead to worker dissatisfaction and even injury. And they can help support social distancing requirements, ultimately leading to enhanced workplace safety and improved worker satisfaction.
Meet stringent food safety regulations
Driven by consumer and sector demand, regulatory bodies around the world enforce strict requirements on the food processing sector. Even with the best of intentions, human workers can carry and spread contaminants that end up finding their way into the final product.
With regulatory requirements in mind, it's essential that manufacturers choose certified food-grade grippers. In the United States look for FDA 21 CFR certification for non-fatty food items and within Europe make sure the gripper has EC 1935/2004 certification for food handling.
Vacuum grippers that do not require an external supply of compressed air are ideal for food packaging and palletizing. Robots can perform superbly without vision, but when trying to pick several types of objects arriving in different orientations, adding a vision camera to identify the items and guide the robot arm makes sense. Many automation engineers regard vision-guided applications with trepidation due to cost and complexity, but new user-friendly solutions for collaborative automation are now emerging. An example is OnRobot’s VG10 gripper that works seamlessly with the company’s new vision camera “Eyes”.
Certified soft grippers are recommended for processing of delicate, easily bruised items. They not only only enhance food safety, but they’re also capable of handling a wide array of irregularly-shaped and delicate foods, such as lettuce, herbs and strawberries.
Ideally, choose a gripper that doesn't require an external air supply because it will eliminate problems associated with dust and noise and reduce both complexity and cost.
Improve productivity and quality
Certified grippers can help manufacturers maintain high-quality standards –and avoid costly product recalls-- while simultaneously helping to improve productivity.
Make sure that your gripper can handle payloads that meet (and even exceed) your current application requirements –in most food processing scenarios, this means a gripper with a payload of up to 2.2kg (4.85 lb).
Look out for grippers that are easy to swap around as this will reduce downtime when switching grippers out for cleaning.
Select grippers that are dishwasher safe as this will reduce overall cleaning times. Further, look out for grippers that are compatible with a wide range of robots, as they will add to the flexibility of your investment, enabling you to use the gripper in a wide variety of applications.
There is a long-standing shortage of skilled workers in the manufacturing sector, so it's important to choose grippers that are easy to integrate with existing automation and that are easy for end-users of all skill sets to operate. In the case of grippers intended for use with collaborative robots, this means ensuring compatibility with leading collaborative robot brands.
Vacuum or Soft?
Soft grippers are well-suited to delicate food handling and packing tasks. Vacuum grippers can take on some these tasks, but they have some limitations that makes them a good fit for handling less delicate foods and for general palletizing tasks.
Most vacuum grippers require compressed air. This adds a layer of technological complexity. It also means having to clean down the extra equipment and associated tubing and wiring.
Vacuum grippers prefer working with silky smooth surfaces –a preference that excludes a lot of foodstuffs. While vacuum grippers can handle cans and food packages with ease, they will struggle with the uneven surfaces of many foods.
The nature of vacuum gripper technology means that they can leave marks on food items, resulting in an unappetizing product. Generally speaking, it's best to choose soft grippers when dealing with easily bruised items and vacuum grippers for handling hardier objects such as beverage cans and boxes of food. There are exceptions, but in general, vacuum grippers are ideal for palletizing and soft grippers ideal for food handling.
When using vacuum grippers to handle food directly, the same regulations around food safety apply. So, choose grippers that come with easy to switch and replace suction pads –and, especially in cases where they are going to be handling product directly, make sure the gripper's suction pads are food grade and easy to clean.
If the gripper is intended for use in palletizing, then make sure its payload capabilities meet your requirements. For most applications this means a gripper capable of handling payloads of up to 15 kg (35lb). Ideally, select a gripper that doesn't require an external air supply as this will reduce the overall complexity of the implementation and reduce overall maintenance costs.
Food demand is set to increase dramatically over the decades ahead. But with the right automation and gripper solutions, food processing facilities can meet that demand while satisfying food processor's hunger for greater productivity and reduced costs.
The content & opinions in this article are the author’s and do not necessarily represent the views of RoboticsTomorrow
Comments (0)
This post does not have any comments. Be the first to leave a comment below.
Featured Product
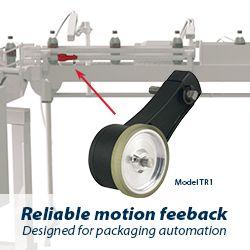