RobotsTrader.com Launches as Premier Marketplace for Buying and Selling Used Robots
Warehouse Robotics Company, Contoro, Achieves New Milestone, Surpassing 100 Trailers Unloaded Autonomously With Its AI-Powered Robot
High-Throughput PIC Production Needs Precision Alignment Equipment for Photonics Arrays, Fibers, Lenses
The most sensitive and durable robot hand yet created
Understanding Torque and Speed in Electric Motors
Trend 2025: Energy requirements often depend on the size of the AI model
Top 5 trends for the AIoT industry in 2025
Automation and Robotics Can Help Address Worker Efficiency While Delivering Business Results Through Smart Construction
MassRobotics Opens Applications for Third Annual Form and Function Robotics Challenge
Celebrating10 years of Innovation in Robotics
How Robot Sensors Are Powering a USD 5 Billion Revolution by 2032
Jasper Group Using AMRs for Material Handling
IEEE Reveals Predictions for Top Technology Trends of 2025
Exploring the Future of Supply Chain in 2025
Dürr equips first BYD plant in Europe with sustainable painting technology
Records 121 to 135 of 3630
First | Previous | Next | Last
Featured Product
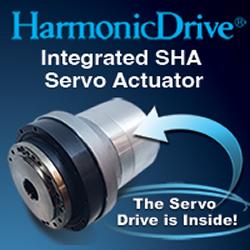