In this article, let's dive deeper into how it works and what factors you should consider if you are thinking to switch to using the Goods-to-Person fulfillment model.
10 Factors Warehouse Managers Should Consider for Goods-to-Person Fulfilment
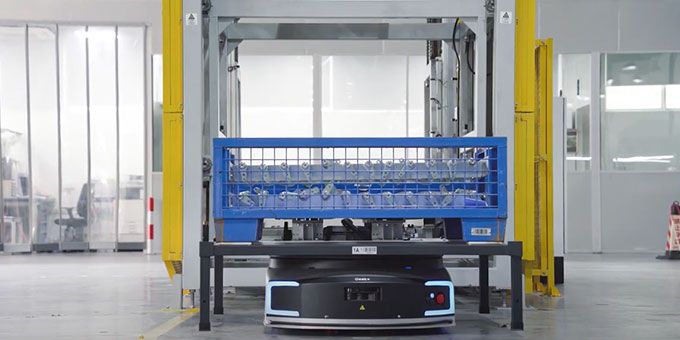
Article from | Geek +
Propelled by market shifts such as the rise of e-commerce, as well as growing consumer demand for just-in-time ordering, fulfillment centers around the globe face an inevitable pressure to deliver goods faster than ever. As a result, the traditional model of fulfillment, commonly known as Person-to-Goods picking, struggles to keep pace with the speed and accuracy necessitated by businesses worldwide. In response, many fulfillment operators have transitioned to the Good-to-Person(GTP) model to meet those needs.
In this article, let's dive deeper into how it works and what factors you should consider if you are thinking to switch to using the Goods-to-Person fulfillment model.
What is Goods-to-Person Fulfilment?
In a Goods-to-Person(GTP) environment, human workers remain at their workstations while a software-driven Automated Storage and Retrieval System (ASRS) retrieves, conveys and delivers required SKUs via totes, trays etc., directly to pickers, packers, shippers and replenishers. The mode of fulfilment eliminates unnecessary walking between warehouse aisles and reduces potential human errors, thereby fortifying both efficiency and precision.
How does Goods-to-Person Picking work?
1. Decanting workstations receive inventory where operators scan bar codes and transfer items into inventory totes
2. Inventory totes are conveyed and automatically stored in a high-density storage buffer
3. Inventory totes are retrieved when required and directed to picking stations
4. Operators are directed by lights and graphical instructions to pick the required items from the inventory totes and place them into order containers
5. After fulfillment of an order container, it is automatically routed to the packing area
6. Inventory totes return to the high-density storage buffer
Does my business need Goods-to-Person Fulfilment? Here are 10 Factors to Help Weigh Your Decision
Order Picking Travel Time
One of Goods-to-Person(GTP)’s highlights, strongly touted by its advocates, is how employees in Goods-to-Person(GTP) operations do not have to move at all – all work is directed to their workstations, hence eradicating travel time, improving individual productivity, and minimizing full-time equivalent (FTE) requirements. This is especially beneficial for organizations managing massive numbers of SKUs or with large facilities, as compared to operations with small facilities or very densely slotted pick engines.
System Scalability
Goods-to-Person(GTP) operations are highly scalable and in view of majorly fluctuating business demands, growth, and SKU proliferation, such flexibility is essential to safeguard the sustained efficacy of the business’ order fulfillment system. Well-devised Person-to-Goods(PTG) systems can also be engineered to scale easily. In deciding which is more optimal for your business, what additional labour requirements and capital investments are required should be taken into account. Additionally, businesses should factor in their equipment throughput limitations since that would impact the possibility of system bottlenecks after scaling up.
Order Accuracy
Goods-to-Person(GTP) automated retrieval systems are designed to directly deliver the correct product to pickers’ workstations, reducing opportunities for mispicks. As such, Goods-to-Person(GTP) system providers often regard increased accuracy as a major differentiator for their technologies. This is not unfounded as real-world data confirms that most Goods-to-Person(GTP) systems routinely exceed 99-plus percent order accuracy. Yet, comparable levels of accuracy can similarly be achieved by Person-to-Goods(PTG) order picking driven by Pick-To-Voice (PTV) or Pick-to-Light (PTL). Businesses should note that exceptional high order accuracy stems from quality system design, technologies, and well-trained employees, regardless of the type of fulfillment method deployed.
Smaller Footprint & Better Space Utilization
Since automated retrieval systems can be more condensed horizontally in Goods-to-Person(GTP) systems, a smaller footprint is realized. The true benefit of Goods-to-Person(GTP) operations, however, is unparalleled vertical space utilization. ASRS systems can be constructed up to 100 feet high, effectively economizing and utilizing previously inaccessible vertical space. Henceforth, the higher a building’s clear height, the more its operations will benefit from Goods-to-Person(GTP) Distribution Center (DC) cube utilization.
Single Point of Failure
Goods-to-Person(GTP) ASRS technologies are exceedingly productive and expeditious, but in the event of a calamitous mechanical or software mishap, manual access to inventory contained within can be almost impossible. If this failure is concurrent with a peak period, the debilitation of order fulfillment can negatively impact an organization’s profitability and long-term customer retention. In comparison, inventory accessibility of automated PTG systems can allow more operational flexibility even in times of system failure.
Productivity Optimization
In terms of productivity rates, Goods-to-Person (GTP) environments seem to fare better than most efficient PTF automated operations but there are further factors for consideration. For example, Goods-to-Person(GTP) order fulfillments require pickers to transfer picked items from totes/bins into shipper cartons and this process entails supplementary labour, thereby impacting overall fulfillment productivity. Moreover, an organization’s SKU movements and order profiles are imperative – if a business’ order profiles are inclined towards a relatively small quantity of high volume “hyper-mover” SKUs, GTP’s ASRS system can utilize batch picking to simultaneously fulfill multiple orders requiring that particular SKU and attain improved productivity.
Capital
Due to the level of automation, equipment, and software needed for fully automated Goods-to-Person systems, they are considerably more expensive than automated PTG systems. However, despite the differential initial capital expenditure, GTP systems are capable of generating favourable ROI when considering potential labour efficiencies, real estate savings, and life cycle costs.
Business Seasonality
Peak periods are crucial points for businesses to capitalize on.Goods-to-Person systems can be flexibly scaled up when required to help businesses effectively accommodate seasonal spikes in order volumes. Of course, implementing a highly automated Goods-to-Person(GTP) system in a situation where the organization only experiences drastic peaks one to three times a year may lead to underutilization. In contrast, since Person-to-Goods(PTG) operations are more closely tied to labour rather than automated hardware, the amount of labour can be more flexibly adjusted to business demands. It may be thus more financially viable for operations that experience seasonal spikes in order volumes and have access to sufficient labour pools to select an optimal Person-to-Goods(PTG) picking system.
Ergonomics
Goods-to-Person workstations are often designed for exceptional ergonomics that enable employees to perform job functions with safe postures and well-choreographed movements. In addition, since the need for lifting and carrying SKUs by pickers is significantly reduced compared to PTG systems, Goods-to-Person(GTP) operations can reduce warehouse injuries and in turn, improve workplace safety, productivity, and employee job satisfaction.
Product Sequencing
Goods-to-Person(GTP) systems can provide intelligent picking services like smart product placement within an order container to accommodate weight distribution as well as grouping by product category etc. to take business operations optimization to another notch.
Siemens Switchgear Shanghai had considered these factors when the company was deciding whether or not to invest in automation. As the company experienced a surge in demand for customized equipment, their priority was to relieve the strain on its already complex production process and resolve operational issues like inefficient storage of raw materials, labor-intensive material handling, and low visibility of the production process. In response to Siemens' needs, Geek+ introduced an AI-driven robotics solution to realize a more dynamic and efficient production process in Siemens Shanghai factory. The result was palpable - with 2-3 times more storage capacity, 99.99% accurate operations, 2.5 times storing efficiency, outbound collection process improved by 2.15 times, and 30% less manual labor needed.
In conclusion, we hope that breaking down what Goods-to-Person(GTP) fulfillment is and the accompanying multitude of factors to consider can better aid your business in deciding whether Goods-to-Person(GTP) is suitable for your operations. To learn more about Geek+’s avant-garde Goods-to-Person(GTP) systems and solutions, contact our consultants today!
The content & opinions in this article are the author’s and do not necessarily represent the views of RoboticsTomorrow
Comments (0)
This post does not have any comments. Be the first to leave a comment below.
Featured Product
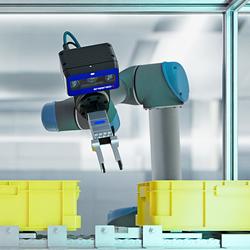