Fully Autonomous Hamburger Line
Watch PBS NOVA Episode "Rise Of The Drones"
Adept's New Material Automation Robot
Filling A Room With Single-line Drawing
Swarm Of Pingpong-Ball-Sized Robots
OpenBeam
New Lego Mindstorm EV3 With Linux-based OS
NASA Kicks Off 2013 First Robotics Season With Live Broadcast Jan. 5
60 Minutes Segment On Brain Controlled Robotic Limbs
New AlphaDog Field Test Footage
New Arduino Esplora With Built-in Onboard Sensors
iRobot Co-founder's New Company And Product Unveiled
Liquid Robotics' Marine Robot Completes 9,000 Mile Record Breaking Journey
Disney Research Papers On Robotics
Lehmann Aviation's LA100 UAV
Records 766 to 780 of 920
First | Previous | Next | Last
Industrial Robotics - Featured Product
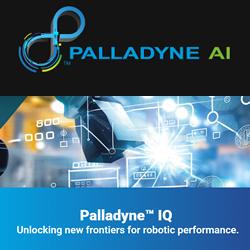