SCARA Robot Sorts Recyclables Using a Simple Conveyor Speed Feedback System
As Everest Labs was developing their system to be sold to recycling centers worldwide, they found that their robot needed speed feedback in order to track the recyclables on the conveyor, and therefore needed a simple way to install conveyor speed feedback on a gear motor.
Choosing the Right Encoder for Your Robot
Most robots use servo motors to move their joints, calling for rotary or angle encoders. As speeds increase, so do the control dynamics the motors require, sometimes making vibration mitigation just as important accuracy and resolution.
US Digital Automates Production Process Using Robot and In-House Engineering Talent
When US Digital released the E4T Miniature Optical Kit Encoder it needed to update manufacturing procedures to better handle the miniaturized encoder disks. The company decided to use automation and built the delta robot system above.
Industrial Robots: Encoders for Tool Center Point Accuracy
The use of secondary encoders on all of a robots axes, as well as the use of linear encoders for positioning the robot relative to the workpiece, enables a level of accuracy at the tool center point
Encoder Selection: Speed Control
A general in depth analysis shows that the highest encoder resolutions are required for very precise speed control. The encoder resolution increases with the square of the demanded speed accuracy.
Tru-Tracâ„¢ Keeps Frankenstein Alive
This machine was assembled from various parts from other machines, so "Frankenstein" was really the only logical name for it.
What IS an Encoder?
Encoders use different types of technologies to create a signal, including: mechanical, magnetic, resistive and optical - optical being the most common.
Records 1 to 7 of 7
Featured Product
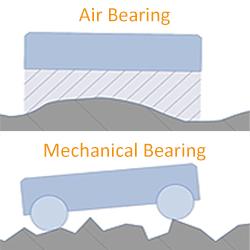
PI USA - Multi-Axis Automation
Choice of components to suit application requirements +++ Easy to set-up +++ Functional safety +++ Base plate, mounting bracket, wide range of accessories +++ Short lead time +++ Preconfigured with cable management +++ Delivery includes alignment, adjustment, calibration and detailed test reports +++ On-site support by engineering and application experts