Revolutionizing Warehouse Floors: How AGVs & AMRs are Driving Safety in Modern Manufacturing
With automated systems, the possibilities for implementation are endless, but depending on your business goals and needs, automated guided vehicles (AGVs) and autonomous mobile robots (AMRs) prove to be particularly impactful.
AGV and AMR Are Becoming More Complex
To enable the industry to keep pace with trends through quick and cost-efficient development, Markus Fenn and Prof. Dr. Stefan May developed Eduard, a teaching and prototyping platform that can be used to map current trends.
What Are The Differences Between Safe LiDAR and LiDAR?
One of the key elements to consider when selecting LiDAR technology is whether you need safe LiDAR or LiDAR. But what makes LiDAR safe? And when do you need a safety-rated device? Well, look no further, we've got the answers for you right here!
Delica Drives Efficiency with AGV Installation
Delica selected a Stöcklin AGV with BlueBotics' ANT navigation technology to automate their materials handling between production and logistics.
Kivnon AGVs Drive Efficiency for Forvia
Forvia, one of the world's leading automotive manufacturers, completes a successful AGV installation at its factory in Paraná, Brazil.
Forklift Safety: AGVs to the Rescue
As a relatively new addition to site operations, standards and data on AGV safety are still developing, but some AGV manufacturers are going above and beyond the minimum requirements to help ensure accident-free operations.
Investing in AGVs or AMRs? 6 Ways Engineered Mezzanine Flooring Maximizes Implementation Success
Having the wrong elevated flooring surface - such as concrete, which frequently has uneven surfaces, cracks, and spalling - can significantly hamper the function and productivity of AGVs and AMRs.
Warehouse Robots and Why Flooring is Important
One of the best ways today to improve business efficiency is through the use of warehouse robots. And while planning is underway to adopt warehouse robots, it's important to consider the most ideal flooring.
Why Do AGVs Need Reliable Motors?
Any automated system is only as good as its reliability. An automated guided vehicle (AGV) for example, needs to do the job it is programmed to do; without error, quickly and efficiently.
AGV or Conveyor - Which System Should You Choose?
Material logistics plays a crucial role in manufacturing processes and warehouses, but should a company choose an autonomous guided vehicle (AGV) or a conveyor system? Leaders in intralogistics solutions give their opinions on when and why each technology can make sense.
Most Accurate Lotus Car Ever, Thanks to Cutting Edge Metrology
The CMM installed in Hethel is set one meter into the floor on a special foundation. It means that a car for inspection carried on an automated guided vehicle (AGV) is able to access the area without the need for any lifting equipment.
AGV and AMR Technology: Solving Your Internal Logistics Challenges
AGV's and AMR's address a number of key manufacturing process and facility-related concerns as well as key cost-related metrics in the migration towards continuous improvement philosophies such as lean manufacturing and six sigma.
Following the Path to AGV Safety
Although automated guided vehicles (AGVs) are, by definition, designed to run autonomously, they usually need to collaborate with people and therefore move, and react, in a safe, predictable manner.
The Imperative to Automate to Relieve Labor Constraints: The Reason to Attend the Automate Show
Because there is such a shortage of fork truck drivers for the foreseeable future, automation has become an imperative. The only alternative is to automate bringing loads of finish goods (or sub-assembly) from docks to warehouses and warehouse to docks.
What's the Difference Between AGVs and AMRs?
We have been hearing a lot about AGVs and AMRs in warehouses and fulfillment centers. But do you understand the differences between these two? Let's find out from the experts.
Records 1 to 15 of 46
Featured Product
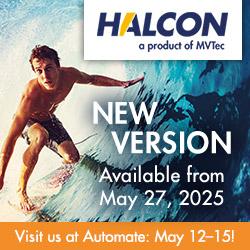
Next-Level Vision with HALCON 25.05
HALCON 25.05 sets new standards for machine vision, introducing Deep 3D Matching for robust bin picking, enhanced OCR accuracy, improved QR code reading on curved surfaces, and smarter camera integration. Meet MVTec at Automate Detroit and experience how the latest deep learning technologies and development tools empower you to create faster, more reliable, and flexible industrial solutions.