THIS WHITE PAPER discusses how manufacturers in many industries are leveraging collaborative robots (cobots) to create safe zones for workers returning to production lines.
COBOTS VS COVID: Today’s Manufacturing Reality and Tomorrow’s New Normal
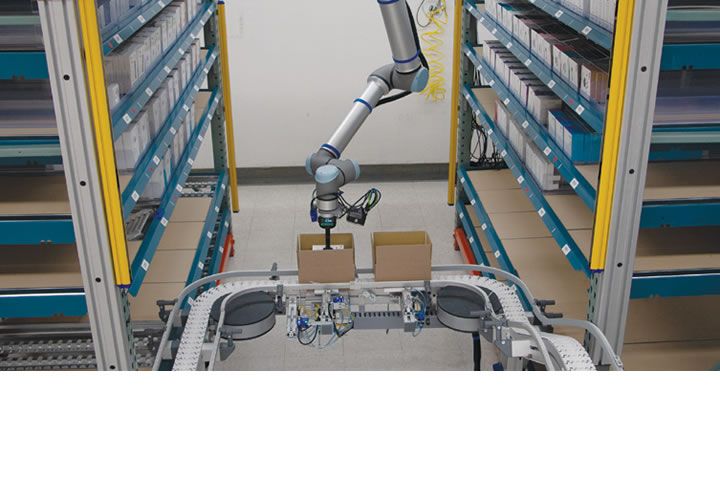
White Paper from | Universal Robots
As countries around the world get back to “normal’ operations following the COVID-19 shutdowns in early 2020, leaders struggle to create the new normal, where people feel safe and employees can return to work safely and with confidence. Thankfully, manufacturing companies have help when it comes to creating new operational plans. Organizations such as the National Association of Manufacturers (NAM) and analyst firm McKinsey & Company are providing guidance both big — such as requesting governments to update digital infrastructure and encouraging reshoring of manufacturing operations — and small, such as leveraging automation to “drive productivity at a distance.”
Manufacturing the ‘New Normal’
In the second week of March, just days after the first U.S. state issued a stay-at-home order, nearly 80% of U.S. manufacturers expected to take a financial hit from the pandemic, while more than half anticipated that they would need to change their basic operations, according to NAM. Take electronics manufacturing, for example. It takes hundreds of workers to make a single cell phone. Traditionally, workers assembling electronic devices stood at 2-foot intervals along the production line. Obviously, that spacing will have to be significantly increased to maintain 6-foot safe zones around each mask-wearing employee. Interspersing cobots among the assembly workers allows manufacturers to create the necessary safe zones.
To learn how Manufacturers are leveraging collaborative robots
(cobots) to create safe zones for workers returning
to production lines, read this Universal Robots White Paper, “COBOTS VS COVID: Today’s Manufacturing Reality and Tomorrow’s New Normal”.
The content & opinions in this article are the author’s and do not necessarily represent the views of RoboticsTomorrow
Comments (0)
This post does not have any comments. Be the first to leave a comment below.
Featured Product
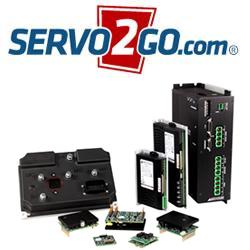